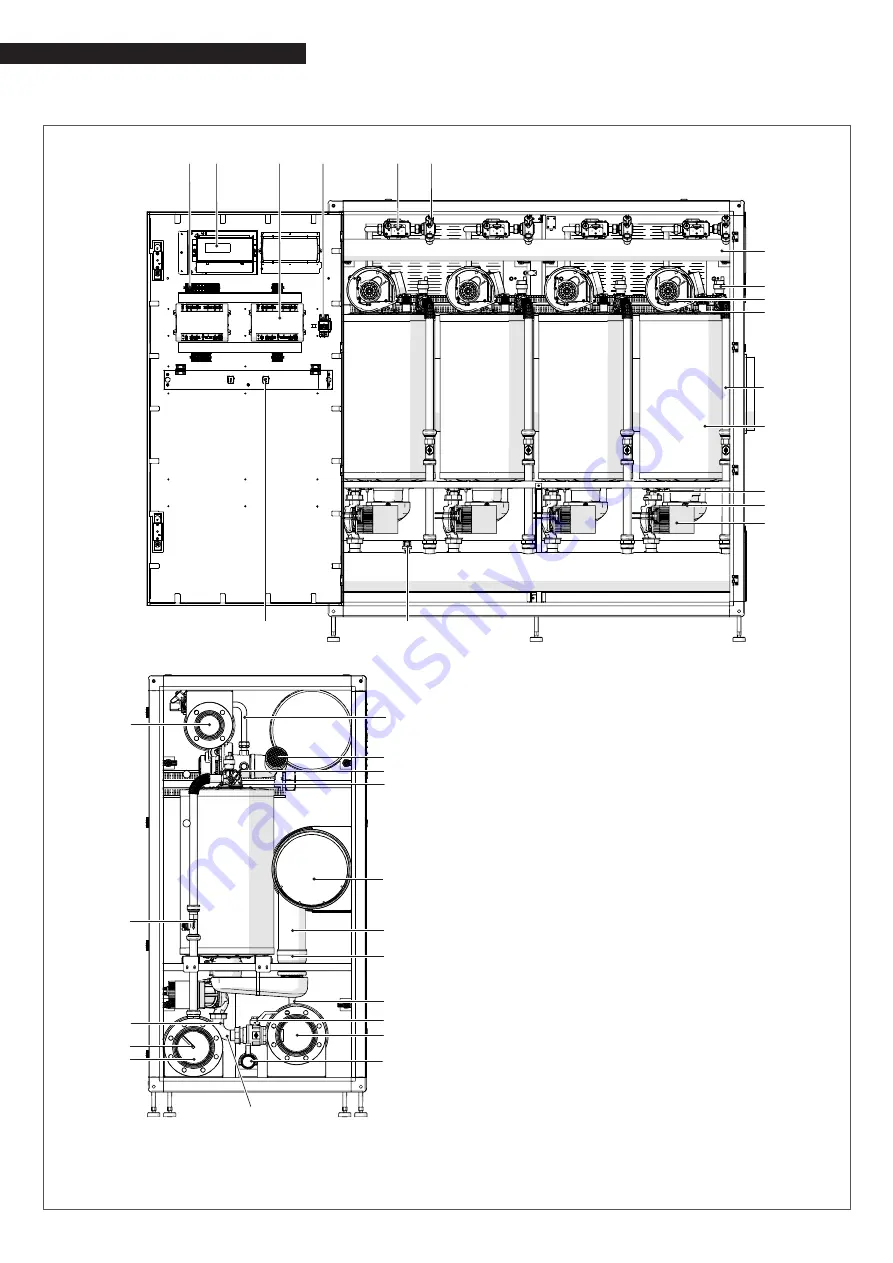
8
GENERAL INFORMATION
Steel Pro Power 300-3 P/V ÷ 540-4 P/V
1
2
30
33
32
31
29
4
5
3
8
10
9
28
12
27
13
3
25
26
14
11
22
23
24
21
18
19
20
15
16
6
7
17
1
Gas valve
2
Gas cock
3
Gas manifold
4
Fan
5
Electrode
6
Flow probe
7
Safety thermostat with reset by the board
8
Automatic bleed valve
9
Delivery pipe unit
10
Combustion chamber
11
Flow-meter
12
Unit return probe
13
Minimum pressure switch
14
Unit drain valve
15
Gas pipe unit
16
Unit inlet pipe
17
Flue Manifold
18
Flue exhaust pipe unit
19
Clapet unit
20
Condensate drain unit
21
Return pipe unit
22
Two-way valve return unit
23
Water return manifold
24
Condensate collector
25
Water flow manifold
26
Delivery probe socket
27
Unit pump / 2-way valve
28
Exhaust flue probe
29
unit switch
30
Control board
31
Terminal strip
32
Display
33
Mains power switch