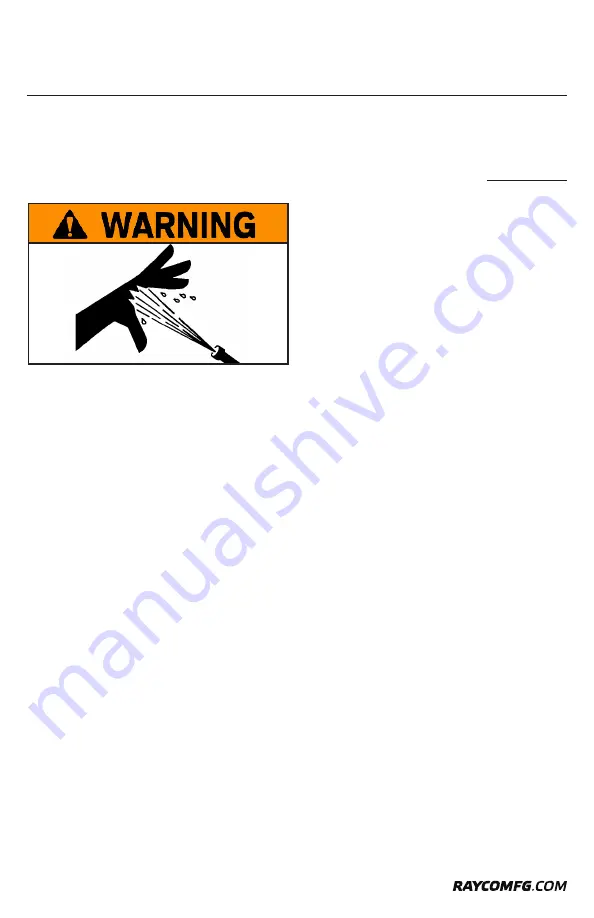
RG55R Operation • Service • Maintenance
14
Safety
Lines, Tubes and Hoses
Do not bend high pressure lines. Do not strike high pressure
lines. Do not install any lines that are bent or damaged.
Repair any lines that are loose or damaged. Leaks can
cause fires. Consult your Rayco dealer for repair or for
replacement parts.
Check lines, tubes and hoses carefully. Do not use your bare
hand to check for leaks. Use a board or cardboard to check
for leaks. Tighten all connections to the recommended torque.
Replace the parts if any of the following conditions are present:
• End fittings are damaged or leaking
• Outer coverings are chafed or cut.
• Wires are exposed.
• Outer coverings are ballooning.
• Flexible part of the hoses are kinked.
• Outer covers have embedded armoring.
• End fittings are displaced. Make sure that all clamps,
guards, and heat shields are installed correctly. During
machine operation, this will help to prevent vibration,
rubbing against other parts, and excessive hear.
Electrical Storm Injury Prevention
When lightning is striking in the vicinity of the machine, the
operator should never attempt to operate the machine. If you
are on the ground during an electrical storm, stay away from
the vicinity of the machine!
Before Operation
Safety information is available in English for this machine.
A list of some of the material is available in the Operation
and Maintenance Manual, “Reference Material”. Consult
your Rayco dealer in order to obtain copies of the material.
The information should be reviewed by every person that
operates the machine.
Clear all personnel from the machine and from the area.
Clear all obstacles from the path of the machine. Beware
of hazards such as wires, ditches, etc.
Make sure that all windows are clean. Secure all doors in the
closed position. Secure the windows in the open position
or in the shut position.
Call 811 Before You Dig. One free, easy call gets your utility
lines marked and helps protect you from injury and expense.
Know whats below, before you dig. Go to www.call811.com
for more details.
Guards (Operator Protection)
There are different types of guards that are used to protect
the operator. The machine and the machine application
determines the type of guard that should be used.
A daily inspection of the guards is required in order to check
for structures that are bent, cracked or loose. Never operate
a machine with a damaged structure.
The operator becomes exposed to a hazardous situation if the
machine is used improperly or if poor operating techniques
are used. This situation can occur even though a machine
is equipment with an appropriate protective guard.
Other Guards (If Equipped)
Protection from flying object and/or falling objects is required
for special applications. Logging applications and demolition
applications are two examples that require special protection.
A front guard needs to be installed when a work tool that
creates flying objects is used. Mesh front guards that are
approved by Rayco or polycarbonate front guards that are
approved by Rayco are available for machines with a cab or
an open canopy. On machines that are equipped with cabs,
the windshield should also be closed. Safety glasses are
recommended when flying hazards exist for machines with
cabs and machines with open canopies.
If the work material extends above the cab, top guards and
front guards should be used.
Additional guards may be required for specific applications
or work tools. The Operation and Maintenance Manual
for your machine or your work tool will provide specific
requirements for the guards. Consult your Rayco dealer for
additional information.
Precautions for Welding on FRAME with
ENGINE/MACHINE Electronic Control
Unit (ECU)
Important: ALWAYS disconnect Electronic Control Unit (ECU)
connectors, battery and engine control system-to-machine
ground before welding on engine or machine.
High currents or electrostatic discharge in electronic
components from welding may cause permanent damage
Safety Decals
The safety decals located on this machine contain useful
and important information which will help you to operate
your machine safely. The complete decal kit and location of
each decal is given in the “Parts” manual. For your protection,
Summary of Contents for RG55R
Page 27: ...RG55R Operation Service Maintenance 800 392 2686 27 Operation...
Page 58: ...RG55R Operation Service Maintenance 58 Hydraulic Schematic 805921...
Page 59: ...RG55R Operation Service Maintenance 800 392 2686 59 Hydraulic Schematic 805921...
Page 67: ...RG55R Operation Service Maintenance 800 392 2686 67 Specifications...