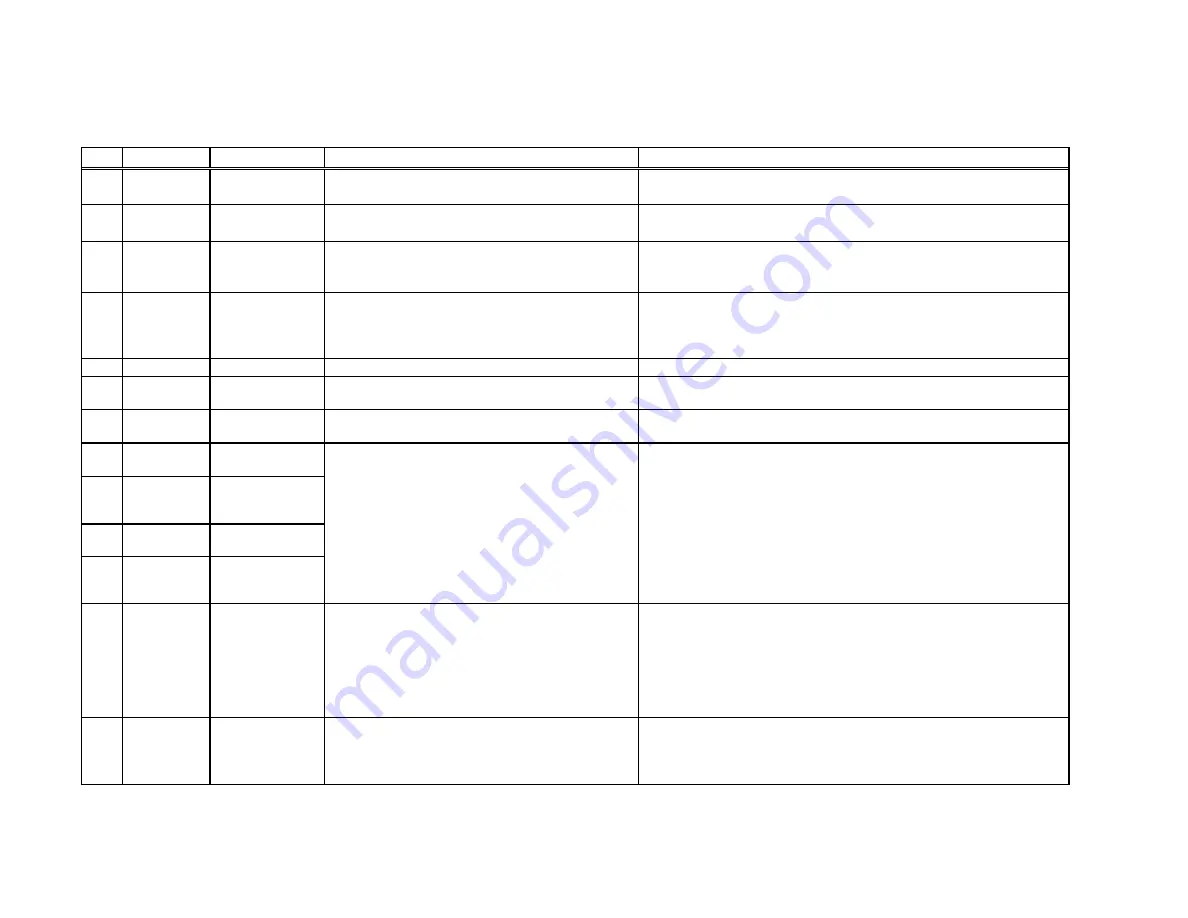
Ishida OMNi-4000 Error Codes and Troubleshooting
15.4a SERVO CONTROLLER ERROR CODES (0430 - 0011~0097)
The Lift Servo has built-in protection. When an error occurs the error code is displayed on the 7-segment display.
CAUTION
: These manufacturer's codes are provided as reference only and may have no bearing on the Ishida OMNi-4000 wrapper.
No.
Number*
Protection
Symptom or Phenomenon
Check
0430
11
Under voltage,
control power
Power voltage drops due to instantaneous power
failure or short capacity of power supply.
Check if power voltage is within permissible voltage range.
0430
12
Over voltage,
main power
Convertor voltage increases due to regenerative
energy. For 200V mode: 400VDC or more.
Increase the deceleration time or lower the load inertia.
Note
: Not applicable when the regenerative brake is used continuously.
0430
13
Under voltage,
main power
Power voltage drops due to instantaneous power
failure or short capacity of power supply.
Check if power voltage is within permissible voltage range.
Note
: Be careful of short power capacity, voltage drop due to rush
current at power ON, and open-phase of the power supply.
0430
14
Over current error Convertor output current is abnormally high.
1. After power supply is completely shut off, check if motor connection
wires U, V, W are short circuited together.
2. Check insulation resistance between connection wires U, V, W and
Ground, and check if motor insulation is compromised.
0430
15
Over heat error
Servo Driver power elements are abnormally heated. Check Servo Driver ambient temperature and cooling conditions.
0430
16
Over load error
Servo Driver is continuously operated exceeding the
rated current.
Increase acceleration/deceleration time or lower the load. Increase
motor and Servo Driver capacity.
0430
18
Regenerative
discharge error
Regenerative energy exceeds the permissible
regenerative discharge resistor value.
Connect external regenerative discharge resistor.
0430
20
Encoder A/B-
phase error
0430
21
Encoder
Communication
error
0430
22
Encoder
connection error
0430
23
Encoder
Communication
data error
0430
24
Position error
Position error pulse is exceeding the permissible
range set by parameter No. 63 (Position error limit
setup)
1. Check if the motor runs according to the position command.
2. Use the torque monitoring function to check if the output torque
is saturated.
3. Set the torque to maximum value.
4. Check the gain adjustment.
5. If no problems are observed, increase acceleration/deceleration
time and lower the load to reduce the velocity.
0430
25
Protection against
hybrid deviation
error
In full closed control mode, the position of load by
external scale and the position of motor by encoder
differ by more than pulse number set by parameter
No. 73 Hybrid deviation error.
1. Check the connection between the motor and the load.
2. Check the connection between the external scale and the
servo driver.
Encoder line has trouble such as disconnection.
Encoder is defective.
1. Check if encoder connection has any trouble and check the
connected state at connector [X4].
2. Check the power voltage (5V ± 5%) on the encoder side.
Rev. Feb 2015
21/
40
Yellow highlights indicate updates