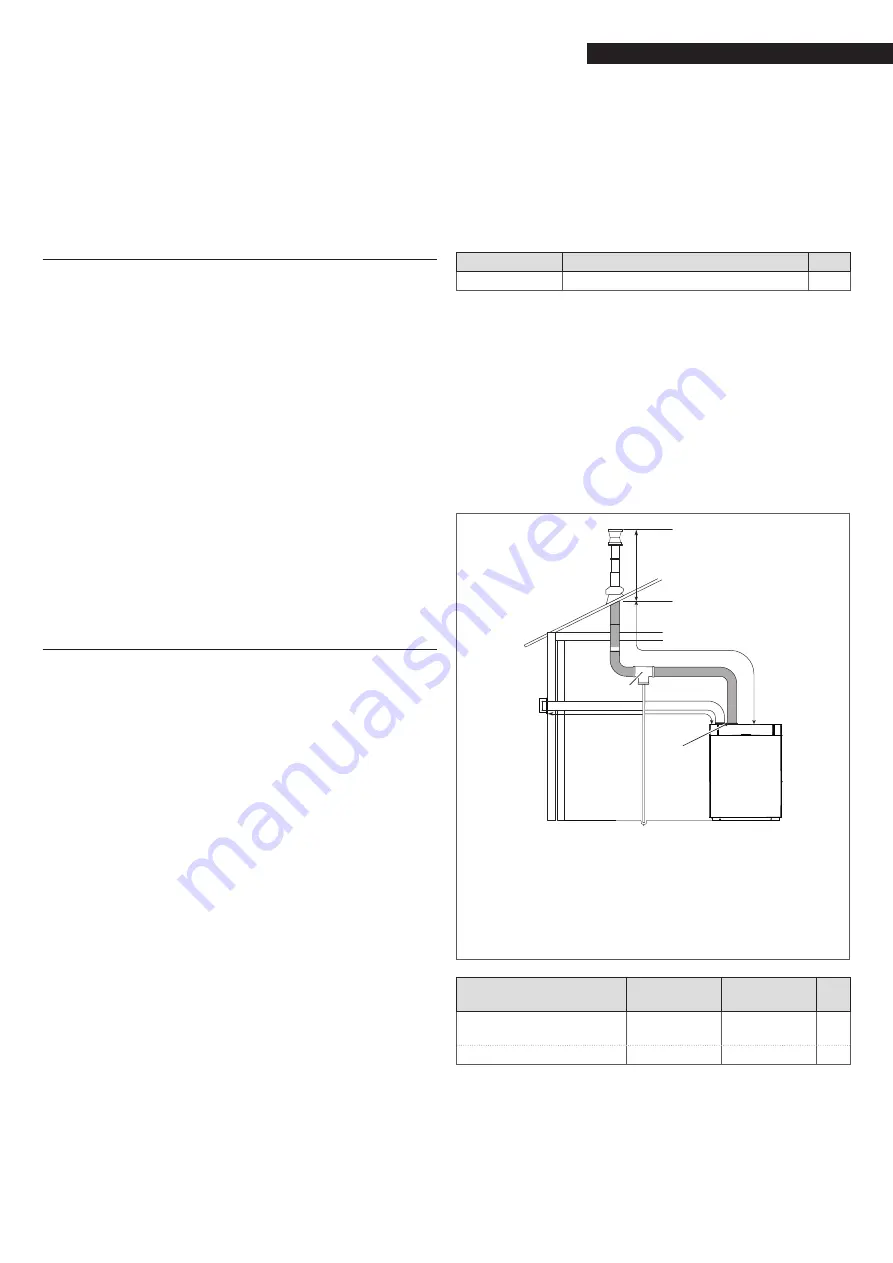
21
INSTALLATION
INSIEME EVOe K LN
boilers derive their comburent air from the
room in which they are installed. Suitable air vents must there-
fore be provided in compliance with applicable laws and stand-
ards.
0
Do not obstruct or restrict the air vents in the room where
the boiler is installed. Adequate ventilation is essential for
correct combustion and functioning.
2.10.1
Technical specifications of stack
The stack must satisfy the following requirements::
− It must be constructed from materials that are imper-
meable to flue gases and that offer lasting resistance to
mechanical stress, heat and the action of the products of
combustion and condensate
− It must be vertical, free of restrictions and contain bends
of no more than 45°
− It must be suitable for the specific operating conditions
of the boiler and must be CE marked
− It must be of adequate dimensions to ensure draught
and venting properties suitable for the needs of the boil-
er
− It must have adequate external insulation to prevent
condensation and the cooling of flue gases
− the stack must have a dedicated condensate drain sys-
tem at the bottom.
9
The diameter of the stack must never be smaller than that of
the flue pipe from the boiler.
9
In configuration B23, the stack must guarantee the mini-
mum draught specified by applicable technical standards,
assuming zero pressure at the boiler's flue gas exhaust.
2.10.2
Connection to the stack
The boiler must be connected to the stack using rigid flue pipes
that are resistant to heat, condensate and mechanical stress. All
joins must be sealed and the finished flue must be insulated.
Only use materials that are suitable for this purpose, e.g. stain-
less steel.
The near-horizontal section of flue pipe must have a slope of at
least 5° towards the boiler and must also be properly insulated.
In long near-horizontal sections of flue pipe (L>1 m), install a
condensate drain system near the boiler exhaust (as shown in
the figure) to drain off any condensate forming in this section
of flue.
The diameter of the stack must always be greater than that of
the flue pipe from the boiler's exhaust fitting. To change direc-
tion, use a T section with an inspection cap to permit easy access
for cleaning inside the pipe. After cleaning, always make sure
that inspection caps are replaced tightly and that their seals are
undamaged and efficient.
9
Flue pipes must maintain a distance of at least 500 mm
from flammable or heat sensitive construction materials.
9
Joins must be sealed with materials that are resistant to
acid condensate and to the high temperatures of the boil-
er's flue gases.
9
When installing flue pipes, always bear in mind the direc-
tion of the flue gases and of possible condensate flows.
9
Inadequate or badly dimensioned stacks and flues can in-
crease combustion noise, cause condensation problems
and affect combustion parameters.
9
Uninsulated flues are potentially dangerous and can cause
burns.
"OPEN" CONFIGURATION OF THE TYPE B BOILER
The equipment is supplied as standard in type B configura-
tion, hence prepared to suck air directly in the installation room
through the venting openings, that must be carried out in com-
pliance with the Technical Standards.
It can become a type C equipment with the use of specific ac-
cessories. In this configuration the equipment will suck air di-
rectly from the outside with the possibility to have coaxial or
split pipes.
Description
INSIEME EVOe K LN
L
MAX
20 (*)
m
(*)
This length must be reduced by 1 metre for every 90° curve
and by 0.5 metres for every 45° curve.
BOILER CONFIGURATIONS C “SEALED”
If comburent air is drawn from outdoors, the appliances are type
C "sealed" and the boiler room does not require ventilation.
Twin pipes (Ø 80 air / Ø 80 flue gases)
For these configurations, the type C transformation accessory
must be installed (following the instructions supplied with the
accessory itself).
Split ducts can be oriented in the direction most suitable to the
room needs, respecting the specified maximum lengths.
1 m
T
G
L
L
A
C
A
Type C transformation accessory
C
Condensation exhaust system (not supplied)
G
Protective grille (not supplied)
T
Terminal
L
Maximum straight length
(This length must be reduced by 1 metre for every 90°
curve and by 0.5 metres for every 45° curve.)
Description
INSIEME EVOe
25 K LN
INSIEME EVOe
32 K LN
L
MAX
Flue gas vent and
comburent air intake
20 (*)
30 (*)
m
L
MAX
Air inlet
10 (*)
15 (*)
m
(*)
This length must be reduced by 1 metre for every 90° curve
and by 0.5 metres for every 45° curve.