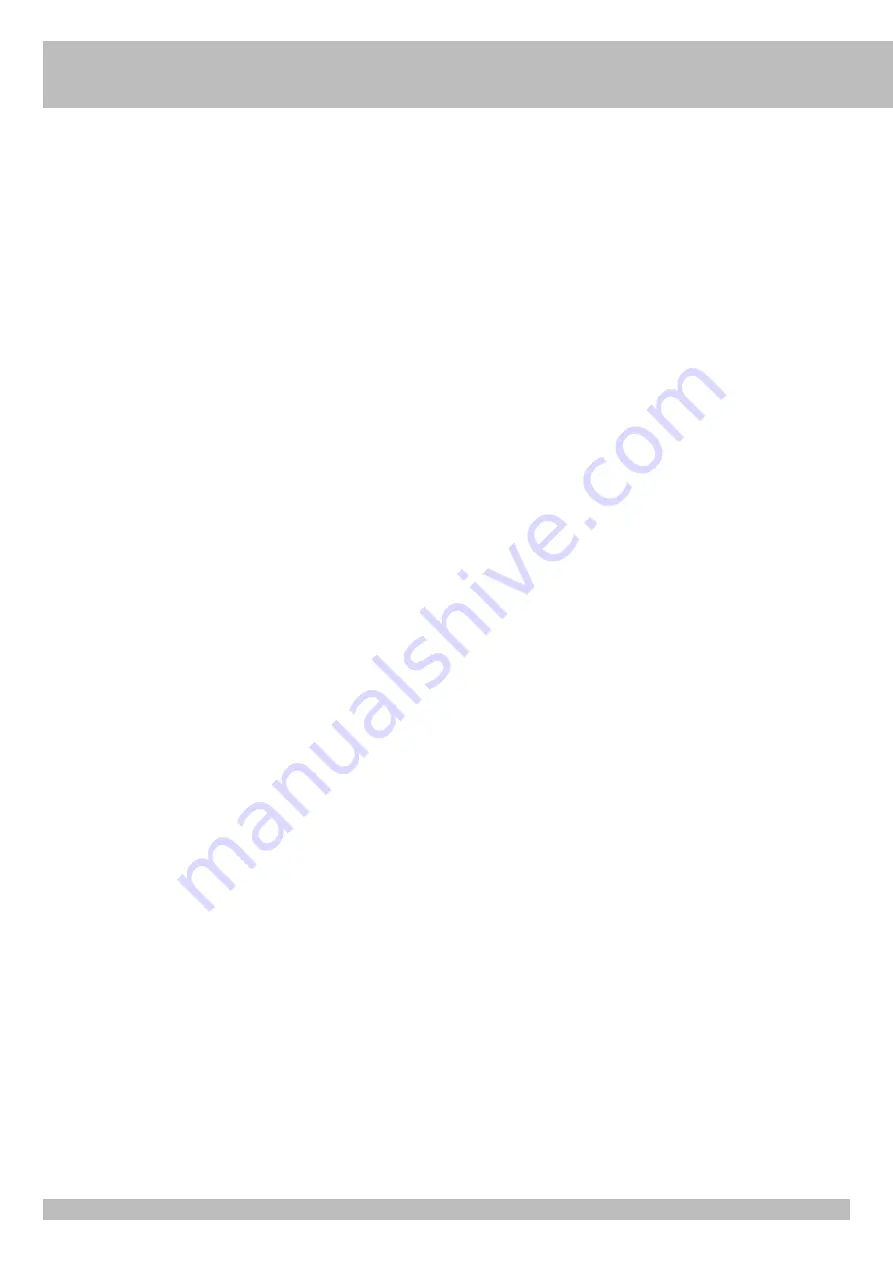
43
out with a total delay between the two gate leaves. Therefore, first the leaf M2 will close
completely; once it is OFF, M1 will start closing. This separate movement of the two gate leaves
is done to avoid their incorrect overlapping.
HEATER ONLY FOR KING ICE and KING EVO ICE
The in-built thermal sensor of the KING EVO ICE motor can be connected to the terminal block J11
on the B2 control board. For the connection details please refer to the KING EVO ICE Instruction
Manual.
The probe for motor heating is a device intended to be used in extremely cold environment (up
to -30°C) to avoid motor freezing.
Such device activates automatically when the gate is steady (the position being irrelevant,
provided it is not moving) at a ambient temperature motor inferior to 10°C (found from the
sensor of temperature PROBE).
The work of the heater is indicated by both the DL6 and DL7 leds for the motor number 1, and by
the DL4 and DL5 leds for the motor number 2.
When the motor is running the heating system is inoperative.
On elapsing of 10 s delay from gate stop, the heating system gets activated (in case the
environment temperature in the motor area is below 10°C).
Upon achieving a 20°C temperature the heating system deactivates, maintaining a constant
environment temperature.
PROBE TECHNICAL DATA
Operation voltage
5 Vdc
Resistance
10 KΩ ±2% (at 25°C)
Working temperature
-30 ÷ +55°C
TECHNICAL SPECIFICATIONS
- Temperature range
-10 ÷ + 55°C
- Humidity
< 95% without condensation
- Power supply voltage
230 V o 120 V~ ±10%
- Frequency
50/60 Hz
- Maximum absorption
45 mA
- Power supply microinterruptions
100 ms
- Maximum power SIGNAL output
24 Vdc 3W
- Maximum load of blinker output
40 W with resistive charge
- Current available for photocells and accessories 500 mA 24 Vdc
- Current available on radio connector
200 mA 24 Vdc
TECHNICAL RADIO SPECIFICATIONS (model B2-CRX)
- Reception frequency
433,92 MHz
- Impedence
52 Ω
- Sensitivity
>1 µV
- Feedback control
PLL
- Memory storage (codes)
1000
- All the inputs must be used as clean contacts because the power supply is generated
internally (safe voltage) in the card and it is set in a way to guarantee the use of the double
insulation and reinforced in relation to parts with hazardous voltage.
- Any external circuits connected to the outputs of the control board, must be carried out to
make sure the double or reinforced insulation is used in relation to parts with hazardous
voltage.
- All the inputs are run by a programmed integrated circuit which carries out a self-check at
the beginning of each operation.
TROUBLE SHOOTING
After having carried out all connections, by carefully following the layout and having positioned
the gate in intermediate position, check the correct ignition of red LEDS DL6, DL7, DL8, DL9
and DL10.
In case of no ignition of the LEDS, always with gate in intermediate position, check the following
and replace any faulty components.
DL6
OFF Stop button malfunction (if Stop is not connected, perform the jump
between COM A+ and STOP).
DL7 or DL8
OFF Faulty photocells (In case the edge is not connected, carry out jumper
between COM A+ and PHOTO 1/PHOTO 2)
DL9 or DL10
OFF Faulty safety edge (In case the edge is not connected, carry out
jumper between COM A+ and EDGE 1/EDGE 2)
During functioning with personnel present, with
DIP 1 to ON
, check that during opening of M1
and M2 the green DL2 and DL4 LEDS switch on and that during closing of M1 and M2 the red DL3
and DL5 LEDS switch on.
Or else, reverse the wires of the motor.
DL13 blue
ON
Some functions are enabled via smartphone, so via smartphone check
the card functions as the dips/trimmers status may not be true.
On the board there are resettable fuses which intervene in the event of a short circuit,
interrupting the output assigned to them.
In the event of troubleshooting, it is advisable to disconnect all the removable connectors and
insert them one at a time in order to more easily identify the cause of the fault.
G
B
Summary of Contents for AA14050
Page 75: ...75...