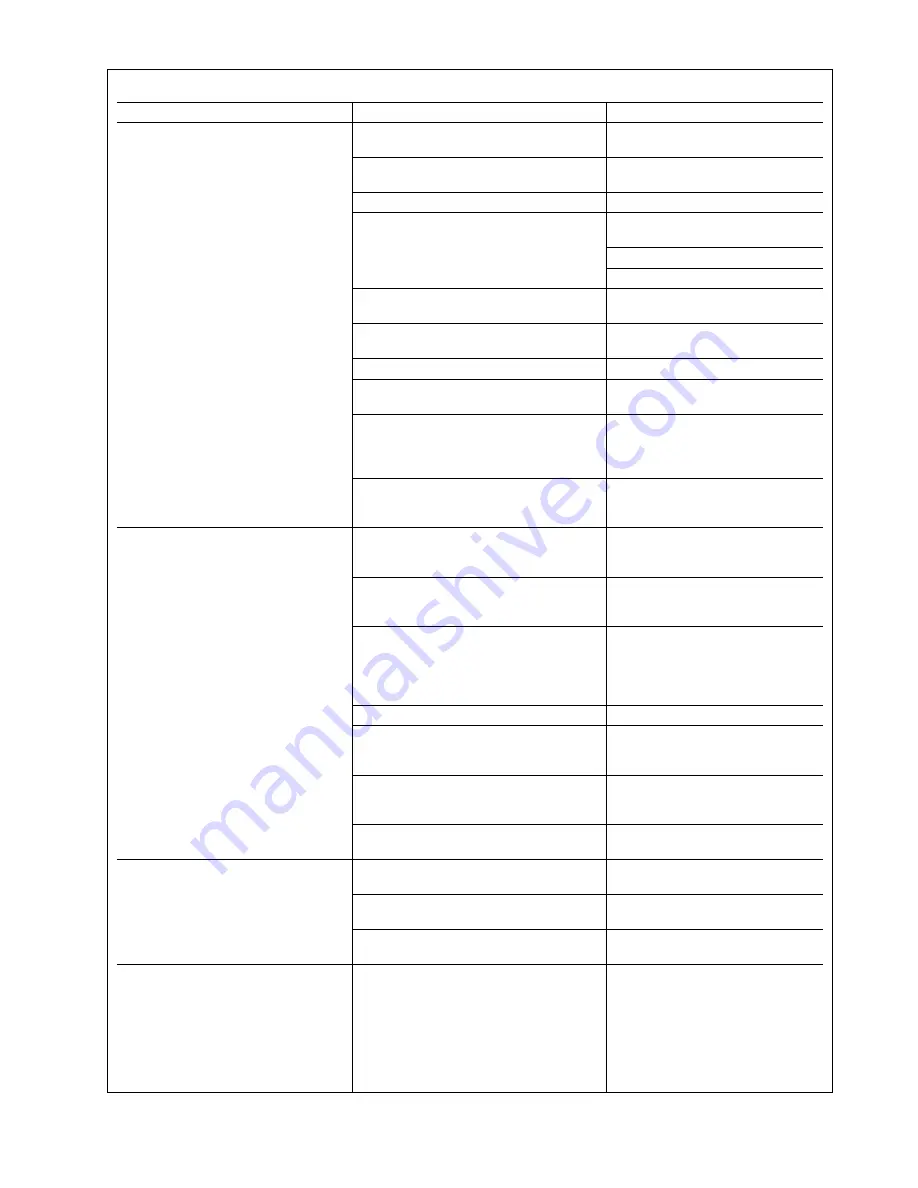
45
THERMOSTATIC EXPANSION VALVES
SYMPTOMS
POSSIBLE CAUSE
CHECK OR REMEDIES
High Superheat, Low Suction Pressure
Moisture freezing and blocking valve
Recover charge, install filter-drier,
evacuate system, recharge
Dirt or foreign material blocking valve
Recover charge, install filter-drier,
evacuate system, recharge
Low refrigerant charge
Correct the charge
Vapor bubbles in liquid line
Remove restriction in liquid line
Correct the refrigerant charge
Remove non-condensible gases
Size liquid line correctly
Misapplication of internally equalized
Use correct TEV
valve
Plugged external equalizer line
Remove external equalizer line
restriction
Undersized TEV
Replace with correct valve
Loss of charge from power
Replace power head or complete
head sensing bulb
TEV
Charge migration from sensing bulb
Ensure TEV is warmer than
to power head (Warm power head
sensing bulb
with warm, wet cloth. Does valve
operate correctly now?)
Improper superheat adjustment
Adjust superheat setting counter-
(Only applicable to TEV with adjustable
clockwise
superheat settings)
Valve feeds too much refrigerant,
Moisture causing valve to stick open.
Recover refrigerant, replace filter-
with low superheat and higher than
drier, evacuate system and then nor-
mal suction pressure
recharge
Dirt or foreign material causing
Recover refrigerant, replace filter-
valve to stick open
drier, evacuate system and
recharge
TEV seat leak (A gurgling or hissing
Replace the TEV
sound is heard AT THE TEV during
the off cycle, if this is the cause.)
NOT APPLICABLE TO BLEED
PORT VALVES.
Oversized TEV
Install correct TEV
Incorrect sensing bulb location
Install bulb with two mounting
straps, in 2:00 or 4:00 position on
suction line, with insulation
Low superheat adjustment
Turn superheat adjustment
(only applicable to TEV with
clockwise
adjustable superheat setting)
Incorrectly installed, or restricted
Remove restriction, or relocate
external equalizer line
external equalizer
Compressor flood back upon start up
Refrigerant drainage from flooded
Install trap riser to the top of the
evaporator
evaporator coil
Compressor in cold location
Install crankcase heater on
compressor
Any of the causes listed under
Any of the solutions listed under
Symptoms of Problem #2
Solutions of Problem #2
Summary of Contents for ASL-JEC Series
Page 48: ...48 FIGURE 13 WIRING DIAGRAM FOR ASL 024JEC 036JEC 19 0 WIRING DIAGRAMS...
Page 49: ...49 FIGURE 14 WIRING DIAGRAM FOR ASL 039JEC 048JEC 060JEC DUAL DRIVE...
Page 50: ...50...
Page 51: ...51...
Page 52: ...52 CM 1108...