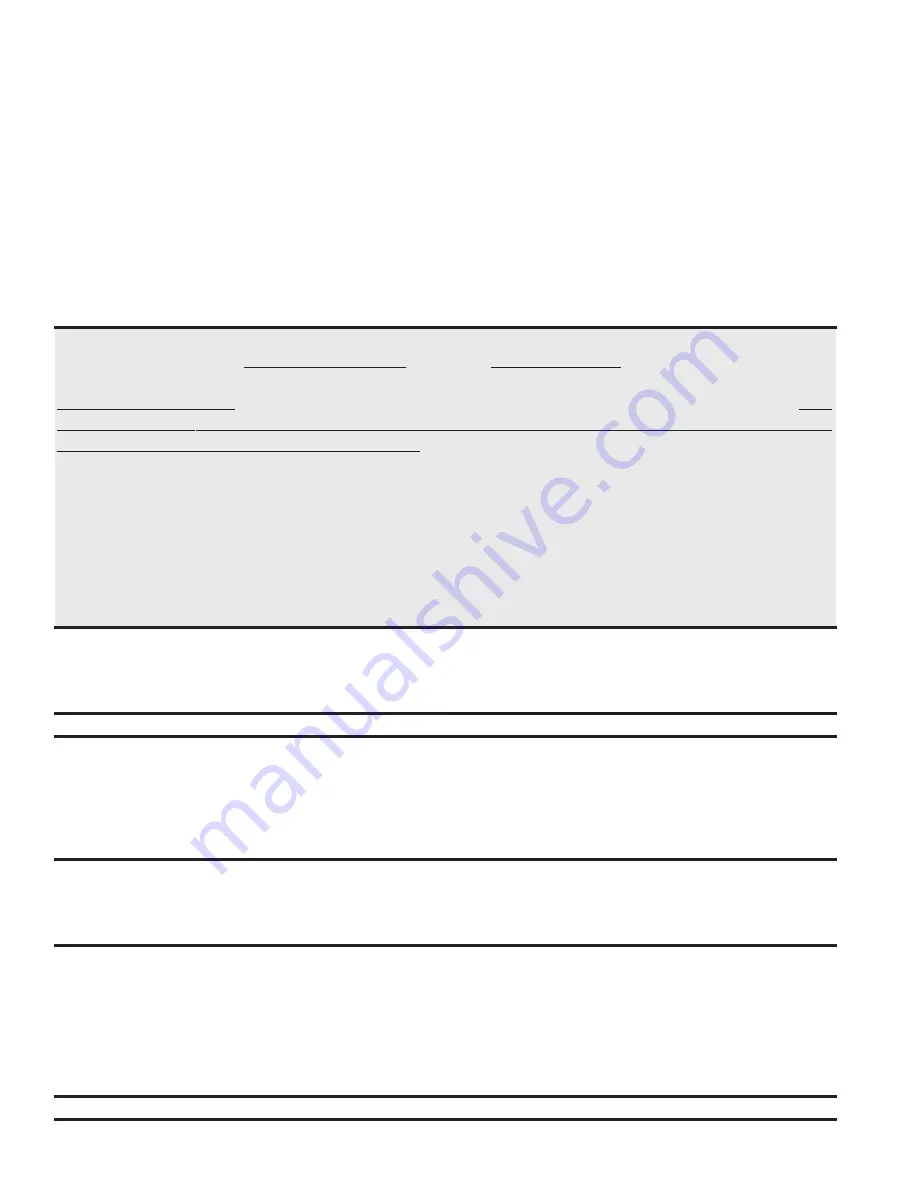
Form 433-CV/LN, Page 16
MAINTENANCE AND SERVICE
WARNING: If you turn off the power supply, turn off the gas. See Hazard Levels, page 1.
The material contained in the MAINTENANCE AND SERVICE Section of this manual is designed to aid a qualified service person in maintaining
and servicing this equipment. This unit will operate with a minimum of maintenance. To ensure long life and satisfactory performance, a heater that
is operated under normal conditions should be inspected and cleaned at the start of each heating season. If the heater is operating in an area where
an unusual amount of dust or soot or other impurities are present in the air, more frequent maintenance is recommended.
When any service is completed, be careful to reassemble correctly to ensure that no unsafe conditions are created. When re-lighting, always follow
the lighting instructions on the heater.
WARNING: Excessive dirt buildup on and inside the burner ports could cause fuel gas to spill out of
the back of the burner tube causing gas odor inside the building. If uncorrected, fuel spilling out of the
back of the burner tube could cause a fire or explosion. To prevent fuel gas from spilling from the back
of the burners, clean the burner ports at least annually.
Maintenance Schedule - The following procedures should be carried out at least annually (See Figure 11 and Paragraphs 20-30.):
•
Clean all dirt and grease from the primary and secondary combustion air openings (vents in cabinet panels).
•
Clean the fan blade, fan guard, and motor.
•
Clean the heat exchanger both internally and externally.
•
Check the burners for scale, dust, or lint accumulation.
•
Check the vent system for soundness. Replace any parts that do not appear sound.
•
Check the wiring for any damaged wire. Replace damaged wiring. (See Paragraph 13 for replacement wiring requirements.)
NOTE: Use only factory-authorized replacement parts.
CGA B149.1and B149.2, Installation Code for Gas Burning Appli-
ances and Equipment, and this manual. Determine that there is no
blockage or restriction, leakage, corrosion and other deficiencies
which could cause an unsafe condition.
3. In so far as practical, close all building doors and windows and all
doors between the space where the heater is and other spaces of the
building. Turn on clothes dryers and exhaust fans, such as range
hoods and bathroom exhausts, so they shall operate at maximum
speed. Do not operate a summer exhaust fan. Close fireplace damp-
ers.
4. Light the heater following the lighting instructions. Adjust the ther-
mostat for continued operation. Verify that combustion products
DANGER: The gas burner in this gas-fired equipment is designed and equipped to provide safe and
economically controlled complete combustion. However, if the installation does not permit the burner
to receive the proper supply of combustion air, complete combustion may not occur. The result is
incomplete combustion which produces carbon monoxide, a poisonous gas that can cause death. Safe
operation of indirect-fired gas burning equipment requires a properly operating vent system which
vents all flue products to the outside atmosphere. FAILURE TO PROVIDE PROPER VENTING WILL
RESULT IN A HEALTH HAZARD WHICH COULD CAUSE SERIOUS PERSONAL INJURY OR
DEATH.
Always comply with the combustion air requirements in the installation codes and in Paragraphs 7 and
8. Combustion air at the burner should be regulated only by manufacturer-provided equipment. NEVER
RESTRICT OR OTHERWISE ALTER THE SUPPLY OF COMBUSTION AIR TO ANY HEATER.
Indoor units installed in a confined space must be supplied with air for combustion as required by
Code and in Paragraph 8 of this heater installation manual. MAINTAIN THE VENT SYSTEM IN
STRUCTURALLY SOUND AND PROPERLY OPERATING CONDITION.
19. Check Installation & Start-up (cont'd)
Check the installation after start-up (cont'd):
are venting properly. After determining that the heater vents prop-
erly, return doors, windows, exhaust fans, and fireplace dampers to
their previous conditions. If improper venting is observed, the vent-
ing system must be corrected.
o
With the unit in operation, measure manifold gas pressure. See Para-
graph 12.
o
Turn the unit off and on, pausing two minutes between each cycle.
Observe for smooth ignition.
o
Place the "Owner's Envelope" containing the Limited Warranty, this
booklet, and any control or optional information in an accessible
location near the heater. Follow the instructions on the envelope.