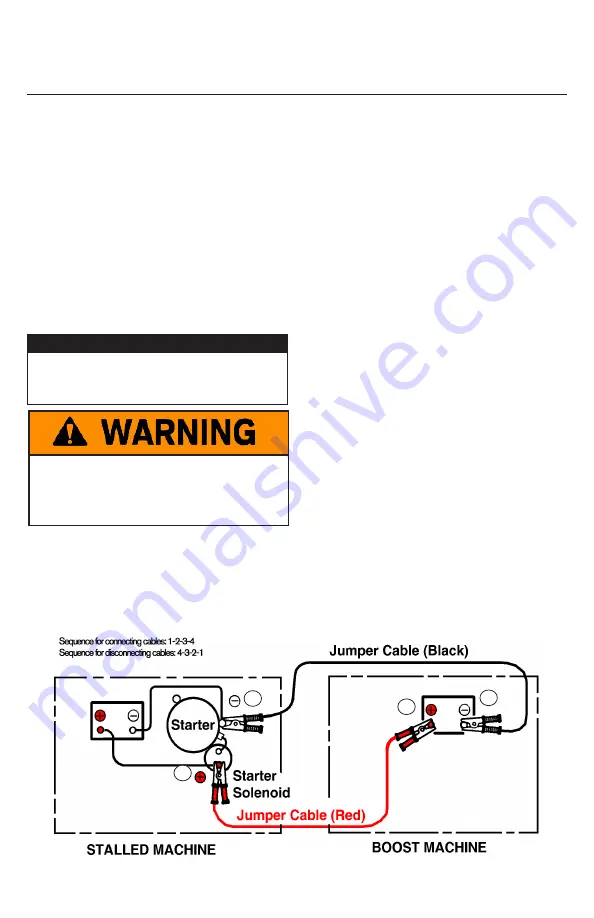
RG55R Operation • Service • Maintenance
800.392.2686
31
Operation
Starting With Jumper Cables
1. On the stalled machine, turn the start switch to OFF.
2. Move the boost machine near enough to the stalled
machine for cables to reach, but DO NOT ALLOW THE
MACHINES TO TOUCH.
3. Stop the engine on the boost machine.
4. Open the battery covers of both machines to purge
flammable fumes.
5. Remove all of the battery caps from the batteries (if not
maintenance-free type) on both machines, allowing
explosive vapors to disperse.
6. Connect jumper cables:
a. Connect the red positive (+) jumper cable to the
positive (+) terminal of battery of the stalled machine,
where the battery red positive (+) cable is already
connected. (Pull back rubber boot to gain access.)
b. Connect the other end of the red positive (+) jumper
cable to the positive (+) terminal of the battery of the
boost machine.
c. Connect the black negative (-) jumper cable to the
negative (-) terminal of the boost machine battery.
d. Connect the other end of the black negative (-) jumper
cable to the negative post of the stalled machine, where
the battery black negative (-) cable is already connected.
7. Start the engine on the boost machine and allow it to
run at high idling speed for about ten minutes. This will
partially charge the stalled engine’s battery.
8. Start the stalled engine.
9. Immediately after starting the stalled engine, disconnect
the jumper cables, in reverse order.
10. Reinstall the battery caps and battery covers.
11. After completion of the above procedure, perform failure
analysis on the starting/charging system of the stalled
machine as required.
NOTICE
Before attempting to start an engine that has been
in storage, check that all fluids are topped off and
clean.
DO NOT ALLOW JUMPER CABLE CLAMPS TO
TOUCH THE OTHER SOLENOID TERMINAL.
UNCONTROLLED STARTING OF THE ENGINE
WOULD OCCUR, WHICH COULD CAUSE
SEVERY INJURY OR DEATH!
1
2
3
4
Summary of Contents for RG55R
Page 27: ...RG55R Operation Service Maintenance 800 392 2686 27 Operation...
Page 58: ...RG55R Operation Service Maintenance 58 Hydraulic Schematic 805921...
Page 59: ...RG55R Operation Service Maintenance 800 392 2686 59 Hydraulic Schematic 805921...
Page 67: ...RG55R Operation Service Maintenance 800 392 2686 67 Specifications...