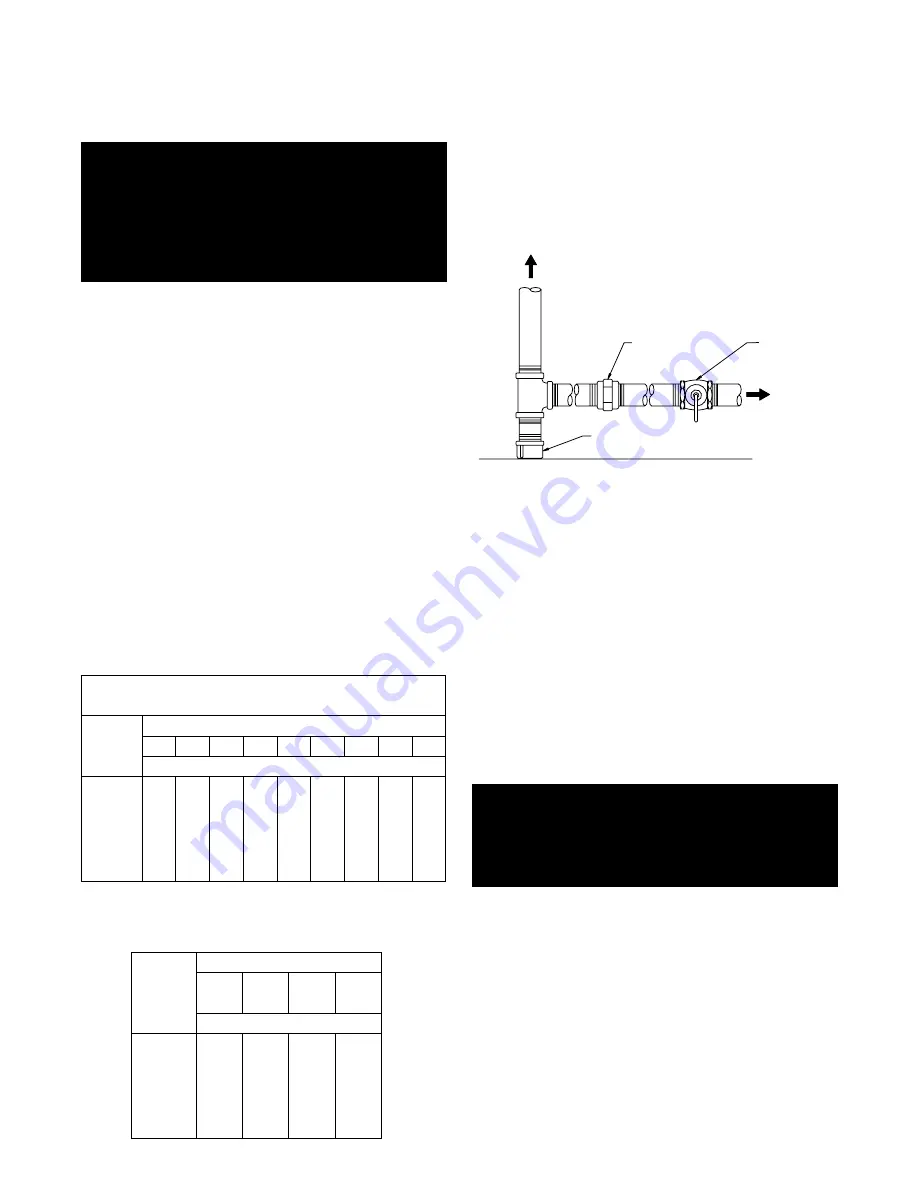
SERIES 8800 & 8900 INSTALLATION AND OPERATING INSTRUCTIONS
Page 13
30
285
590
890
1650
2700
4700
9700
Equivalent of pipe length (ft)
Maximum gas volume of pipe, (ft
3
/hr)
Pipe length in feet
A ground joint union should be installed between the
boiler gas controls and the supply piping. Each of these
items are needed to ensure long life and ease of
servicing. Always use a pipe sealant that is suitable for
use with LP gas.
Figure 7 - Gas Supply Piping
CAUTION: Always use a wrench on the gas valve
body when making gas connections to it. Never
over-tighten the piping entering the gas valve body
or gas valve failure may result!
When applicable, provisions for vent, bleed and gas
relief lines must be made in accordance with the latest
revision of ANSI Z223.1.
Safe lighting and other performance criteria were met
with the gas manifold and control assembly provided on
the boiler. All gas connections
MUST
be leak tested
before putting the boiler into operation.
WARNING: Never use an open flame to test for
gas leaks. Always use an approved leak
detection method. Failure to comply with this
warning can cause extensive property damage,
severe personal injury or death!
Whenever the gas supply piping is pressure tested the
boiler/water heater gas controls must be protected.
If the test pressure is equal to, or less than 1/2 psig (3.5
kPa) isolate the boiler/water heater by closing it’s manual
shut off valve, see Figure 16. If the test pressure is
greater than, or equal to 1/2 psig (3.5 kPa), disconnect
the boiler/water heater and its individual shut-off valve.
Table 6 - Gas Pipe Capacity
Nominal
Iron Pipe
Size, (in)
Nominal
Iron Pipe
Size, (in)
Maximum pipe capacity in ft
3
/hr based on 0.60 specific gravity gas
at a pressure of 0.5 psig or less and a 0.3" WC pressure drop.
1"
1 1/4"
1 1/2"
2"
2 1/2"
3"
4"
10
520
1050
1600
3050
4800
8500
17,500
20
350
730
1100
2100
3300
5900
12,000
40
245
500
760
1450
2300
4100
8300
50
215
440
670
1270
2000
3600
7400
60
195
400
610
1150
1850
3250
6800
80
170
350
530
990
1600
2800
5800
100
150
305
460
870
1400
2500
5100
150
120
250
380
710
1130
2000
4100
Gas
Cock
3
Gate
Valve
2
Tee
1
90°
Elbow
Type of pipe fitting
1"
1 1/4"
1 1/2"
2"
2 1/2"
3"
4"
5.2
6.9
8.0
10.3
12.3
15.3
15.3
0.6
0.8
0.9
1.2
1.4
1.8
1.8
1.5
1.9
2.3
3.0
3.7
4.5
4.5
Notes: 1. For flow through branch.
2. for flow at full open.
Note: Multiply the gas volume by 0.62 for propane flow capacity in ft
3
/hr.
Multiply the propane flow capacity by 2500 Btu/ft3 to determine the propane Btu/hr
capacity for a given pipe size and length.
Table 7- Equivalent Pipe Length Chart
GAS SUPPLY PIPING
WARNING: Check the boiler/water heater rating
plate to make sure that the boiler/water heater
is for the type of gas that will be used. If it isn’t,
do not connect the boiler/water heater to the gas
supply. Failure to comply with this warning can
result in extensive property damage, severe
personal injury or death!
The Series 8800 and 8900 come from the factory ready
to be piped to the gas supply. If for any reason the boiler/
water heater is not for the type of gas available at the
installation site, call the nearest RBI Water Heaters
representative to resolve the problem.
Table 6 should be used to ensure that the gas supply
piping is sized properly. If more than one appliance is
supplied by the same supply pipe, the piping must be
sized based on the maximum possible demand. Do not
neglect the pressure drop due to pipe fittings. Table 6
should be used in conjunction with Table 7 to ensure
that the gas supply piping has the capacity to meet the
demand.
Figure 7 depicts the proper way to connect the boiler/
water heater to the gas supply piping. Provide a
sediment trap at the bottom of the vertical section of the
gas supply pipe upstream of the gas controls.
2.6
3.5
4.0
5.2
6.2
7.7
7.7
TO GAS SUPPLY
CONTROL(S)
TO GAS
( TO EXTEND TO FLOOR )
SEDIMENT TRAP & DRIP LEG
SHUTOFF
GROUND
UNION
JOINT
MANUAL
VALVE