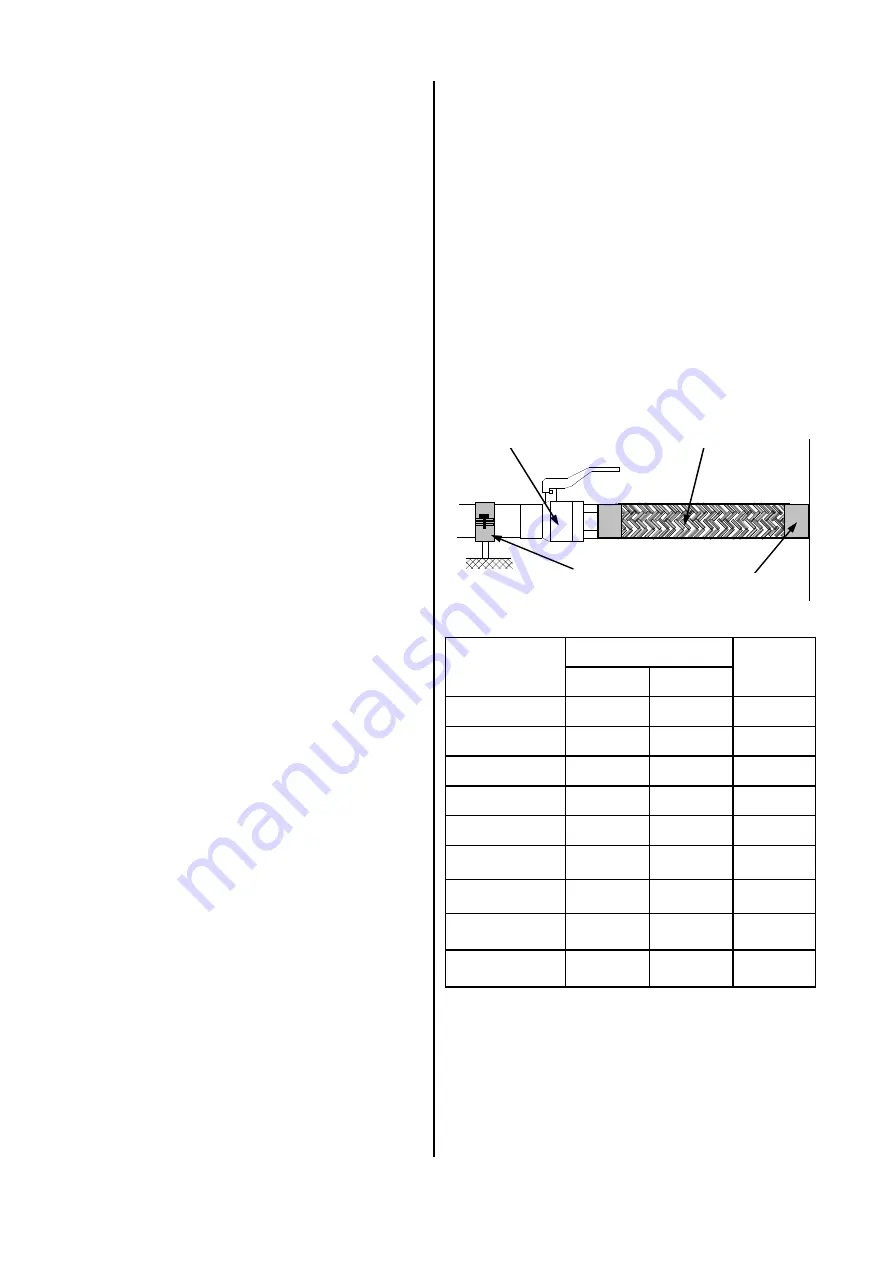
16
Hydraulic connections
The hydraulic connections are located on the back of
the units.
The RKW 1000 and 1600 INOX units are ready to be
connected upon shipment.
For the RKW 2600, 3600 and 4500 INOX units, it is
possible to separate the plate heat exchanger of the
chiller and the storage module mounted underneath this.
For the RKW 2600 INOX unit, the plate heat exchanger
and the storage module are connected hydraulically by
the pipe connection installed at the factory.
For the RKW 3600 and 4500 INOX units, the plate heat
exchanger and the separately ordered storage module
must be connected upon assembly with the supplied
pipe connection. If the module is set up separately, the
necessary connection line must be installed by the cus-
tomer
The RKW 8000 and 9800 INOX units in this series are
supplied without hydraulics. The required components
are selected by the person who develops the system.
General information
◊
We recommend equipping the connections with
shut-off valves for service purposes.
◊
Additional, automatic ventilation valves must be
mounted at the highest location of the installation in
the supply and discharge pipes.
◊
To prevent vibrations from being transferred, com-
pensators (flexible lines) should be used between
the fixed pipe installation and the chiller.
◊
All pipe lines must be insulated to protect them from
condensation. According to the HeizAnlV (German
Heating Systems Ordinance), a 50% insulation di-
ameter must be planned for cooling mode and a
100% insulation diameter for cooling and heating
mode.
◊
To prevent the unit from becoming dirty, a water filter
(approx. 16 meshes pro cm²) should be installed in
the discharge line.
◊
The water pipes may not exert any static strain on
the chiller.
◊
A second key or pliers must be used to mount the
pipe lines on the RKW so as not to create any strain
on the pipe lines in the inside of the unit.
◊
If the chiller is only initially operated with a single part
of the overall system, the flow rate of the missing
system parts must be stimulated by pipe regulating
valves.
◊
To increase the run time of the unit, we recommend
using a storage module or cold water pipes that are
slightly larger to increase the volume if the necessary
capacity of the inner units is considerably smaller
than the cooling capacity of the chiller.
◊
The hydraulics must be set up in such a way that the
predefined minimum flow rate is reached.
Model
Water
incoming
outgoing
1000 INOX
1 ¼ ‘‘ inside 1 ¼ ‘‘ inside ½ ‘‘ outside
1600 INOX
1 ¼ ‘‘ inside 1 ¼ ‘‘ inside ½ ‘‘ outside
2600 INOX
1 ¼ ‘‘ inside 1 ½ ‘‘ inside
½ ‘‘ outside
3600 INOX
2 ‘‘ inside
2 ‘‘ inside
-
4500 INOX
2 ‘‘ inside
2 ‘‘ inside
-
3600 INOX with
storage module
2 ‘‘ inside
2 ‘‘ inside
½ ‘‘ outside
4500 INOX with
storage module
2 ‘‘ inside
2 ‘‘ inside
½ ‘‘ outside
8000 INOX
2 x 2 ‘‘inside
2 x 2 ‘‘ in-
side
-
9800 INOX
2 x 2 ‘‘inside
2 x 2 ‘‘ in-
side
-
Filling con-
nection
Shut-off valve
Compensator
Static attachment
RKW connection
Connecting the water pipes
The RKW 1000, 1600 and 2600 INOX models in this
series are equipped with a cold water storage module
as a compact unit. The 3600, 4500, 8000 and 9800
INOX models are supplied in this series without hydrau-
lics for technical reasons. The water components in-
cluding the plate heat exchanger and the differential
pressure monitor are located in the chiller. The hydraulic
connections are found on the backs of all units.
For models RKW 3600 and 4500 INOX and higher, a
separate storage module can be mounted underneath
the chiller or somewhere else (e.g. inside the building).
So as not to transfer the vibrations of the chiller to the
system parts, the lines are connected to the unit by
compensators (flexible lines). We recommend equip-
ping the connections with shut-off valves for service pur-
poses.