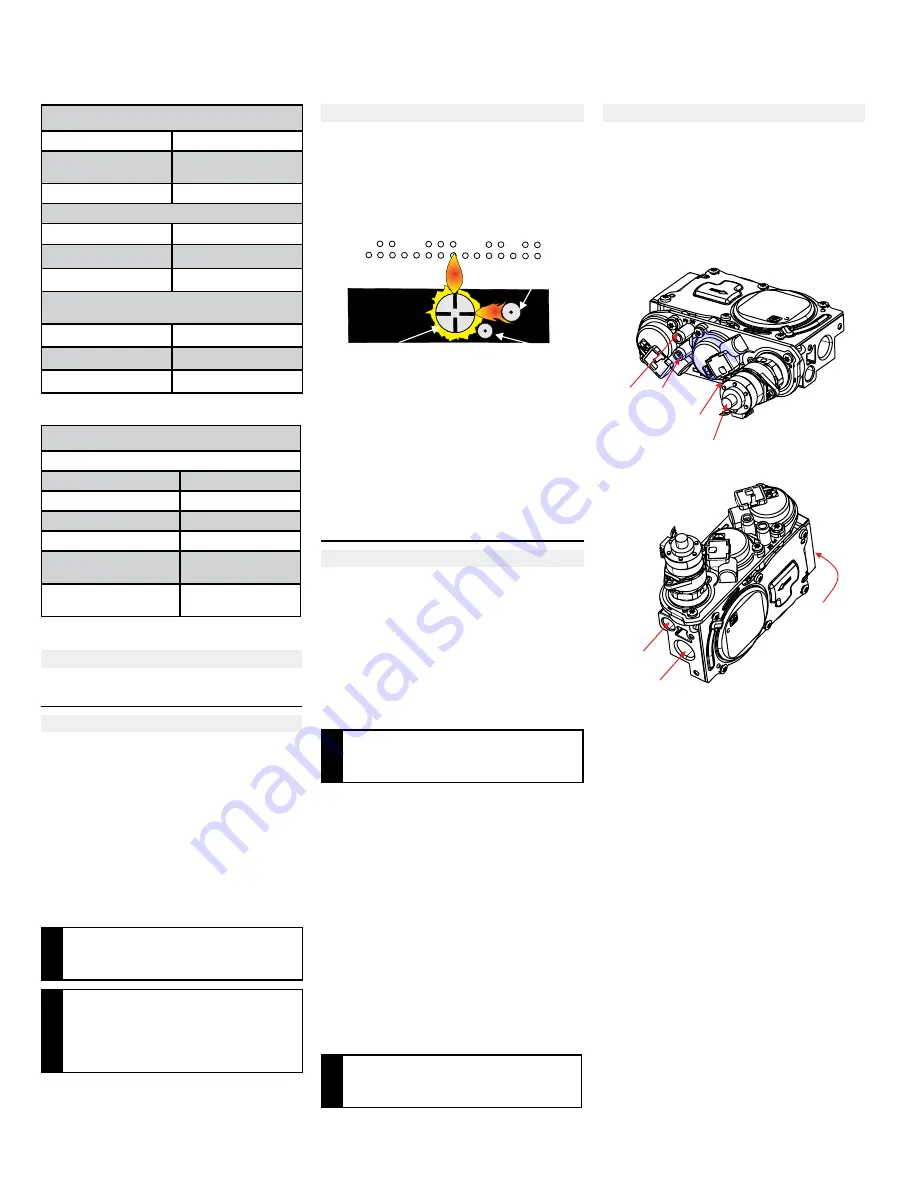
Gi29 Direct Vent Gas Insert | 31
installation
Gas Pipe Pressure Testing
It is necessary to isolate the unit from the gas supply
piping system prior to gas pipe pressure testing.
Close the unit’s manual shutoff valve during test
-
ing at pressures equal to or less than 1/2 psig.
(3.45 kPa). Disconnect the piping from the valve
at pressures over 1/2 psig.
The manifold pressure is controlled by a regulator
built into the gas control and should be checked
at the pressure test point.
High Elevation
This unit is approved for altitudes 0 ft. to 4,500 ft.
Gas Line Installation
Some municipalities have local codes for gas line
installation. Consult with your local authorities and
the CAN/CGA B149 installation code.
For USA installations, follow local codes and the
current National Fuel Gas Code, ANSI Z223.1.
When installing copper or flex connectors, use
approved fittings only. Flare nuts for copper lines
and flex connectors usually meet this requirement.
Provide a union for easy disconnection of gas lines
when servicing.
NG System Data
Min. Supply Pressure
5" WC (1.25kPa)
Low Setting Man.
Pressure
1.1 WC (0.27 kPa)
Max. Manifold Pressure
3.8" WC (0.95 kPa)
Factory equipped for altitude 0-2000 ft. (0-610 m)
Orifice Size
#38 DMS
Minimum Input
17,000 Btu/h (4.98 kW)
Maximum Input
31,500 Btu/h (9.22 kW)
Field convertible for altitude 2000-4500 ft. (610 m -
1,370 m) - use conversion kit #311-980
Orifice
#39 DMS
Minimum Input
16,500 Btu/h (4.83kW)
Maximum Input
30,500 Btu/h (8.93 kW)
LP System Data
Factory equipped for altitude 0-4,000 ft. (0-1,370 m)
Min. Supply Pressure
11" WC (2.74 kPa)
Low Setting Man. Pressure
2.9 WC (0.72 kPa)
Max. Manifold Pressure
10.5 WC (2.61 kPa)
Orifice Size
#52 DMS
Maximum Input
31,500 Btu/h (9.22
kW)
Minimum Input
17,000 Btu/h (4.98
kW)
NO
TE
To properly check gas pressure, both inlet
and manifold pressures should be checked
using the valve pressure ports on the valve.
1. Make sure the unit is in the “OFF” position.
2. Loosen the “IN” or “OUT” pressure tap(s),
turning counterclockwise with a 1/8” wide flat
screwdriver.
3. Attach manometer to “IN” or “OUT” pressure
tap(s) using a 5/16” ID hose.
4. Turn the unit on using the remote or wall switch.
5. Do the pressure check with the unit burning.
The setting should be within the limits specified
on the safety label.
6. When finished reading the manometer, turn off
the unit, disconnect the hose, and tighten the
screw clockwise with a 1/8” flat screwdriver.
NO
TE
The screw should be snug, but do not
over-tighten.
NO
TE
A shutoff/Dante valve should be supplied in
or near the unit (or as per local codes) for
ease of servicing this appliance.
IMPOR
TANT
Always check for gas leaks with a
soap and water solution or gas leak
detector. Do not use open flame for
leak testing.
Pilot Adjustment
Periodically check the pilot flames. Correct
Note: If you have an incorrect flame pattern,
contact your Regency
®
dealer for
further instructions.
Incorrect flame pattern will have small,
probably yellow flames, not coming into
proper contact with the rear burner or flame
sensor.
Burner
Flame Sensor
Pilot
Ignitor
flame pattern has two strong blue flames:
1 flowing around the flame sensor and 1
flowing across the burner (it does not have
to be touching the burner).
1. 6 Stage flame adjustment
2. Pilot adjustment
3. Inlet Pressure Tap
4. Outlet Pressure Tap
5. Pilot Outlet
6. Main Gas Outlet
7. Main Gas Inlet
885 S.I.T. Valve Description
1
2
3
4
6
5
7
1
2
3
4
6
5
7
Summary of Contents for Gi29LE
Page 72: ...72 Gi29 Direct Vent Gas Insert warranty ...
Page 73: ...Gi29 Direct Vent Gas Insert 73 notes ...
Page 74: ...74 Gi29 Direct Vent Gas Insert notes ...
Page 75: ......