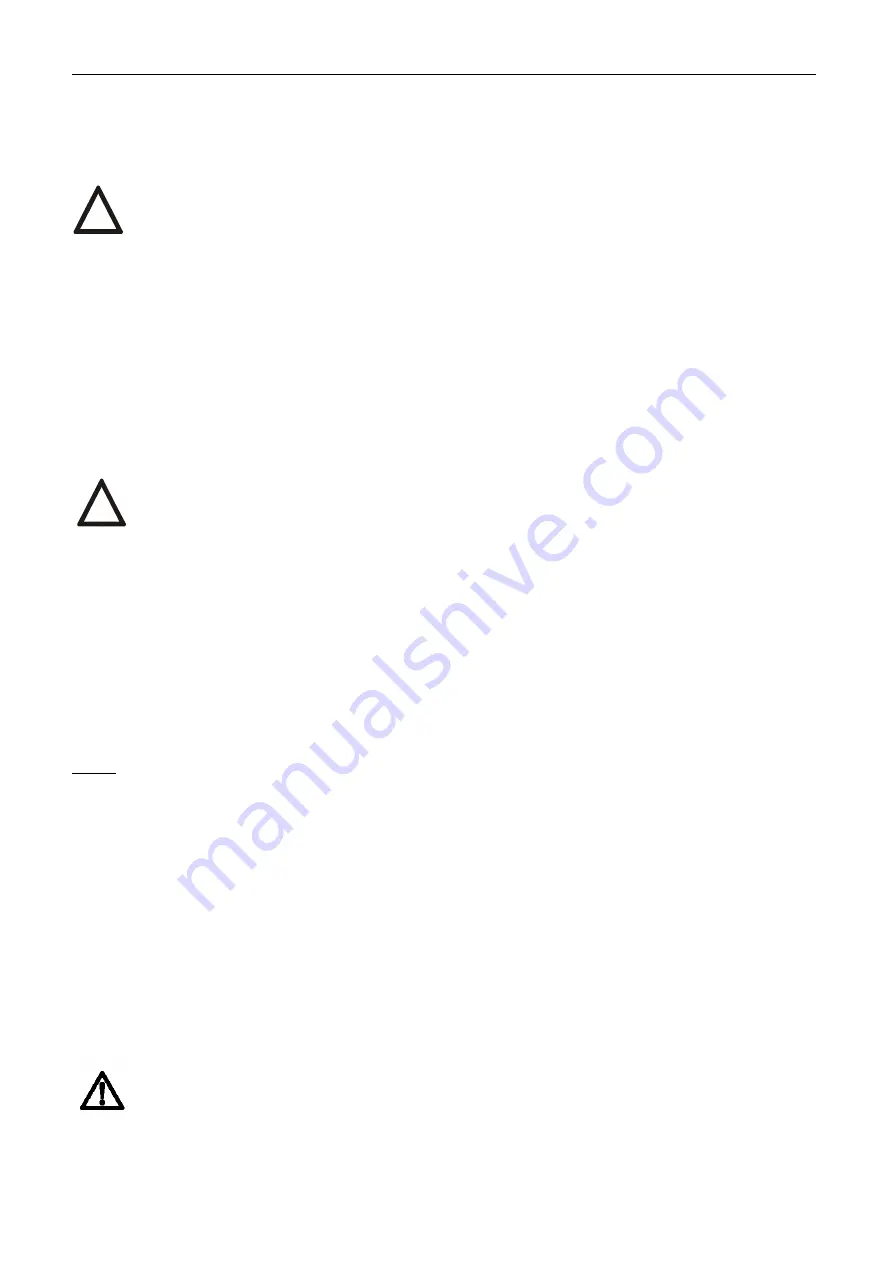
UP 0, UP 1, UP 2, UP 2.4, UP 2.5
19
3.1.2 Electric connection and checking of function
Follow up with connecting the EA with mains or master system.
1. Follow instructions in the part "Requirements for professional qualification"!
2. While laying electrical line abide by the instructions for heavy current installations. Power supply
cables must be of the type approved. Minimum thermal resistance of power supply cables and wires
must be +90°C.
3. Cables to terminal boards or connectors lead through screw cable glands.
4. Before initiation ES into operation internal and external protection terminals are needed to be
connected.
5. Feeding cables are to be fixed to the solid construction at most 150 mm from the cable glands.
6. Torque switching is not fitted with mechanical interlocking device (except for UP 2, UP 2.4, UP 2.5).
7. To prevent moisture from entering the actuator around the connecting cables, the cables must be
sealed with silicone material at the point of penetration through device shell.
Connecting with the master system:
The EA can be controlled with:
•
a built-in position controller
•
an external position controller
1. If the EA is controlled with an external controller using unified signal from a two- wire transmitter
(capacitive or resistive with a controller in two-wire connection), it is needed to arrange connecting of
the two-wire transmitter loop to electrical earth of the successive external controller!
2. Connection can be performed only in one point, in any part of loop out of the EA.
3. Electronics of the two-wire transmitters is galvanically insulated that is why it can serve as an
external source for supplying of several transmitters (their number depends on current which the
source can supply).
Connection with the terminal board:
Before the connection remove the actuator case and check whether the type of current,
power supply and frequency correspond with the data on the actuator nameplate.
Electric connection:
•
The electric connection should be realized according to the wiring diagram stuck into the case of the EA;
•
The electric connection should be performed through two cable glands see No. 2.2.2.
•
Once electrical services are completed put on the cover and fasten it evenly crosswise by bolts. Fasten the
cable glands to ensure specified shielding.
Notes:
1. To connect the input control signals and output signals is needed to use shielded wires with steel wire braid
(Galvanised Steel Wire Braid GSWB
Ξ
), for example cable type "Bruflex ® HSLCH", 4x0, 5 (company
Bruns Kabel).
2. The EA are delivered with cable glands which in case of correct tighten are onto the supply lead allow the
protection enclosure of IP 68.
3. The cable is to be fixed the way corresponding with its allowable bending radius not to damage or deform
the sealing element of the cable lead. The supply leads have to be fixed onto a fixed construction max. 150
mm from the leads.
4. It is recommended to connect the remote transmitters with shielded wires.
5. The face areas of the control part cover should be clean before fixing it back.
6. The EA is reversible if the time interval between the power supply is switched off and on for the reverse
direction of the output part motion is at least 50 ms.
7. The allowed delay after it is switched off, i.e. time from the switches reaction up to the motor without any
voltage is 20 ms maximally.
Observe the valve manufacturer´s instructions with respect to the requirement to ensure switching-off
in limit positions through position or torque switches!
!
!
Summary of Contents for UP 0
Page 10: ...8 UP 0 UP 1 UP 2 UP 2 4 UP 2 5 5 9 Fig 1a Fig 1b ...
Page 11: ...UP 0 UP 1 UP 2 UP 2 4 UP 2 5 9 Fig 1c UP 2 5 with controller ...
Page 42: ...40 UP 0 UP 1 UP 2 UP 2 4 UP 2 5 7 Enclosures 7 1 Wiring diagrams UP 1 UP 2 UP 2 4 UP 2 5 ...
Page 43: ...UP 0 UP 1 UP 2 UP 2 4 UP 2 5 41 ...
Page 44: ...42 UP 0 UP 1 UP 2 UP 2 4 UP 2 5 Wiring diagrams UP 0 ...
Page 51: ...UP 0 UP 1 UP 2 UP 2 4 UP 2 5 49 Electric part turn actuators Unimact UP 2 4 UP 2 5 ...