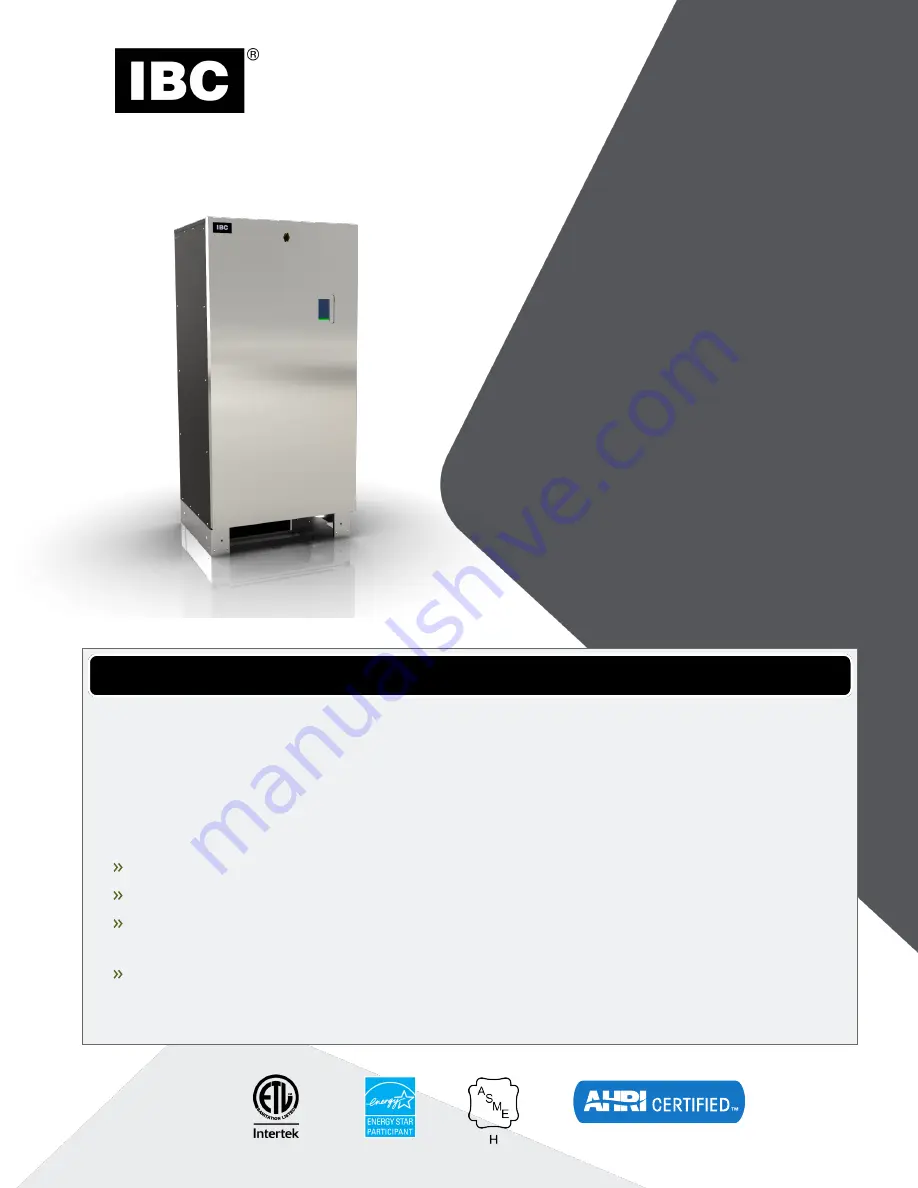
Installation and
Operating Manual
EX SERIES
Commercial Boilers
EX 700
EX 850
WARNING
If the information in this manual is not followed exactly, a fire or explosion may result causing
property damage, personal injury, or loss of life.
Do not store or use gasoline or other flammable vapors and liquids or other combustible
materials in the vicinity of this or any other appliance.
If you smell gas:
Do not try to light any appliance.
Do not touch any electrical switch; do not use any phone in your building.
Immediately call your gas supplier from a nearby phone. Follow the gas supplier’s
instructions.
If you cannot reach your gas supplier, call the fire department. Installation and service must
be performed by a qualified installer, service agency or the gas supplier.