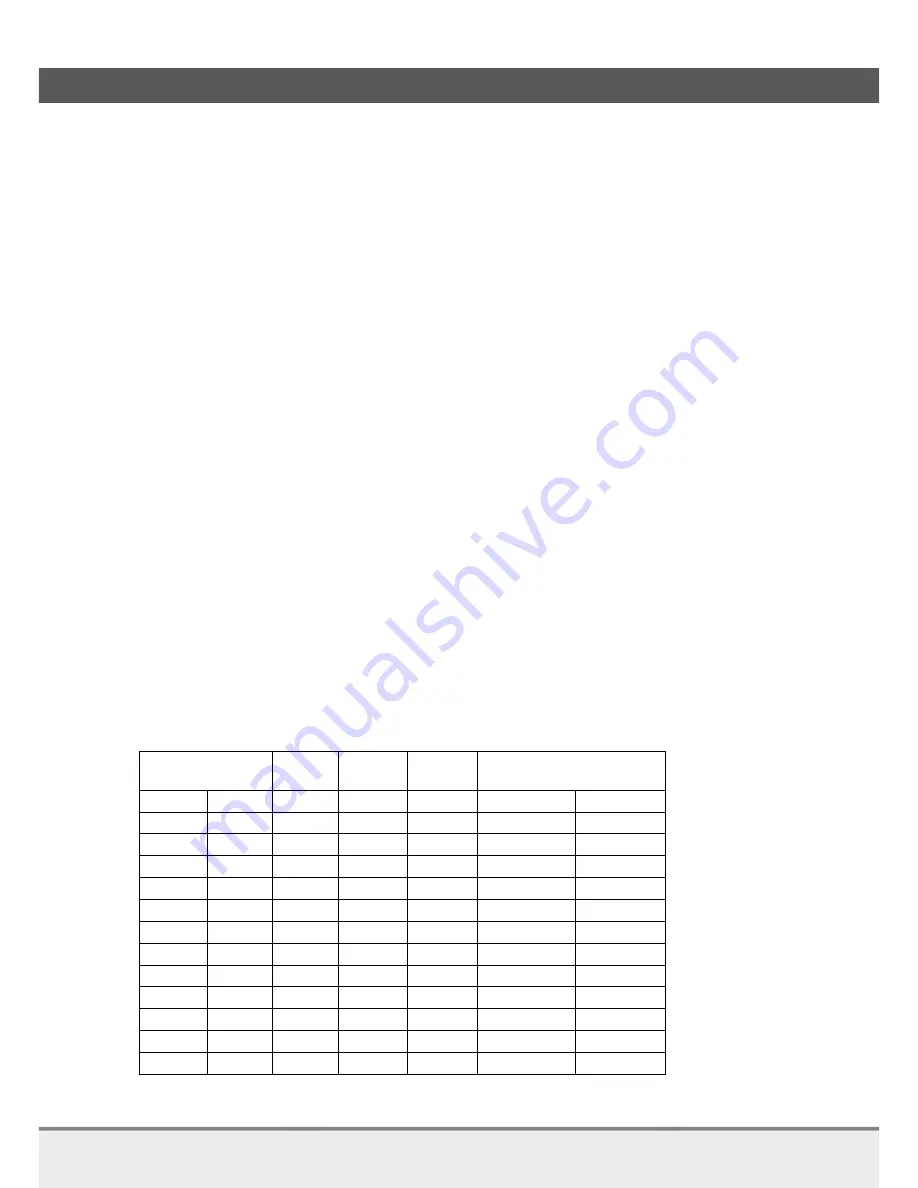
SDM – Slurry Density Meter
13
www.rhosonics.com
INSTALLATION
2.3.4
Instructions
1.
Carefully align the pipe sections with the spool in order to avoid stress at the flange surface of the
spool. In addition, the piping must be secured and supported to prevent movement which can
create excess stress and flange face damage.
2.
Once the gasket is in place, align the bolt holes of the spool and the adjacent flange faces
3.
Lightly lubricate and insert all bolts and washers and loosely apply the nuts
4.
Number all bolts for record purposes
5.
Make sure the faces of the mating surfaces are flush against gasket prior to bolting down the
flanges.
6.
Tighten the nuts by hand until they are snug. Establish uniform pressure over the flange faces by
tightening the bolts in increments up described as below.
2.3.5
4 and 8 Bolt Flanges
First round - 30% of final torque (flange sequential order, crisscross)
Second round- 60% of final torque (flange sequential order, crisscross)
Third round - 100% of final torque (flange sequential order, crisscross)
One final time after 24 hours - clockwise or counter clockwise sequentially around the flange
2.3.6
12 Bolt Flanges and More
First round - 20% of final torque (flange sequential order, crisscross)
Second round - 40% of final torque (flange sequential order, crisscross)
Third round - 80% of final torque (flange sequential order, crisscross)
Fourth round - 100% of final torque (flange sequential order, crisscross)
One final time after 24 hours - clockwise or counter clockwise sequentially around the flange.
In below table, torque values are given for Rhosonics metal spools (SDM-1) and metal wafers (SDM-4 or
SDM-5). These values assume the flanged joint connects the spool to a CLASS 150 flange. These values are
for Spiral Wound Gaskets, ASME B16.5.
Nom. OD
Bolt
hole
No.Bolts Size Bolts Preferred Torque per Bolt
(Inch)
(mm)
(mm)
M…
(ft lb)
(Nm)
3
80
19
4
16
120
163
4
100
19
8
16
120
163
5
125
22.2
8
18
200
271
6
150
22.2
8
18
200
271
8
200
22.2
8
18
200
271
10
250
25.4
12
22
320
434
12
300
25.4
12
22
320
434
14
350
28.6
12
24
490
664
16
400
28.6
16
24
490
664
18
450
31.7
16
27
710
963
20
500
31.7
20
27
710
963
24
600
34.9
20
30
1000
1356