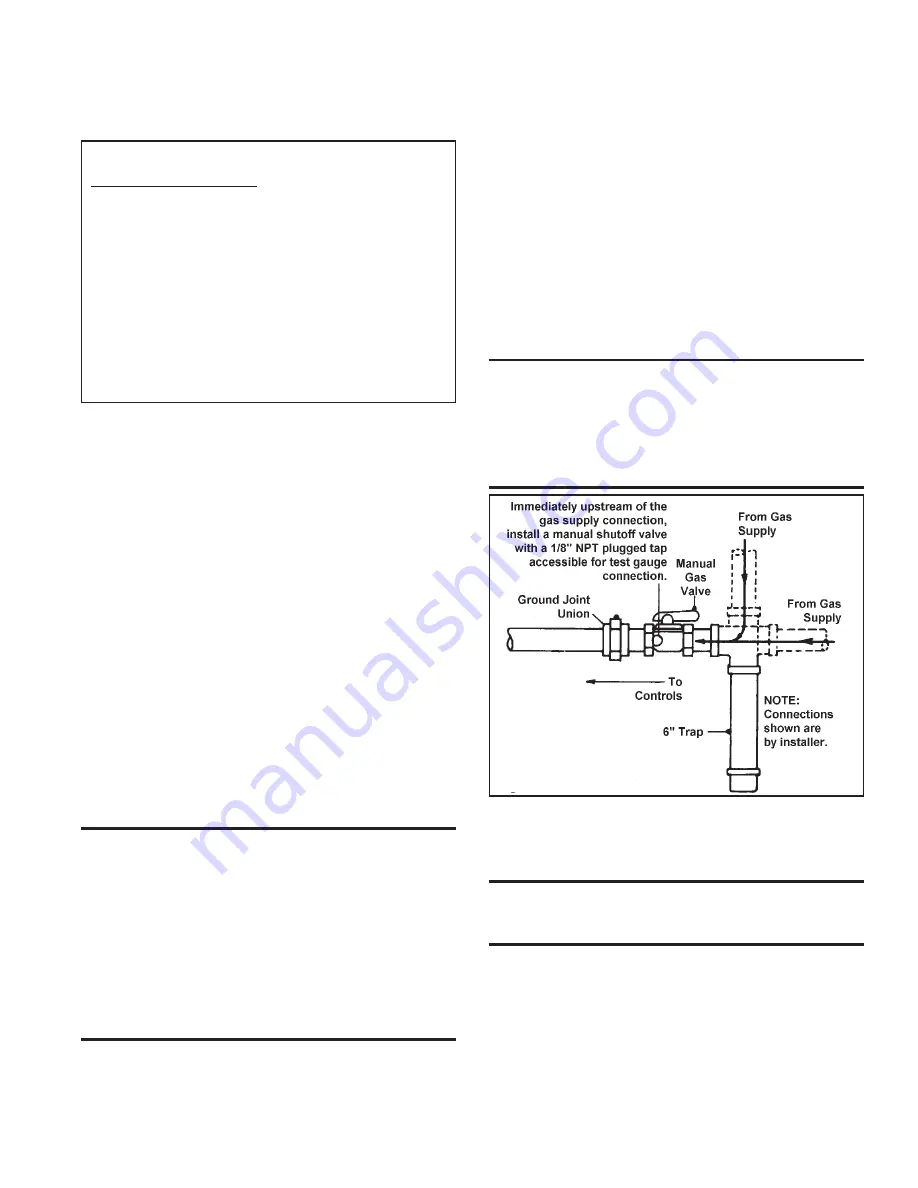
Form RGM 433-CV/LN, Mfg No. 177854 (Revision 1), Page 11
12. Gas Piping and Pressures
WARNING: This appliance is equipped for a
maximum gas supply pressure of 1/2 pound, 8 ounces,
or 14 inches water column. Supply pressure higher
than 1/2 pound requires installation of an additional
lockup-type service regulator external to the unit.
PRESSURE TESTING SUPPLY PIPING
Test Pressures Above 1/2 PSI: Disconnect the heater and manual valve
from the gas supply line which is to be tested. Cap or plug the supply
line.
Test Pressures Below 1/2 PSI: Before testing, close the manual valve
on the heater.
All piping must be in accordance with requirements outlined in the
National Fuel Gas Code ANSI/Z223.1a (latest edition), published by
the American Gas Association or CAN/CGA-B149.1 and B149.2, pub-
lished by the Canadian Gas Association (See Paragraph 1). Gas supply
piping installation should conform with good practice and with local
Figure 6 - Supply
Piping Connection
n
Vent System Joints
•
Follow the pipe manufacturer's instructions for joining Type B
double-wall vent pipe sections.
For joining double-wall pipe to the heater outlet collar or single-
wall pipe, follow the "boxed" instructions below:
Instructions for attaching double-wall (Type B) vent pipe to the
heater outlet or single-wall pipe run
Hardware and Sealant Required: 3/4" long sheetmetal screws; and a
tube of silicone sealant
1) Look for the "flow" arrow on the vent pipe; attach according to
the arrow. Slide the pipe so that the heater outlet or the single-wall
pipe is inside the double-wall pipe.
2) Drill a hole through the pipe into the outlet collar or the single-
wall pipe. (Hole should be slightly smaller than the sheet metal
screw being used.) Using a 3/4" long sheet metal screw, attach the
pipe. Do not overtighten. Repeat, drilling and inserting two addi-
tional screws evenly spaced (120
o
apart) around the pipe.
3) Use silicone sealant to seal any gaps. If there is an annular open-
ing, run a large bead of sealant in the opening. The bead of sealant
must be large enough to seal the opening, but it is not necessary to
fill the full volume of the annular area.
•
If using single-wall, 26-gauge or heavier galvanized pipe in the
vent connector of an appliance, secure slip-fit connections using
sheet metal screws or rivets. Seal pipe joints with high-temperature
tape or sealant. NOTE: The Model FT requires double-wall vent
connector pipe.
•
When attaching a vent connector to a masonry chimney, use a thimble
or slip joint to facilitate removal. Fasten vent connector securely
being sure that it does not extend into the chimney.
n
Vent System Support
Lateral runs should be supported every six feet using a non-combus-
tible material, such as strap steel or chain. Do not rely on the heater for
support of either horizontal or vertical vent pipe.
n
Vent Terminal
The vent terminal should be a minimum of six feet from adjoining
buildings. The vent terminal should be six inches higher than the an-
ticipated snow depth but no less than two feet above the roof. Where
the vent extends through the roof, a clearance thimble is required when
the flue pipe extends through combustible materials; follow the re-
quirements of the double-wall pipe manufacturer.
If using a Type B double-wall vent, terminate with a vent cap that meets
the requirements of the double-wall pipe manufacturer..
codes. Support gas piping with pipe hangers, metal strapping, or other
suitable material; do no rely on the heater to support the gas pipe.
Unit heaters are orificed for operation with natural gas having a heat-
ing value of 1000 (± 50) BTUH per cubic ft or propane gas with a
heating value of 2550 BTUH per cubic ft. If the gas at the installation
does not meet these specifications, consult the factory for proper ori-
ficing.
Pipe joint compounds (pipe dope) shall be resistant to the action of
liquefied petroleum gas or any other chemical constituents of the
gas being supplied.
Install a ground joint union and manual shut-off valve upstream of the
unit control system, as shown in Figure 6. The 1/8" plugged tapping in
the shutoff valve provides connection for a supply line pressure test
gauge. The National Fuel Gas Code requires the installation of a trap
with a minimum 3" drip leg. Local codes may require a minimum drip
leg longer than 3" (typically 6").
Gas supply connection is 1/2". Leak-test all connections by brushing
on a leak-detecting solution.
WARNING: All components of a gas supply
system must be leak tested prior to placing
equipment in service. NEVER TEST FOR
LEAKS WITH AN OPEN FLAME. Failure to
comply could result in personal injury, property
damage or death.
Manifold or Orifice Pressure Settings
Measuring manifold gas pressure cannot be done until the heater is in
operation. It is included in the steps of the "Check-Test-Start" proce-
dure in Paragraph 19. The following warnings and instructions apply.
WARNING: Manifold gas pressure must never exceed
3.5" w.c. for natural gas and 10" w.c. for propane
gas.
For Natural Gas: When the heater leaves the factory, the combination
gas valve is set so that the manifold gas pressure is regulated to 3.5"
w.c. Inlet supply pressure to the valve for natural gas must be a mini-
mum of 5" w.c. or as noted on the rating plate and a maximum of 14"
w.c.
For Propane Gas: When the heater leaves the factory, the combina-
tion gas valve is set so that the manifold gas pressure is regulated to
10" w.c. Inlet supply pressure to the valve for propane gas must be a
minimum of 11" w.c. and a maximum of 14" w.c.
Before attempting to measure or adjust manifold gas pressure, the inlet
supply pressure must be within the specified range both when the heater