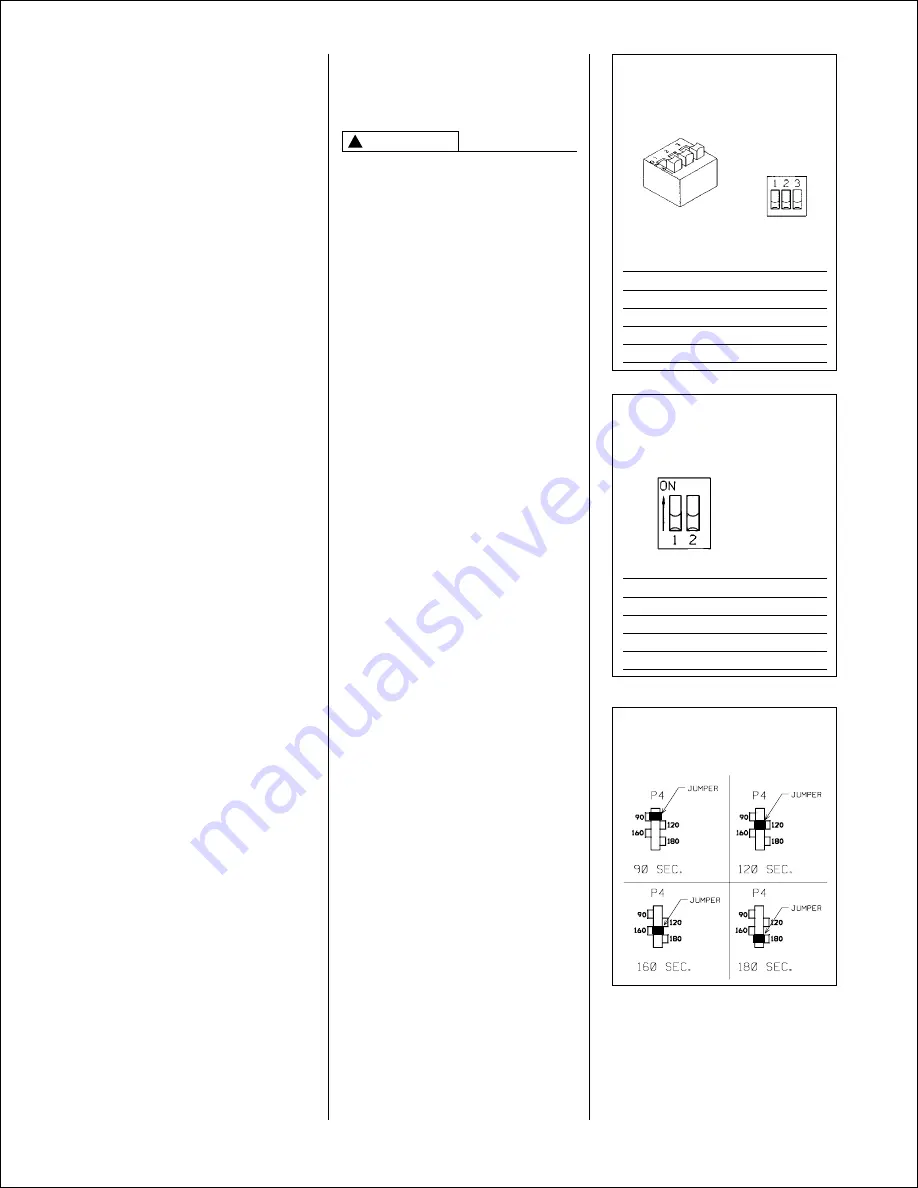
FIGURE 20
UT Electronic Controls 1012-925A
BLOWER OFF TIMINGS
5. After 5 seconds of inter-purge, the
the inducer operate for 180 seconds
before the next ignition trial.
6. It repeats this process up to four times.
At the end of the last try, the inducer
stops immediately.
7. The above sequence will repeat after a
goes through another set of trials for
ignition.
1. FAN SPEED — motor runs on this
speed when the thermostat is in the
“FAN” position.
2. COOL — connect desired cooling
3. HEAT — connect desired heating
4. HEAT/COOL — connect desired
speed when heating and cooling
speed are the same.
This tap not available on (-)GPJ
motor speeds to “HEAT” or “COOL” if
you use the “HEAT/COOL” terminal.
5. If heating and continuous speed are
the same, jump across “FAN” and
“HEAT” terminals.
This does not apply to (-)GPJ or
(-)GLJ models because the heat tap
functions as the continuous fan tap as
well.
See Figures 19, 20 & 21 for instructions
for setting the blower “OFF” timings.
GAS FURNACE (DIRECT
DRIVE) INSTRUCTIONS FOR
CHANGING BLOWER SPEED
The blower motor is wired for blower
speeds required for normal operation
as shown.
temperature rise after changing the
heating speed for any reason.
FIGURE 19
UT Electronic Controls 1028-928
BLOWER OFF TIMINGS