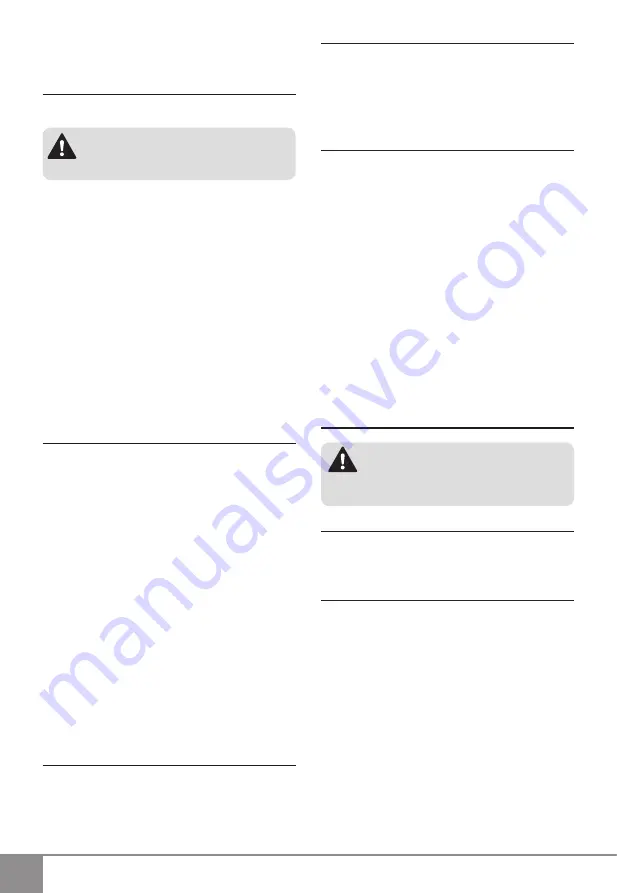
20
EN
RS 18Li MA • RS 18LiE MA
Its position can be different and depends on which side
the auxiliary handle is placed, as well as when the ma-
chine is mounted on a stand.
GRINDING WHEEL REPLACEMENT
Secure spindle (1) by depressing the spindle lock button
(2) provided on the gear case.
WARNING:
Never press button (2) while the
spindle is still rotating!
(With this button depressed turn the spindle till its pro-
nounced going deeper). Unscrew the fixing flange (11)
by a lock nut wrench. Place the new wheel on thesup-
port flange (10) with the inscriptions facing up, and screw
down flange (11) facing its flat side towards the wheel,
using the lock nut wrench. Use blotters if the wheel has
been delivered with them. After replacing the wheel op-
erate the machine with the new wheel in no load mode
for one minute. Vibrating or otherwise improperly rotat-
ing wheels must be replaced immediately and discarded.
Cup brushes (19) are screwed directly on spindle (1)
by means of an open-end spanner. (Check if the brush
thread length is sufficient to accept the spindle thread.)
Sanding is accomplished by means of flexible back
-
ing pad with nut (20) and sandpaper (21) equipped
with hook-and-loop fastening. The flexible backing pad
is screwed directly on the spindle (1) To dismount (un-
screw) the backing pad use a spanner when necessary.
MOUNTING THE WHEEL GUARD
Before performing the following operations, switch the
machine off.
Mounting the wheel guard
(Fig. 4)
- Rotate the black plastic ring
(Fig. 5)
, so that the
crevice S of the ring coincides with the groove for
the tooth of the fixing lever L.
- Place the wheel guard in non-operating position
(Fig.5)
so that the four teeth coincide with the four
grooves in the bearing seat
(Fig.6)
.
- Press the wheel guard down and rotate it clockwise
to the necessary operating position where the
wheel guard is fixed by lever L.
Rotating the wheel guard in a new operating posi-
tion
- Rotate the wheel guard clockwise only to the
necessary operating position where the wheel
guard is fixed by lever L
(Fig.7)
.
Removing the wheel guard
- Rotate the wheel guard in non-operating position
(Fig.6)
so that the four teeth coincide with the
four grooves in the bearing seat, and then draw it
upwards
(Fig.5)
.
AUXILIARY HANDLE
Normally auxiliary handle (7) is screwed on the machine
left side. It can be mounted also on the machine right
side if this is more convenient for the operator.
TURNING THE MACHINE CASE
The machine case can be turned to 90° or to 180°. The
first way of mounting is implemented when the machine
is used mainly for cutting, and the second - in case the
operator works better with his left hand. In both cases
the case turning must be carried out in a specialised ser-
vice centres for REDSTONE power tools.
RECOMMENDATIONS
For best results, it is recommended to use a 4 Ah battery.
When cutting, do not apply pressure, do not oscillate the
wheel. Work with moderate feed rate, suited to the mate-
rial to be machined.
The direction of cutting is very significant. The machine
must always be fed against the direction of wheel rota-
tion
(Fig.8)
. Otherwise, danger exists for the wheel to be
forced uncontrolled out of the cut.
When cutting profiles or rectangular pipes it is best to
start with the smallest cross section.
When grinding do not apply pressure to the processed
surface by rearing down on the machine but move
the wheel regularly backwards and forwards. Special
wheels shall be used for processing non-ferrous met-
als. Best results when roughing can be achieved with
the wheel inclined at 30
0
to 40
0
to the processed surface
Never use cutting wheels for roughing operations. Us
-
age of wheels thicker than 6 mm is not recommended.
Maintenance
WARNING:
Always be sure that the tool is
switched off and the battery cartridge is removed be
-
fore attempting to perform inspection or maintenance.
GENERAL INSPECTION
Regularly inspect all fasteners and ensure they are
properly tightened. Should any of the screws be loose,
retighten it immediately to avoid hazards.
CLEANING
For safe operation always keep the machine and its ven-
tilation slots clean.
Regularly check to see if any dust or foreign matter
has entered the ventilation slots and the grills around
the switches. Use a soft brush and/or air jet to remove
any accumulated dust. Wear safety glasses to protect
your eyes whilst cleaning.
Exterior plastic parts may be cleaned with a damp cloth
and mild detergent if necessary.
When operating in heavily dusty environment (cutting
stone) the ventilation slots and the switch slider of the
machine running at no load must be obligatory cleaned
after each shift by compressed air or by gently tap-
ping it near the ventilation slots with non-metal object
(Fig 9а,9b)
.
If the machine is equipped with a filter (6) on the venti
-
lation slots it has to be removed and cleaned and then
placed again on the machine.
Summary of Contents for RS 18Li E MA
Page 67: ...65 EL 65 67 68 69 73 73 75 76 REDSTONE REDSTONE REDSTONE...
Page 68: ...66 EL RS 18Li MA RS 18LiE MA M14 YYYY Www YYYY ww Li Ion 0 45...
Page 70: ...68 EL RS 18Li MA RS 18LiE MA 1 a b c 2 a b c d e f FI 3 a b c d e f g...
Page 71: ...69 EL 4 a b c d e f g 5 a b c d 6 a a b RS 18Li MA c d...
Page 72: ...70 EL RS 18Li MA RS 18LiE MA e f g h i j k l m n o...
Page 73: ...71 EL a b c d e a b c d e f...
Page 74: ...72 EL RS 18Li MA RS 18LiE MA a b c d e f a a b off REDSTONE...
Page 77: ...75 EL 6 L L 7 6 5 7 90 180 REDSTONE 8 30 40 6 mm 9 9b 6 REDSTONE...
Page 78: ...76 EL RS 18Li MA RS 18LiE MA REDSTONE REDSTONE...