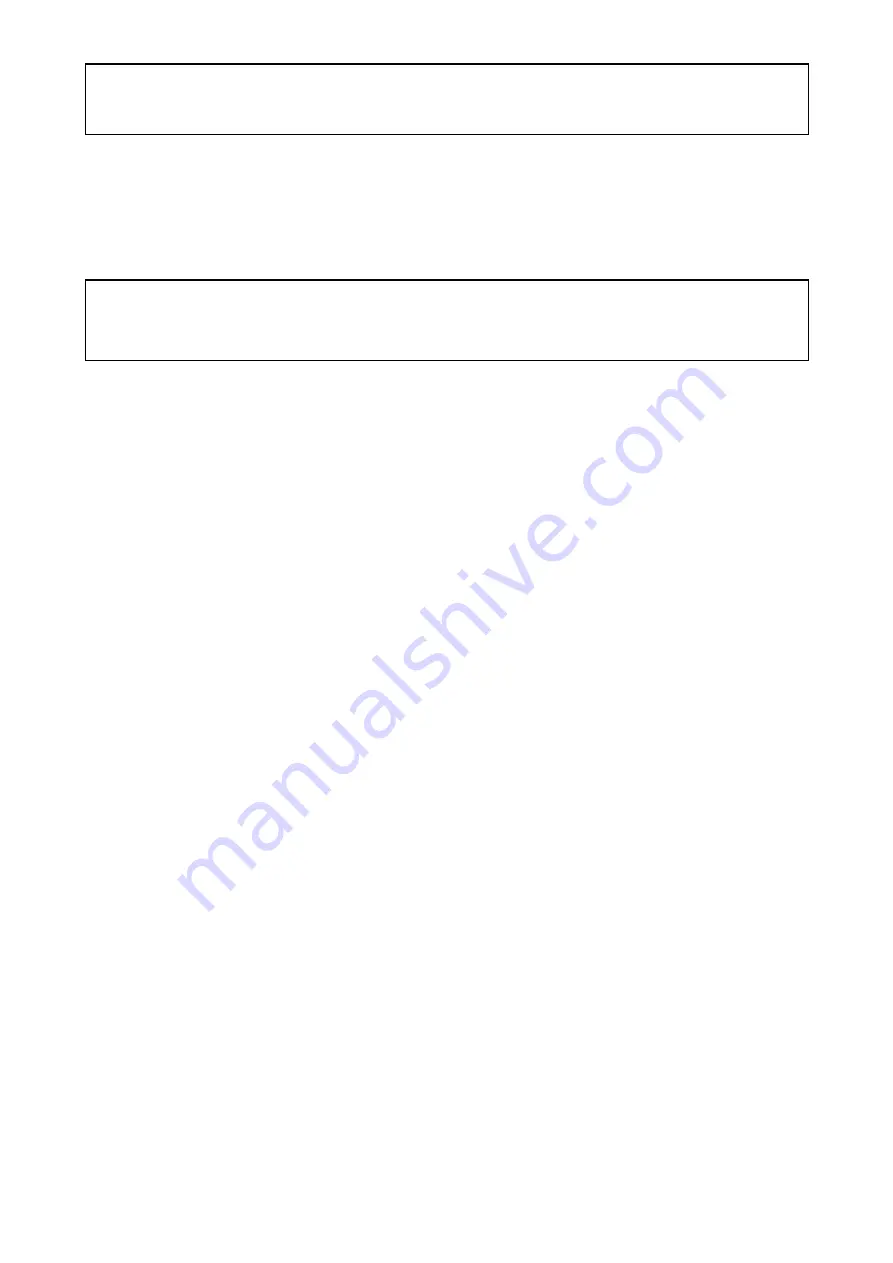
Note:
The ACU-100 and ACU-150 do NOT provide power to the SeaTalkng ® backbone. The backbone
requires a separate 12 V dc power supply.
Rudder angle reference sensor connection
A rudder angle reference sensor / transducer can be connected to the ACU to provide rudder angle
information to the autopilot system.
The connection of a rudder angle reference sensor / transducer is highly recommended, to help
ensure optimum autopilot performance.
Note:
The rudder angle reference sensor / transducer is not included with all autopilot products or
system packs. Consult the Raymarine website or your local dealer for a full list of the components
included with your autopilot system. The rudder angle reference sensor / transducer is also
available separately as M81105.
A rudder angle reference sensor / transducer converts its movement information to rudder angle
in +/- degrees.
Certain environmental conditions such as cross-current can cause the autopilot system to steer
persistently to port or starboard, even when the rudder is centered. With a rudder angle reference
sensor / transducer connected to your autopilot system, you can use an autopilot control head
to specify an offset angle in +/- degrees to compensate for inaccurate rudder angle information
caused by such conditions.
The more accurate the rudder angle information, the more accurately the autopilot system can
keep to a correct course.
The rudder angle reference sensor / transducer connection to the ACU connection panel is shown
below.
79
Summary of Contents for Evolution EV-1
Page 2: ......
Page 4: ......
Page 34: ...Item Description Quantity 4 Mounting screws 2 5 Document pack 1 34...
Page 36: ...5 1 Dimensions EV 1 and EV 2 36...
Page 37: ...5 2 Dimensions ACU 100 ACU 150 Product dimensions 37...
Page 38: ...5 3 Dimensions ACU 200 ACU 300 ACU 400 38...
Page 54: ...54...
Page 66: ...66...
Page 80: ...Item Wire color ACU 100 ACU 150 1 Red 2 Blue 3 Green 4 Gray screen 80...
Page 82: ...82...
Page 104: ...104...
Page 114: ...114...
Page 128: ...128...
Page 134: ...134...
Page 138: ......
Page 141: ......