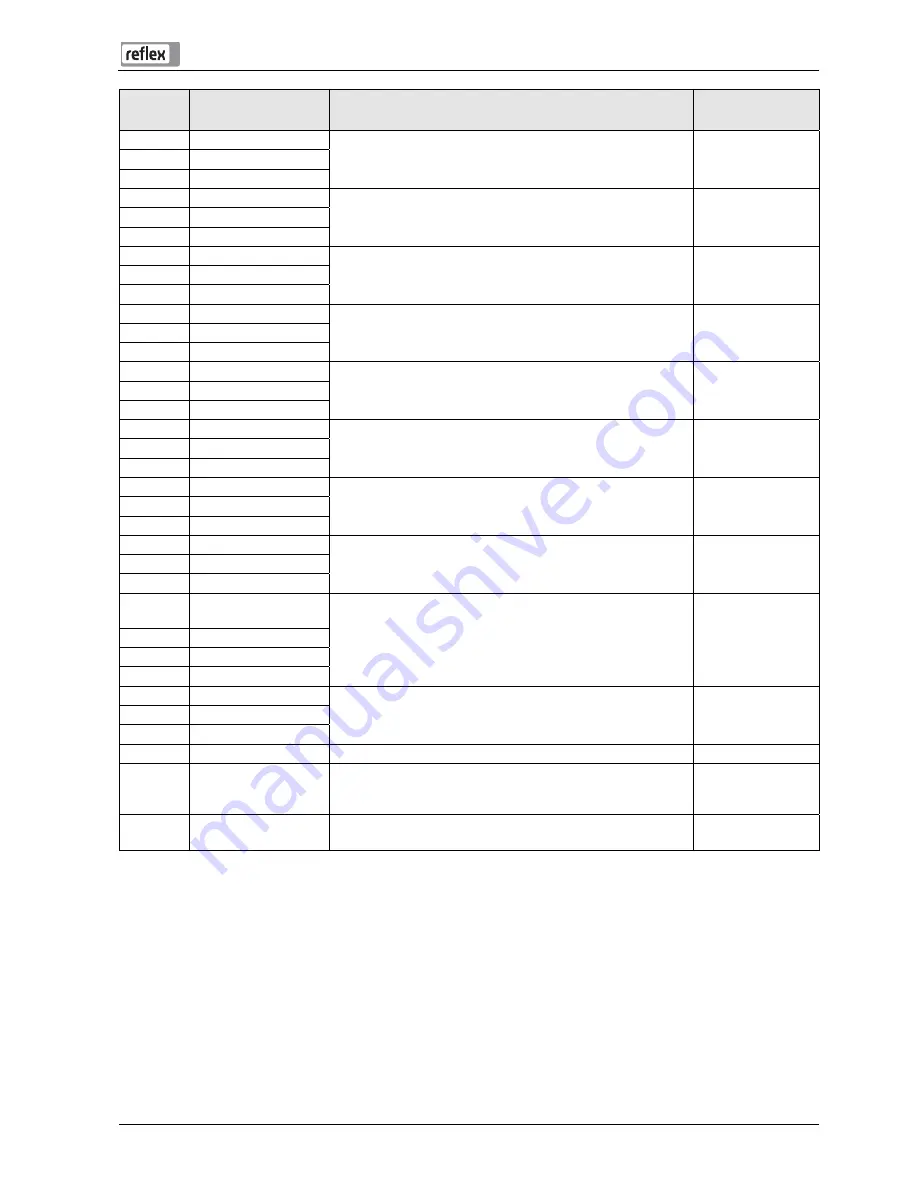
Installation
Vacuum spray degassing — 03.11.2014
English — 27
Terminal
number
Signal
Function
Wiring
1 PE
230 V power supply via mains cable and plug.
Pre-wired
2 N
3 L
4 PE
"PU" vacuum pump for degassing.
Pre-wired
5N N
6 M1
M 1
7 Y2
Overflow solenoid valve
Not used in standard model
---
8 N
9 PE
10 Y
1
"CD" 3-ways motor ball valve for regulating the degassing of make-
up and system water.
Pre-wired
11 N
12 PE
13 COM
Group message (floating).
User, optional
14 NC
15 NO
16 Not
assigned
External make-up demand from a pressure maintaining station;
controller must be set to "Levelcontrol"!
User, optional
17
Make-up (230 V)
18
Make-up (230 V)
19 PE
shield
Level analogue input, not used by the device.
---
20
- Level (signal)
21
+ Level (+ 18 V)
22 PE
(shield)
Pressure analogue input for display and make-up; controller must be
set to "Magcontrol"!
Pre-wired
23
- Pressure (signal)
24
+ Pressure (+ 18 V)
25
0 – 10 V (correcting
variable)
"CD" 3-ways motor ball valve, not used with the device.
---
26
0 – 10 V (feedback)
27 GND
28
+ 24 V (supply)
29 A
RS-485 interface.
User, optional
30 B
31 GND
32
+ 24 V (supply) E1
Supply for E1 and E2.
Pre-wired, bridged
33
E1
Contact water meter, for example in Fillset, see chapter 4.6 "Optional
equipment and accessories" on page 14 , for make-up evaluation,
contact 32/33 closed = meter pulse.
User, optional
34
E2
Insufficient water switch, not used with the device, contact 32/34
closed = OK.
Pre-wired, bridged