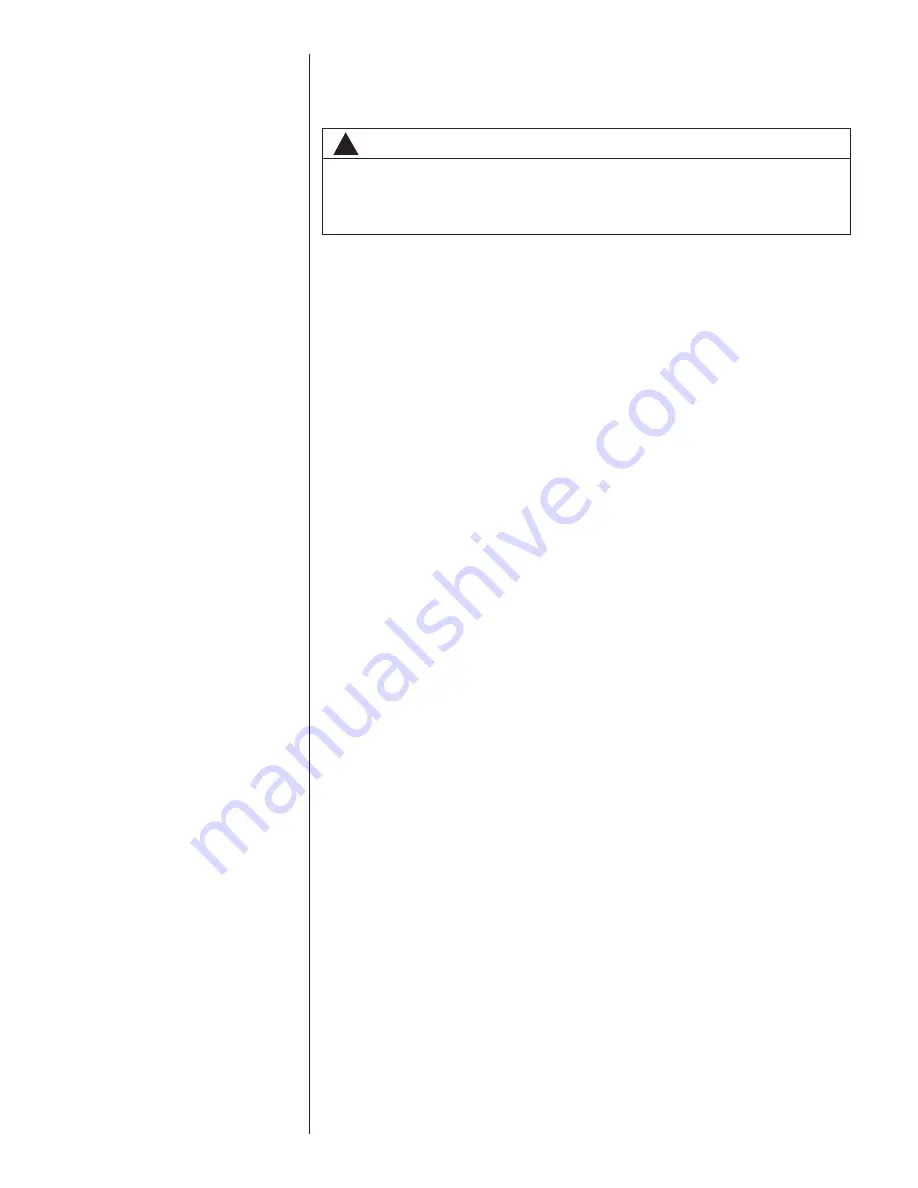
26
6.0 DUCTWORK
Field ductwork must comply with the National Fire Protection Association NFPA 90A,
NFPA 90B and any applicable local ordinance.
Sheet metal ductwork run in unconditioned spaces must be insulated and covered with
a vapor barrier. Fibrous ductwork may be used if constructed and installed in accor-
dance with SMACNA Construction Standard on Fibrous Glass Ducts. Ductwork must
comply with National Fire Protection Association as tested by U/L Standard 181 for
Class I Air Ducts. Check local codes for requirements on ductwork and insulation.
• Duct system must be designed within the range of external static pressure the unit is
designed to operate against. It is important that the system airflow be adequate.
Make sure supply and return ductwork, grills, special filters, accessories, etc. are
accounted for in total resistance. See airflow performance tables in this manual.
• Design the duct system in accordance with “ACCA” Manual “D” Design for
Residential Winter and Summer Air Conditioning and Equipment Selection. Latest
editions are available from: “ACCA” Air Conditioning Contractors of America, 1513
16th Street, N.W., Washington, D.C. 20036. If duct system incorporates flexible air
duct, be sure pressure drop information (straight length plus all turns) shown in
“ACCA” Manual “D” is accounted for in system.
• Supply plenum is attached to the 3/4” duct flanges supplied on the unit around the
blower outlet. Flanges are flat for shipping purposes and must be bent up along per-
forated edge around blower opening. Be sure to bend flanges completely up so they
do not interfere with air being discharged from blower.
IMPORTANT: Flanges around blower opening for attaching supply duct must be up out
of blower discharge even if not used so they do not restrict airflow from blower.
IMPORTANT: If an elbow is included in the plenum close to the unit, it must not be
smaller than the dimensions of the supply duct flange on the unit.
• Some units with electric heaters require 1 in. clearance to supply plenum and branch
ducts to combustible material for the first 3 feet from the unit. See CLEARANCES.
• A 3/4” return duct flange is supplied on all sides of the air inlet opening of the unit coil
casing. If the unit is to be installed without a coil casing (no indoor coil), a 3/4”flange
is supplied on the back and sides of the air inlet opening of the blower casing. No
flange is provided on the front of the opening to the blower casing. If return duct is
attached to the inlet of the blower casing, the front flange of the duct should be run up
into the opening or 90° brake made on the front flange to tape to the front of the blow-
er casing.
• IMPORTANT: The front flange on the return duct if connected to the blower casing
must not be screwed into the area where the power wiring is located. Drills or sharp
screw points can damage insulation on wires located inside unit.
• Return duct flanges on blower or coil casing are flat for shipping purposes and must
be bent out along perforated edge around opening.
• Secure the supply and return ductwork to the unit flanges, using proper fasteners for
the type of duct used and tape the duct-to-unit joint as required to prevent air leaks.
!
WARNING
Do not, under any circumstances, connect return ductwork to any other heat
producing device such as fireplace insert, stove, etc. Unauthorized use of
such devices may result in fire, carbon monoxide poisoning, explosion, per-
sonal injury or property damage.
Summary of Contents for RHPL-HM2421JC
Page 37: ...37 FIGURE 29 AIR HANDLER EQUIPPED WITH Serial Communication WIRING DIAGRAM...
Page 38: ...38...
Page 39: ...39...
Page 40: ...40 CM 0411...