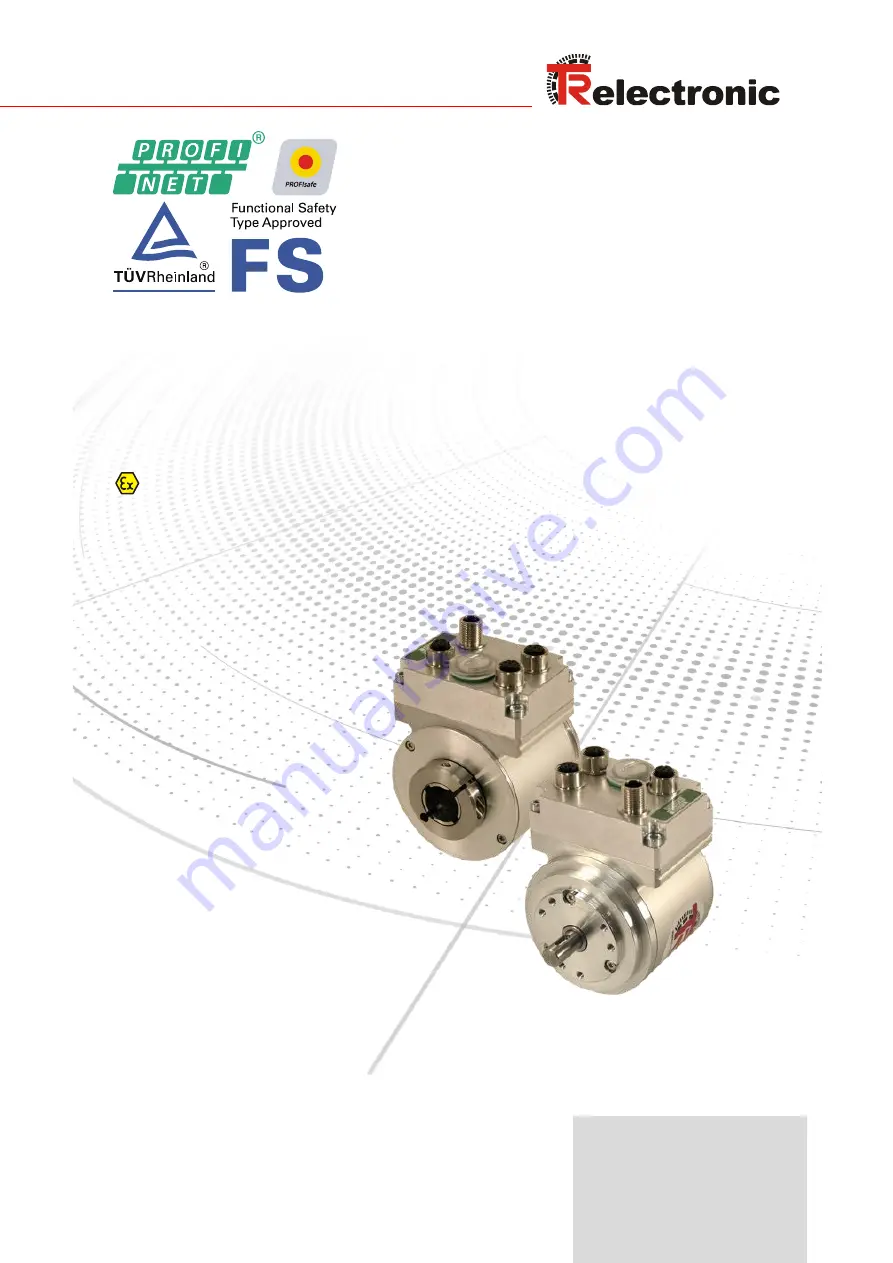
TR
-
EC
E
-
BA
-
G
B
-
0095
-
1
9
05
/30
/201
8
User Manual
Interface
CDH 75 M
Translation of the original manual
_
Safety instructions
_
Device-specific specifications
_
Installation/Commissioning
_
Parameterization
_
Cause of faults and remedies
Absolute Encoder CD_-75
PROFINET/PROFIsafe
Explosion Protection Enclosure
_
A**75*
_
A**88*
Protection Enclosure
_
CDV115
CDH 75 M
DIN EN 61508:
SIL CL3
DIN EN ISO 13849:
PL e
CDV 75 M
CDW 75 M