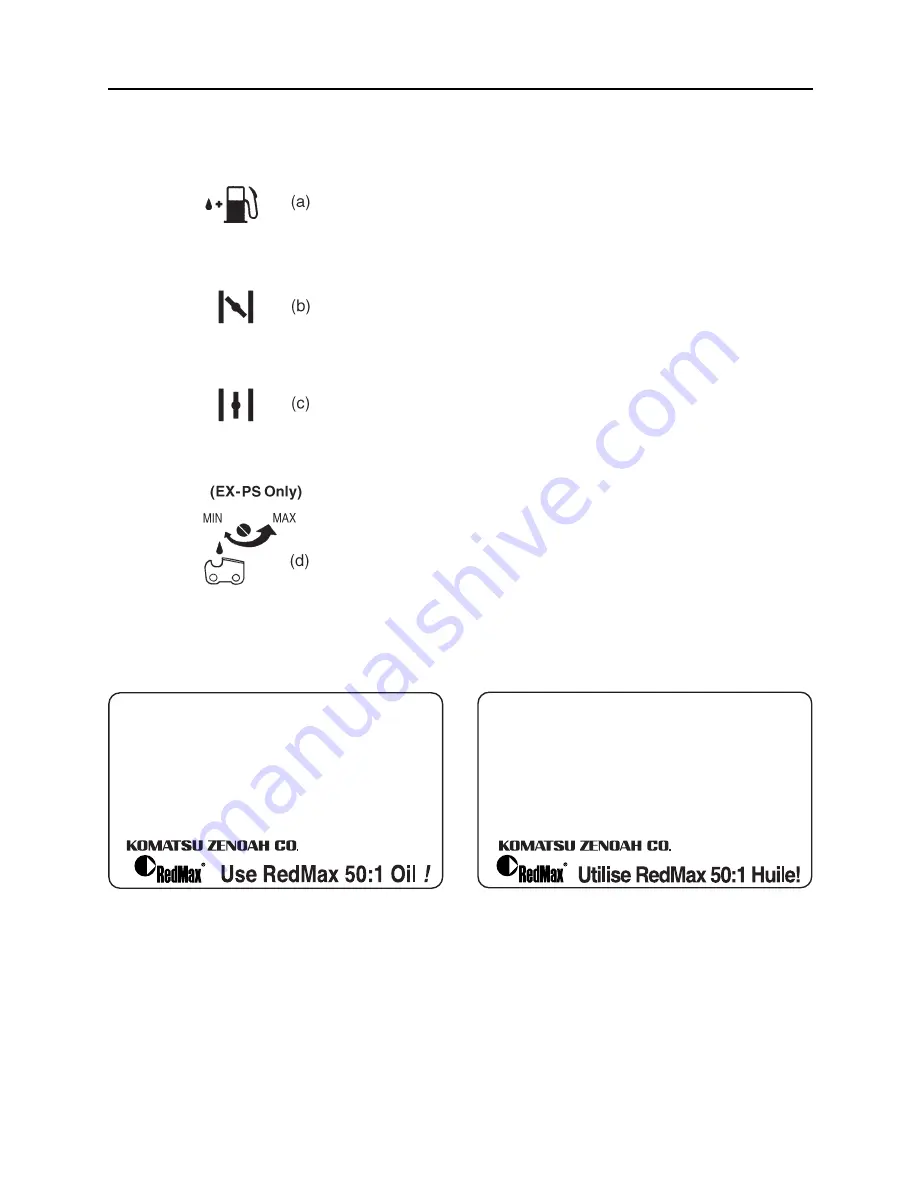
6
For safe operation and maintenance, symbols are
carved in relief on the machine. According to these
indications, please be careful not to make a
mistake.
(a) The port to refuel the "MIX GASOLINE"
Position:
FUEL TANK CAP
(b) The direction to close the choke
Position:
AIR CLEANER COVER
(c) The direction to open the choke
Position:
AIR CLEANER COVER
(d) If you turn the rod by screwdriver follow the
arrow to the “MAX” position, the chain oil flow
more, and if you turn to the “MIN” position, less.
Position:
Bottom of the GEAR CASE
4. Symbols on the machine
IMPORTANT ENGINE INFORMATION
THIS ENGINE MEETS U.S. EPA PH2 AND 2006
CALIFORNIA EMISSION REGULATIONS FOR SI
SORE’s. COMPLIANCE PERIOD : CATEGORY A
ENGINE FAMILY : 6KZXS.0244XY ; EM
ENGINE DISPLACEMENT : 24cc
REFER TO OWNER’S MANUAL FOR MAINTE-
NANCE SPECIFICATIONS AND ADJUSTMENTS.
MANUFACTURED:
MADE IN JAPAN
INFORMATION IMPORTANTE CONCERNANT LE MOTEUR
CE MOTEUR EST CONFORME AUX REGLEMENTS SUR LES
EMISIONS DE GAZ U.S. EPA PH2 ET 2006 DE LA CALIFORNIE
POUR UNE PERIODE DE CONFORMITE SI SORE: CATEGORIE A
TYPE DE MOTEUR : 6KZXS.0244XY ; EM
CYLINDREE DU MOTEUR : 24 cc
SE REFERER AU MANUEL DE L’UTILISATEUR POUR LES
SPECIFICATIONS D’ENTRETIEN ET LES REGLAGES.
FABRIQUE PAR :
MADE IN JAPAN
Summary of Contents for EXtreme EX-HE
Page 46: ...12 Parts list 46 Fig 1 EXZ PU S N 60300000 and up...
Page 48: ...12 Parts list 48 Fig 2 EX2 BC S N 50200000 and up...
Page 50: ...Fig 3 ENGINE UNIT 60100000 and up 50 12 Parts list...
Page 52: ...12 Parts list 52 Fig 4 EX LRT S N 000531 and up...
Page 54: ...12 Parts list 54 Fig 5 EX PS S N 000000 and up...
Page 56: ...12 Parts list 56 Fig 6 EX HE S N 000101 and up...