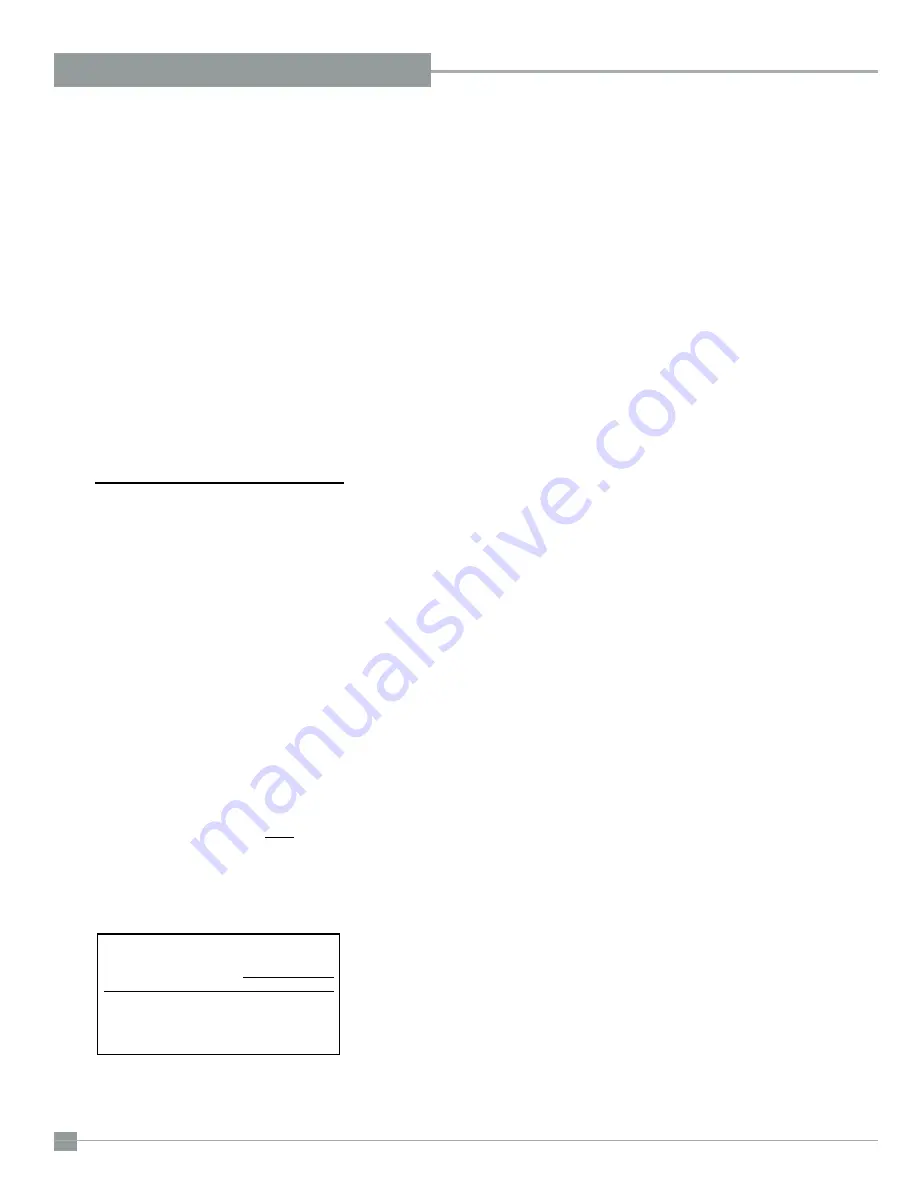
42
Regency Gemfire™ Gas Fireplace
42
OPERATING INSTRUCTIONS
OPERATING
INSTRUCTIONS
1)
Read and understand these instructions
before operating this appliance.
2)
Check to see that all wiring is correct and
enclosed to prevent possible shock.
3)
Check to ensure there are no gas leaks.
4)
Make sure the glass in the glass door frame
is properly positioned. Never operate the
appliance with the glass removed.
5)
Verify that the venting and cap are
unobstructed.
6)
The unit should never be turned off, and on
again without a minimum of a 60 second
wait.
LIGHTING
PROCEDURE
NOTE: The Gas ON/OFF knob cannot be
turned from "ON", "PILOT" or "OFF" unless
it is partially depressed.
Warning:
Turn off the unit by way of the wall
switch or remote. Allow unit to cool at least
10 min. - prior to removing faceplate.
1)
Ensure the wall mounted switch or remote
is in the "OFF" position.
2)
Ensure unit has cooled at least 10 min. -
prior to removing faceplate.
3)
Turn the gas control knob so the indicator
points to the "OFF" position and wait 5
minutes for any gas in the combustion
chamber to escape.
4)
Turn the gas control knob counterclockwise
so the indicator points to the "PILOT" position.
Depress the gas control knob fully. Depress
the igniter button until the pilot lights. After
approximately one minute, release the gas
control knob. The pilot flame should continue
to burn.
Only when the pilot holds, without pressure
being applied to the gas control knob, re-install
the glass door to the unit. The unit
must not
be operated without the glass door in place.
If the pilot does not remain lit, repeat opera
-
tion allowing a longer period before releasing
gas control knob.
5)
When the pilot stays lit, turn the gas control
knob to the "ON" position.
6)
Use the wall switch or remote control to turn
the unit ON.
7)
Re-install faceplate.
NOTE:
When using the remote control refer to
the remote manual.
NOTE:
If there is no spark present at the pilot
when depressed, the AA battery may
be weak. Refer to "DC Spark Battery
Replacement" section.
During the first few fires, a white film
may develop on the glass front as part of
the curing process. The glass should be
cleaned after the unit has cooled down
or the film will bake on and become very
difficult to remove. Use a non-abrasive
cleaner and DO NOT ATTEMPT TO CLEAN
THE GLASS WHILE IT IS HOT.
The
FIRST FIRE
in your heater is part of the paint
curing process. To ensure the paint is properly
cured, it is recommended you burn your fireplace
for at least four (4) hours the first time.
When first operated, the unit will release an
odour caused by the curing of the paint and the
burning off of any oils remaining from manufac
-
turing. Smoke detectors in the house may go off
at this time. Open a few windows to ventilate
the room for a couple of hours. The glass may
require cleaning.
NOTE:
When the glass is cold and the appliance
is lit, it may cause condensation and fog
the glass. This condensation is normal
and will disappear in a few minutes as
the glass heats up.
DO NOT ATTEMPT TO CLEAN THE
GLASS WHILE IT IS STILL
HOT
!
DO NOT BURN THE UNIT WITHOUT THE
GLASS DOOR IN PLACE.
FIRST FIRE
NORMAL OPERATING
SHUTDOWN
PROCEDURE
Warning:
Turn off the unit by way of the wall
switch or remote. Allow unit to cool at least
10 min. - prior to removing faceplate.
1)
Turn the wall mounted switch or remote to
the "OFF" position.
2)
Press "OFF" on the remote control.
3)
Turn the gas control knob to the "OFF"
position to turn off the pilot.
SOUNDS OF
GAS APPLIANCES
It is possible that you will hear some sounds from
your gas appliance. This is perfectly normal due to
the fact that there are various gauges and types
of steel used within your appliance. Listed below
are some examples. All are
normal operating
sounds
and should not be considered as defects
in your appliance.
Burner Tray:
The burner tray is positioned directly under the
burner and is made of a different gauge material
from the rest of the firebox and body. Therefore,
the varying thicknesses of steel will expand and
contract at slightly different rates which can cause
"ticking" and "cracking" sounds. You should also
be aware that as there are temperature changes
within the unit these sounds will likely re-occur.
Again, this is normal for steel fireboxes.
Pilot Flame:
While the pilot flame is on it can make a very
slight "whisper" sound.
Gas Control Valve:
As the gas control valve turns ON and OFF, a
dull clicking sound may be audible, this is normal
operation of a gas regulator or valve.
Unit Body/Firebox:
Different types and thicknesses of steel will
expand and contract at different rates resulting
in some "cracking" and "ticking" sounds will be
heard throughout the cycling process.