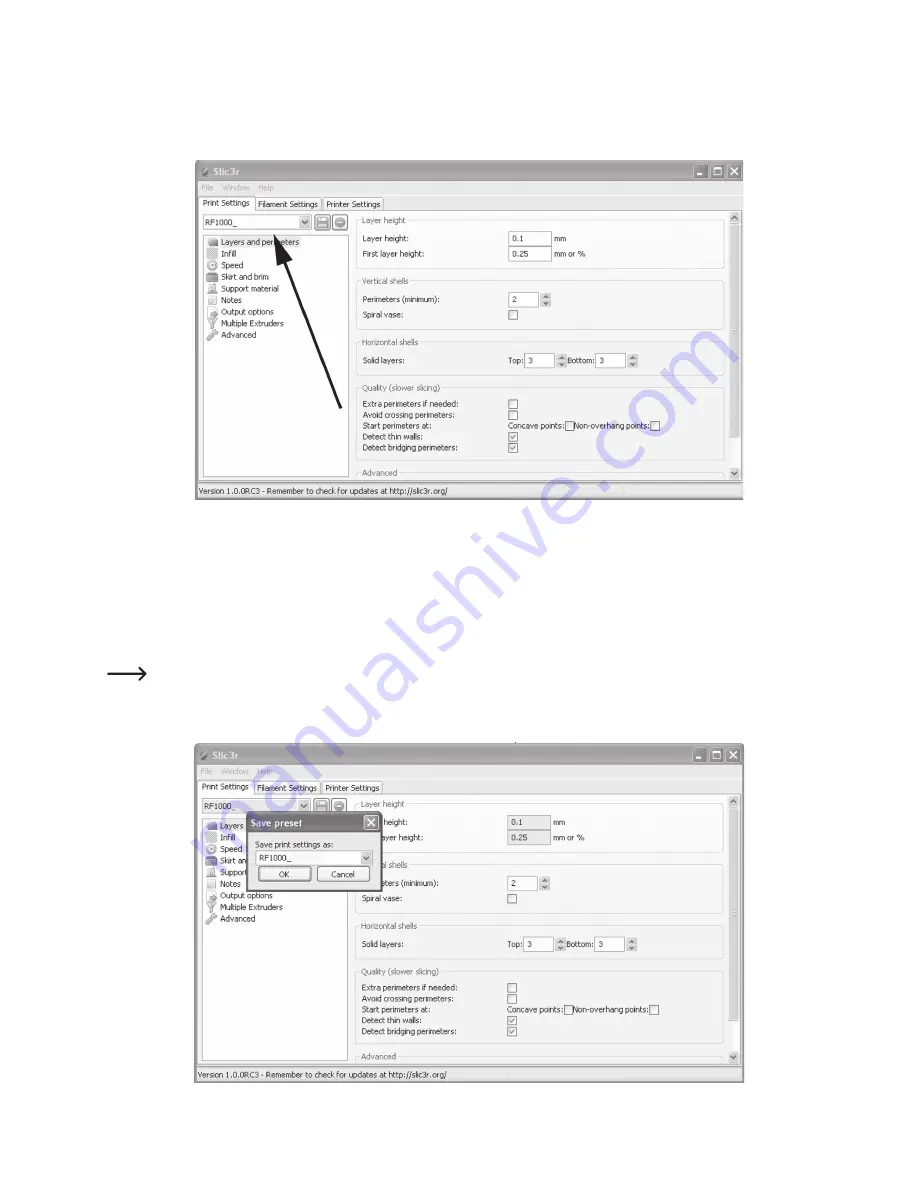
110
Select the tab “Print Settings” and click “Load Config...” in the menu.
Select the folder “Slic3r Settings” on the enclosed SD card in the following dialogue field. Select the first configuration file in this
folder and confirm selection with the button “Open”.
The selected file appears in the window.
Save the configuration file by clicking the disc symbol.
Leave the suggested name or assign one of your own for this configuration setting and click “OK”.
Open the tabs “Filament Settings” and “Printer Settings” in the same manner and save the above file in these tabs as well.
Then save all other configuration files on the SD card as described above in the tabs “Print Settings”, “Filament Settings” and
“Printer Settings”.
For a more detailed description of the different files on the SD-card, see this Annex, “Explanation on the Configuration
Files on the Enclosed SD Card”.