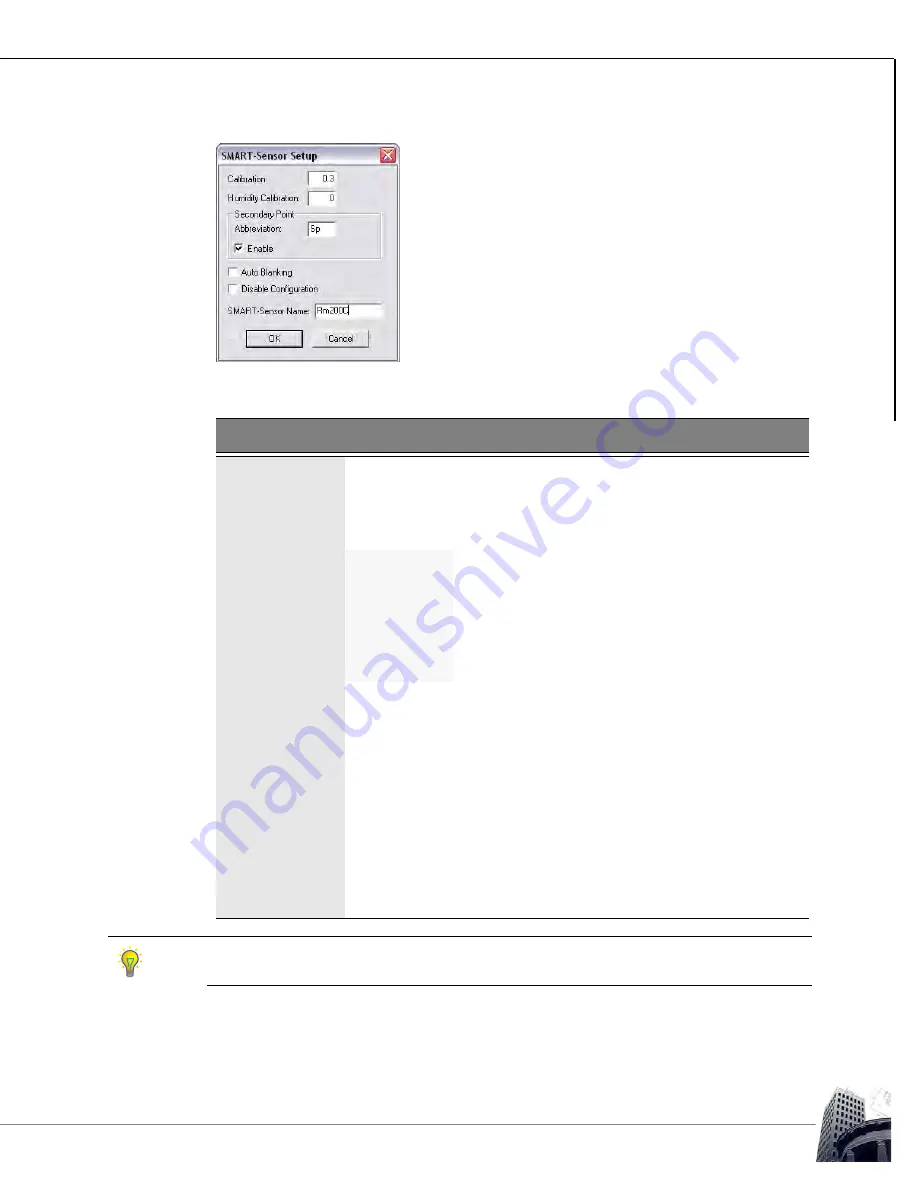
65
The SS Worksheet
U
SER
G
UIDE
SOFTWARE PROGRAMMING
SMART-S
ENSOR
™
2004 – 2014 Reliable Controls
®
Corporation. All rights reserved.
F
IGURE
62: SMART-S
ENSOR
SETUP
DIALOG
BOX
T
ABLE
14: SMART-S
ENSOR
S
ETUP
D
IALOG
B
OX
Field
Description
Calibration
Used to calibrate the onboard temperature sensor ± 3.1 degrees
in °C or °F.
Humidity
Calibration
Used to calibrate the onboard humidity sensor ± 31 percent in
%RH (-H models only).
Secondary
Point
Abbreviation
Two character abbreviated name to be displayed
preceding the value of the secondary-point in
Idle
mode.
Enable
Enables the display of the secondary point on the
top row of the LCD in
Idle
mode rather than the Tag
for Point 1.
Auto Blanking
The LCD reverts to the idle screen after 20 seconds of button
inactivity. When Auto Blanking is enabled, the LCD automatically
turns off after 20 seconds of button inactivity in the idle screen (40
seconds of inactivity before screen blanking occurs). The display
will reappear in
Idle
mode when any button is pressed.
Disable
Configuration
Locks out the configuration abilities of the SS-L inherent in the
firmware. If this box is enabled, the SS-L may not be used as a
SETUP-Tool
™
or Flow Tool.
SMART-Sensor
Name
Twenty character name for the SMART-Sensor
™
LCD that will
appear in the
SMART-Sensor
worksheet title bar and the System
Tree.
If
Time
is selected as the Range for the secondary point, the abbreviation will not be shown.
Instead, AM or PM will be displayed.