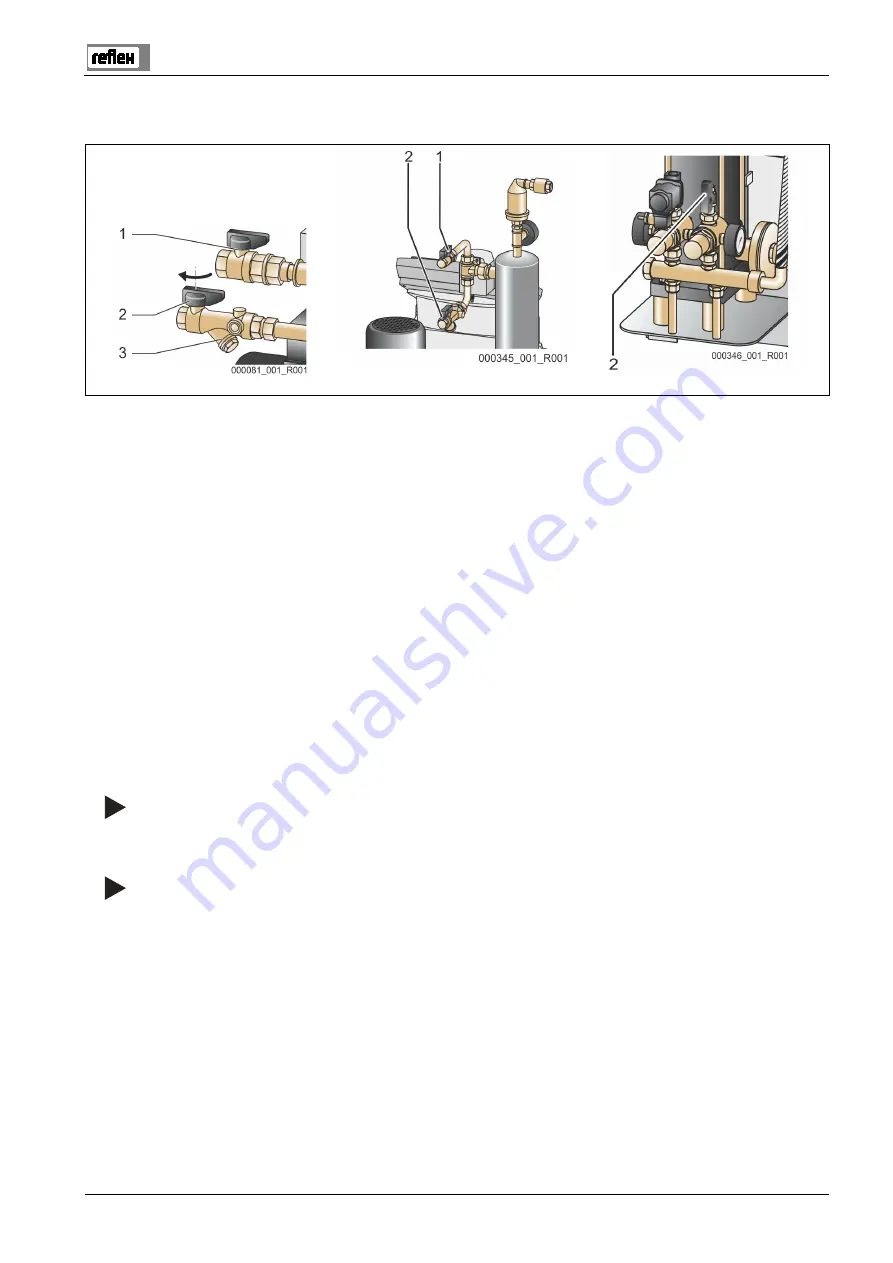
Commissioning
Servitec 35-120 with Touch controller — 06.07.2016 - Rev. B
English — 41
7.5
Vacuum test
Carefully perform the vacuum test to ensure the proper functioning of the device.
Servitec 35 – 60
Servitec 75 – 95
Servitec 75 – 120
Proceed as follows:
1 Close the ball valve (2) with the dirt trap (3) of the "DC" feed line to the spray pipe. The second ball valve (1) in the feed line from the
"DC" pump to the system remains open.
2 Generate a vacuum with the manual mode of the controller.
•
Switch to Manual mode.
– For more information about the Manual mode, see chapter 8.1.2 "Manual mode" on page 48 .
3 Use "Circulate" to activate continuous degassing until the vacuum gauge of the vacuum spray pipe indicates a stable vacuum.
•
Record the vacuum value displayed at the vacuum gauge.
4 After 10 minutes, check again the "PI“ vacuum gauge. The pressure must not change. If the pressure has increased, check the device
for leaks.
•
All screw connections at the "VT“ vacuum spray pipe.
•
The "DV" degassing valve at the "VT" vacuum spray tube.
•
The vent screw at the "PU" pump.
5 After the vacuum test has been concluded successfully, open the ball valve (2).
6 If the controller displays the "Insufficient water" error message, acknowledge the message with "OK".
The vacuum test is completed.
Note!
The obtainable vacuum corresponds to the saturation pressure at the existing water temperature.
– At 10 °C, a vacuum of approximately. -1 bar can be obtained.
Note!
Repeat steps 2 to 4 until no further pressure rise is observed.