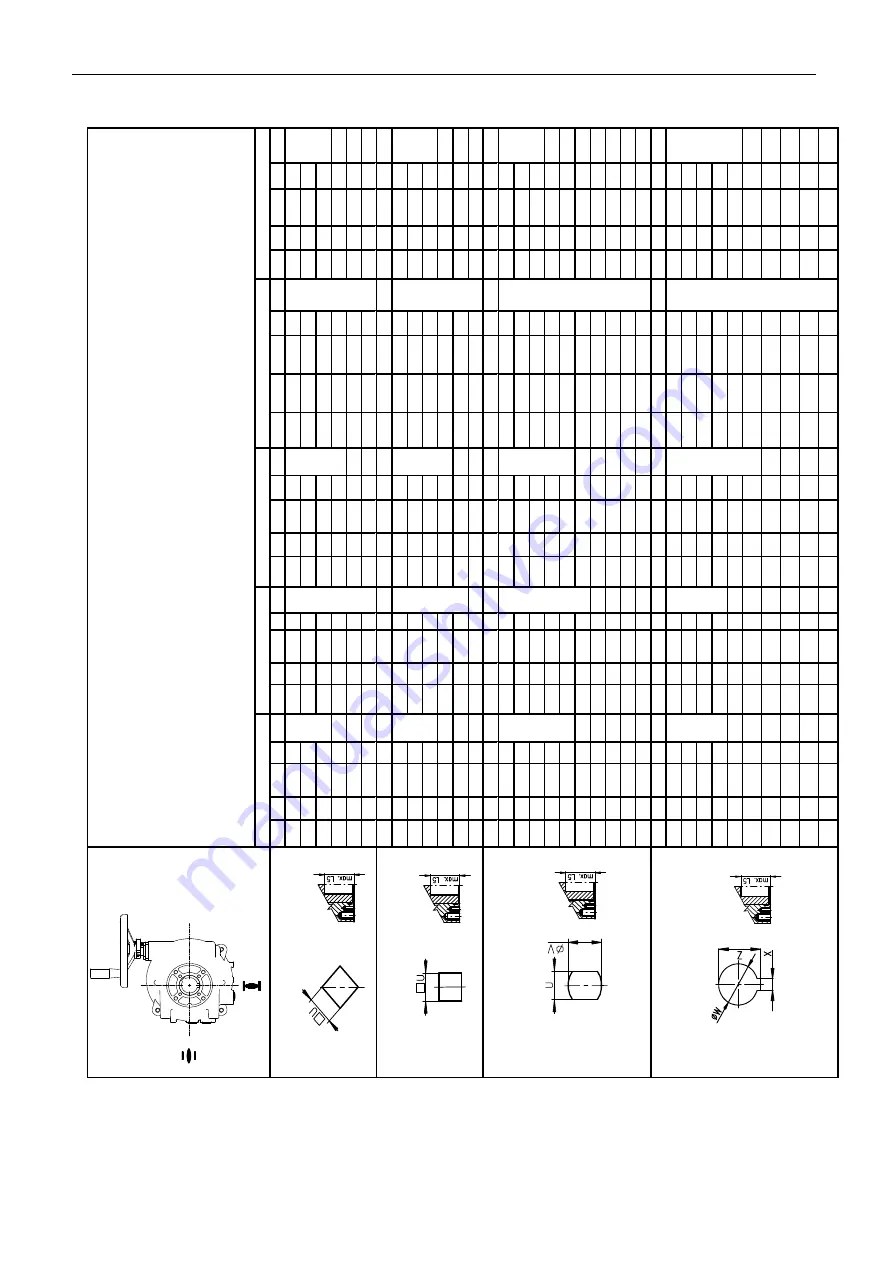
UP 0, UP 1, UP 2, UP 2.4, UP 2.5
53
Tv
ar
D
/
вид
D
/S
ha
pe
D
U
L5
U
L5
U
L5
U
L5
U
L5
D
-9
9
D
-9
9
D
-14
14
D
-11
11
D
-22
22
D
-11
11
D
-11
11
D
-17
17
D
-14
14
D
-27
27
D
-14
14
D
-12
12
D
-19
19
D
-16
16
D
-36
36
D
-14
14
D
-22
22
D
-17
17
D
-16
16
D
-22
22
D
-17
17
D
-27
27
Tv
ar
L
/
вид
L
/S
ha
pe
L
U
L5
U
L5
U
L5
U
L5
U
L5
L-9
9
L-9
9
L-
14
14
L-
11
11
L-
22
22
L-
11
11
L-
11
11
L-
17
17
L-
14
14
L-
27
27
L-
14
14
L-
12
12
L-
19
19
L-
16
16
L-
36
36
L-
16
16
L-
22
22
L-
17
17
L-
17
17
L-
22
22
L-
27
27
Tv
ar
H
/
вид
H
/S
ha
pe
H
U
V
L5
U
V
L5
U
V
L5
U
V
L5
U
V
L5
H-8
8
13
H
-8
8
13
H
-13
13
19
H
-8
8
13
H
-22
22
32
H-9
9
14
H
-10
10
16
H
-14
14
22
H-
10
10
16
H
-27
27
48
H
-11
11
14
H
-11
11
18
H
-17
17
36
H-
11
11
18
H
-36
36
48
H
-11
11
18
H
-13
13
19
H
-19
19
28
H-
13
13
19
H
-14
14
18
H
-14
14
22
H
-22
22
36
H-
14
14
22
H
-17
17
25
H-
16
16
22
H-
17
17
25
H-
19
19
28
H-
22
22
32
H-
27
27
48
Tv
ar
V
/
вид
V
/S
ha
pe
V
W
Z
X
L5
W
Z
X
L5
W
Z
X
L5
W
Z
X
L5
W
Z
X
L5
V-
12
12
13
,6
4
V-
17
17
19
,5
6
V-
17
17
19
,5
6
V-
17
17
19
,5
6
V-
42
42
45
,1
12
V-
14
14
16
,1
5
V-
18
18
20
,5
6
V-
18
18
20
,5
6
V-
18
18
20
,5
6
V-
50
50
53
,5
14
V-
18
18
20
,6
6
V-
20
20
22
,5
6
V-
22
22
24
,9
8
V-
20
20
22
,5
6
V-
48
48
51
,5
14
V-
30
30
32
,5
8
V-
28
28
30
,9
8
V-
22
22
24
,5
6
V-
60
60
64
,4
18
V-
36
36
39
,3
10
V-
28
28
30
,9
8
V-
40
40
43
,1
12
V-
42
42
45
,3
12
V-
30
30
32
,5
8
V-
32
,2
32
,2
35
6,5
V-
42
42
45
,1
12
V-
45
,4
45
,4
48
,8
10
V-
50
50
53
,5
14
TV
AR
P
RIP
O
JO
VA
CI
EH
O
D
IE
LC
A
PR
E
ES
/
Ф
О
РМА
ПР
И
СО
ЕД
И
НИ
ТЕЛ
ЬН
ОЙ
Д
ЕТ
АЛИ
/ C
O
U
PL
IN
G
S
HA
PE
U
P
2.5
U
P 0
U
P 1
U
P 2
U
P
2.4
36
36
36
36
37
.5
37
.5
37
.5
70
70
70
70
37
.5
49
49
49
49
56
56
56
56
O
Z/
З
/C
Summary of Contents for UP 0
Page 10: ...8 UP 0 UP 1 UP 2 UP 2 4 UP 2 5 5 9 Fig 1a Fig 1b ...
Page 11: ...UP 0 UP 1 UP 2 UP 2 4 UP 2 5 9 Fig 1c UP 2 5 with controller ...
Page 42: ...40 UP 0 UP 1 UP 2 UP 2 4 UP 2 5 7 Enclosures 7 1 Wiring diagrams UP 1 UP 2 UP 2 4 UP 2 5 ...
Page 43: ...UP 0 UP 1 UP 2 UP 2 4 UP 2 5 41 ...
Page 44: ...42 UP 0 UP 1 UP 2 UP 2 4 UP 2 5 Wiring diagrams UP 0 ...
Page 51: ...UP 0 UP 1 UP 2 UP 2 4 UP 2 5 49 Electric part turn actuators Unimact UP 2 4 UP 2 5 ...