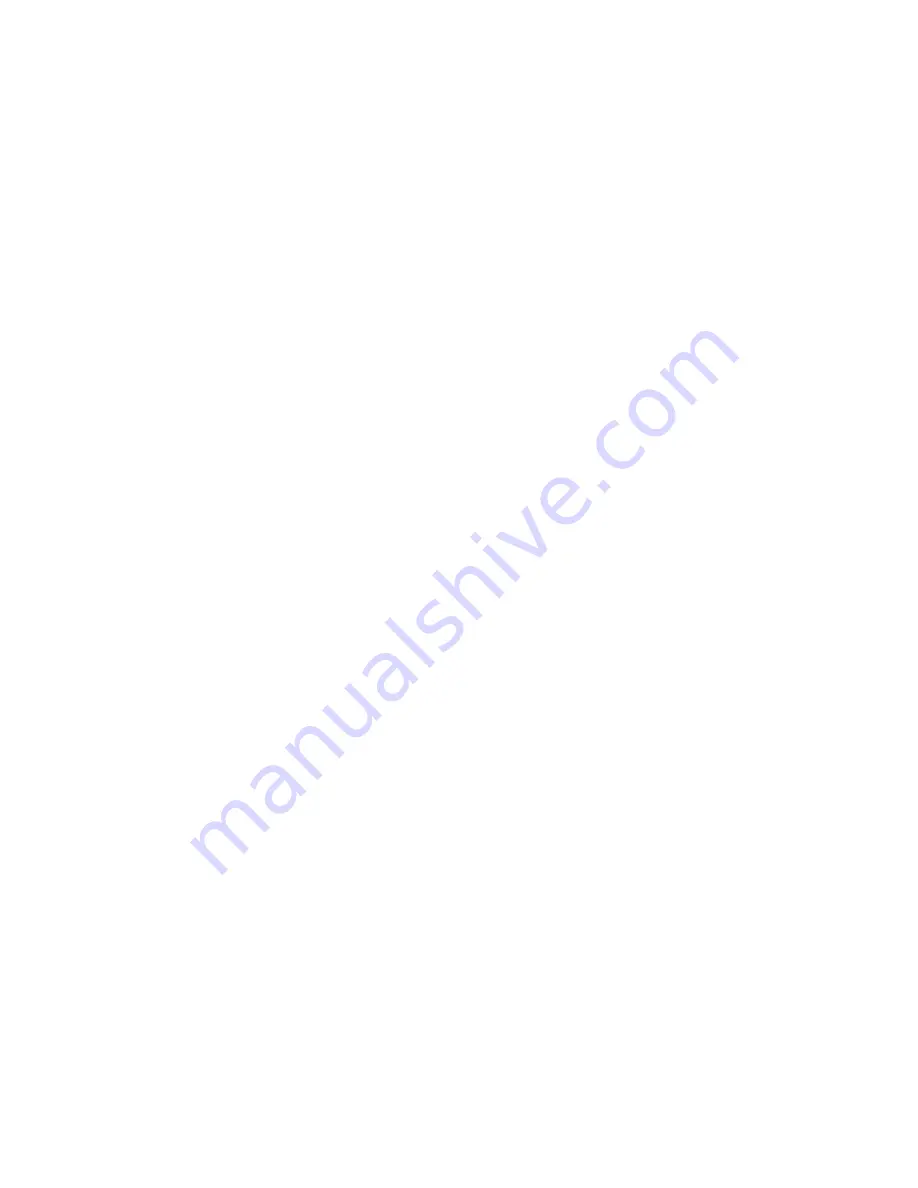
TO ENABLE SPEED
CONTROL
To enable speed control, first make sure the Pulse-
Track 2 is installed as detailed in the "Installation"
section of this manual.
Local Mode Operation
1. Turn the front panel Power ON/OFF switch
to the ON position.
2. Ensure the local/remote switch on the Atomiz-
er Card is in the local position.
3. Turn the front panel Master Control Switch to
the RUN position or activate the electrical master
enable input (see "Electrical I/O" in the "Installation"
section of this manual).
4. Activate the enable input for the given rotator
either by supplying air to the corresponding EN
input on the right side of the control panel or by
activating the corresponding electrical enable input
(see "Enable Inputs" in the "Installation" section
of this manual).
5. Using the Speed Select Thumbwheel Switch on
the Atomizer Card, set the desired speed setting
for the corresponding rotator and press the Speed
Enter Button.
6. Move the Atomizer Card Enable/Disable/Re-
set Switch to the enable position. Speed control
should begin on the rotator corresponding to the
selected atomizer card.
Remote Mode Operation
1. Set Dip Switch SW1-6 on the Control Card for
the desired mode of operation. For a 0-10VDC
input signal set SW1-6 to the OFF position. For a
4-20mA input signal set SW1-6 to the ON position
(see "Dip Switch Settings" in the "Installation "
section of this manual).
2. Turn the front panel Power ON/OFF switch to
the ON position.
3. Move the local/remote switch on the Atomizer
Card to the remote position.
4. Turn the front panel Master Control Switch to
the RUN position or activate the electrical master
enable input (see "Electrical I/O" in the "Iinstalla-
tion" section of this manual).
5. Activate the enable input for the given rotator
either by supplying air to the corresponding EN
input on the right side of the control panel or by
activating the corresponding electrical enable input
(see "Enable Inputs" in the "Installation" section
of this manual).
5. Supply a 0-10VDC or 4-20mADC input sig-
nal to the electrical I/O breakout terminal J2-A1
through J2-A6 corresponding to the given rotator
(see "Table 5" in the "Installation" section of this
manual).
6. Move the Atomizer Card Enable/Disable/Re-
set Switch to the enable position. Speed control
should begin on the rotator corresponding to the
selected atomizer card.
TO DISABLE SPEED
CONTROL
Speed control can be disabled using any of the
following methods:
1. Move the Atomizer Card Enable/Disable/Reset
Switch to the disable position. This will disable
speed control to the rotator corresponding to the
given Atomizer Card.
2. Deactivate the enable input for the given rotator
either by removing air from the corresponding EN
input on the right side of the control panel or by
deactivating the corresponding electrical enable
input (see "Enable Inputs" in the "Installation "
section of this manual). This will disable speed
control to the corresponding rotator.
Summary of Contents for Pulsetrack 2
Page 13: ...Figure 1 Typical Turbodisk 2 Installation With Temperature Humidity Cards...
Page 21: ...Figure 6 Electrical I O Breakout Terminal Locations...
Page 22: ...Figure 7 Control Panel Schematic...
Page 49: ...PARTS IDENTIFICATION Figure 17 Control Panel Front View...
Page 51: ...Figure 18 Control Panel Inside Door View...