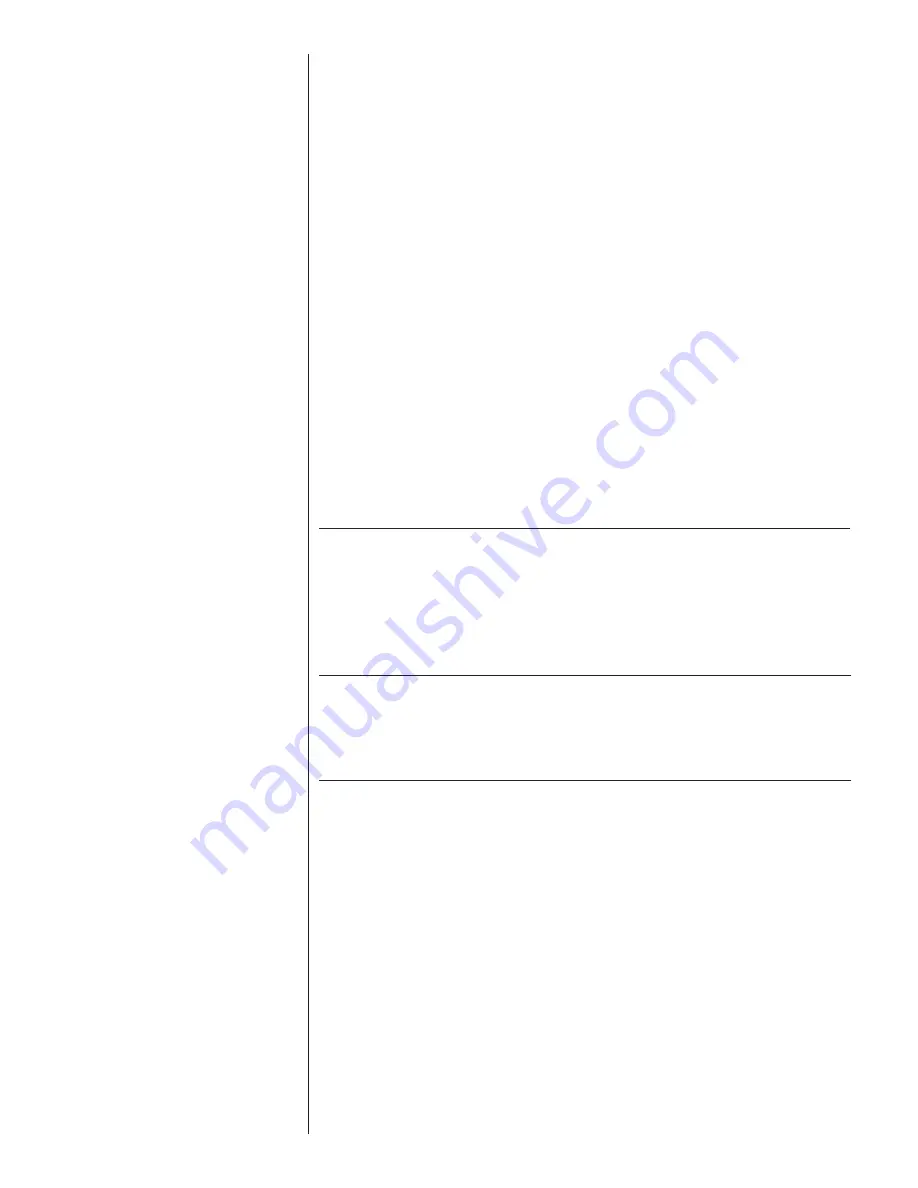
14
EVACUATION PROCEDURE
Evacuation is the most important part of the entire service procedure. The life and
efficiency of the equipment is dependent upon the thoroughness exercised by the
serviceman when evacuating air and moisture from the system.
Air or nitrogen in the system causes high condensing temperatures and pressure,
resulting in increased power input and non-verifiable performance.
Moisture chemically reacts with the refrigerant and oil to form corrosive hydrofluoric
acid. This attacks motor windings and parts, causing breakdown.
•
After the system has been leak-checked and proven sealed, connect the vacu-
um pump and evacuate system to 500 microns and hold 500 microns or less
for at least 15 minutes. The vacuum pump must be connected to both the high
and low sides of the system by connecting to the two pressure ports. Use the
largest size connections available since restrictive service connections may
lead to false readings because of pressure drop through the fittings.
•
After adequate evacuation, open both service valves by removing both brass
service valve caps with an adjustable wrench. Inssert a 3/16” [5 mm] or 5/16” [8
mm] hex wrench into the stem and turn counterclockwise until the wrench
stops.
•
At this time gauges must be connected to the access fitting on the liquid line
(small) service valve and the common suction port connected to the common
suction line betweenn the reversing valve and compressor to check and adjust
charge.
IMPORTANT: Compressors (especially scroll type) should never be used to evacu-
ate the air conditioning system because internal electrical arcing may result in a
damaged or failed compressor. Never run a scroll compressor while the system is in
a vacuum or compressor failure will occur.
FINAL LEAK TESTING
After the unit has been properly evacuated and service valves opened, a halogen
leak detector should be used to detect leaks in the system. All piping within the heat
pump, evaporator, and interconnecting tubing should be checked for leaks. If a leak
is detected, the refrigerant should be recovered before repairing the leak. The
Clean Air Act prohibits releasing refrigerant into the atmosphere.
START-UP AND PERFORMANCE
Even though the unit is factory charged with Refrigerant-410A, the charge must be
checked to the charge table attached to the service panel and adjusted, if required.
CHECKING AIRFLOW
The air distribution system has the greatest effect on airflow. The duct system is
totally controlled by the contractor. For this reason, the contractor should use only
industry-recognized procedures. The correct air quantity is critical to air conditioning
systems. Proper operation, efficiency, compressor life, and humidity control depend
on the correct balance between indoor load and outdoor unit capacity. Excessive
indoor airflow increases the possibility of high humidity problems. Low indoor airflow
reduces total capacity and causes coil icing. Serious harm can be done to the com-
pressor by low airflow, such as that caused by refrigerant flooding. Heat pump sys-
tems require a specified airflow. Each ton of cooling requires between 375 and 450
cubic feet of air per minute (CFM). See the manufacturer’s spec sheet for rated air-
flow for the system being installed. Duct design and construction should be carefully
done. System performance can be lowered dramatically through bad planning or
workmanship. Air supply diffusers must be selected and located carefully. They
must be sized and positioned to deliver treated air along the perimeter of the space.
If they are too small for their intended airflow, they become noisy. If they are not
located properly, they cause drafts. Return air grilles must be properly sized to carry
Summary of Contents for ARL-JEZ 16 Seer Series
Page 36: ...36 FIGURE 5 ARL 025 038 049 WIRING DIAGRAM ...
Page 37: ...37 FIGURE 6 ARL 061 JEZ ASL 024 JEC ASL 025 JEZ ASL 036 JEC ASL 037JEZ WIRING DIAGRAM ...
Page 38: ...38 ...
Page 39: ...39 ...
Page 40: ...40 CM 0213 ...