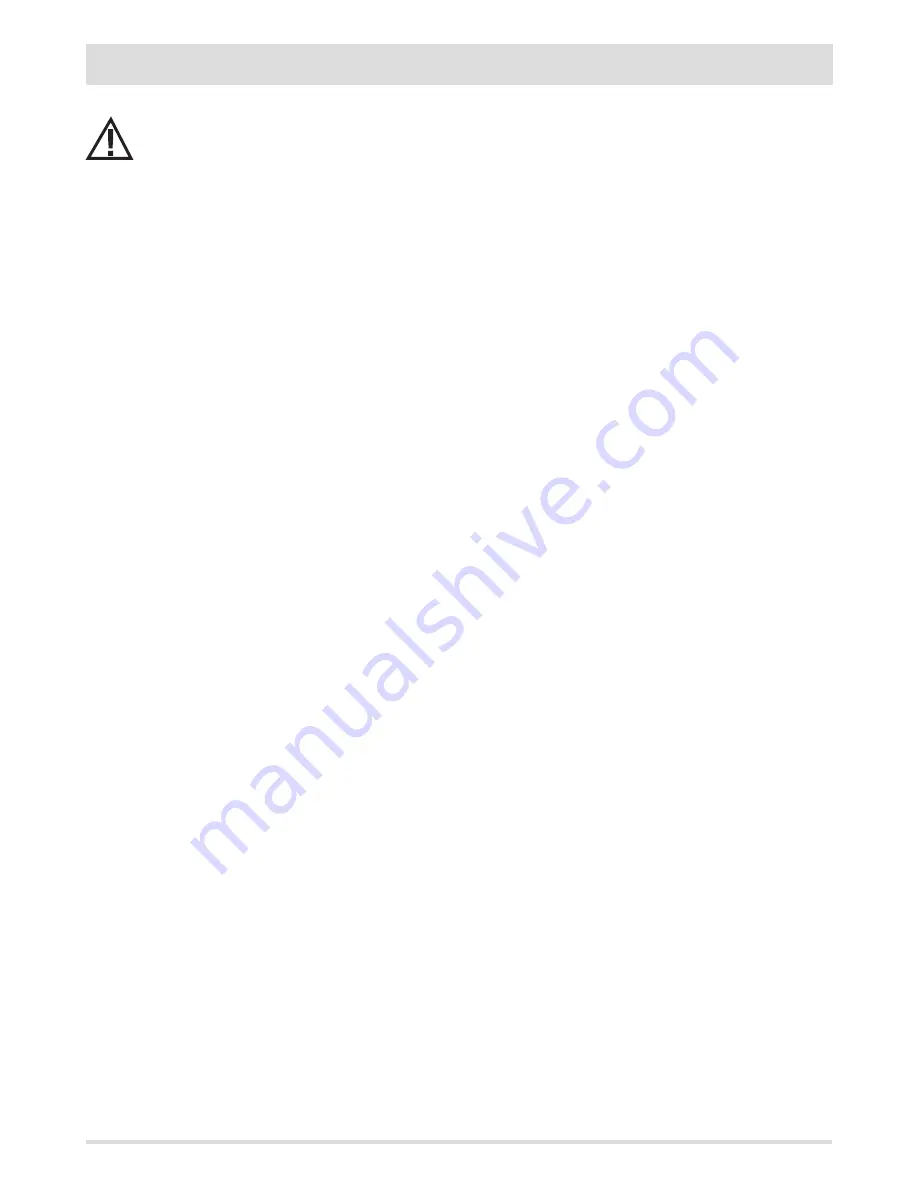
65
12-RECOMMENDATIONS FOR A SAFE USE
Technical Dept. - All rights reserved - Reproduction is prohibited
ONLY CORRECT INSTALLATION AND APPROPRIATE MAINTENANCE AND CLEANING OF THE APPLIANCE CAN GUARANTEE
CORRECT OPERATION AND SAFE USE OF THE PRODUCT
We would like to inform you that we are aware of cases of malfunctioning of domestic pellet-fuelled heating products, mainly due to
incorrect installation and use, as well as inadequate maintenance.
We would like to assure you that all of our products are extremely safe and certified according to European standards of reference. The
ignition system has been tested with the utmost attention to enhance ignition efficiency and to prevent any type of problem, even in the
worst operating conditions. In any case, like for any other pellet-fuelled product, our appliances must be installed correctly and undergo
regular periodical cleaning and maintenance to guarantee safe operation. Our studies show us that malfunctioning is mainly due to the
combination of part or all of the following factors:
• Brazier holes obstructed or brazier deformed, due to lack of maintenance and conditions which can cause delayed ignitions,
generating an anomalous production of unburned gases.
• Insufficient combustion air due to a reduced or clogged air inlet duct.
• Use of smoke ducts nonconforming to regulatory installation requirements, failing to guarantee an adequate draught.
• Partially clogged chimney, due to lack of maintenance, reducing the draught and making ignition difficult.
• End chimneypot nonconforming to the indications of the instruction manual, and therefore not suitable to prevent potential inverse
draught.
• This factor is crucial when the product is installed in especially windy areas, such as costal regions.
The combination of one or more of these factors could generate important malfunctioning conditions.
To keep this from occurring, it is fundamental to guarantee that the product is installed in compliance with standards in force.
Furthermore it is of the utmost importance to respect the following simple rules:
• Every time the brazier is removed for cleaning, it must always be put back properly in the work position before using the product,
completely removing any residual filth left on the support base.
• Pellets must never be loaded in the brazier manually, either before ignition or during operation.
• The accumulation of unburned pellets ensuing a failed ignition must be removed before repeating ignition. Also check that they are
fed correctly and that the combustion air inlet/smoke outlet are regular.
• If ignition fails repeatedly, immediately suspend use of the product and contact a qualified technician to check its operation.
Compliance with these indications is absolutely sufficient to guarantee proper operation and to avoid any type of problems with the
product.
If the above-mentioned precautions are not taken, and during ignition the brazier is overloaded with pellets thus generating anomalous
smoke in the combustion chamber, carefully follow the indications below:
• Do not disconnect electrical power to the product for any reason whatsoever: this would stop the smoke extractor, releasing smoke
into the environment.
• Take the precaution of opening the windows to ventilate the installation room from any smoke in the environment (the chimney
might not work properly).
• Do not open the fire door: this would compromise regular operation of the smoke extraction system to the chimney.
• Just switch the stove off by acting on the on-off button on the control panel (not the rear power supply socket button!) and move
away until smoke has completely evacuated.
• Before attempting re-ignition, clean the brazier and its air passage holes completely of all deposits and unburned pellets. Put the
brazier back in place, removing any residue from its support base. If ignition fails repeatedly, immediately suspend use of the product
and contact a qualified technician to check its operation and the chimney.