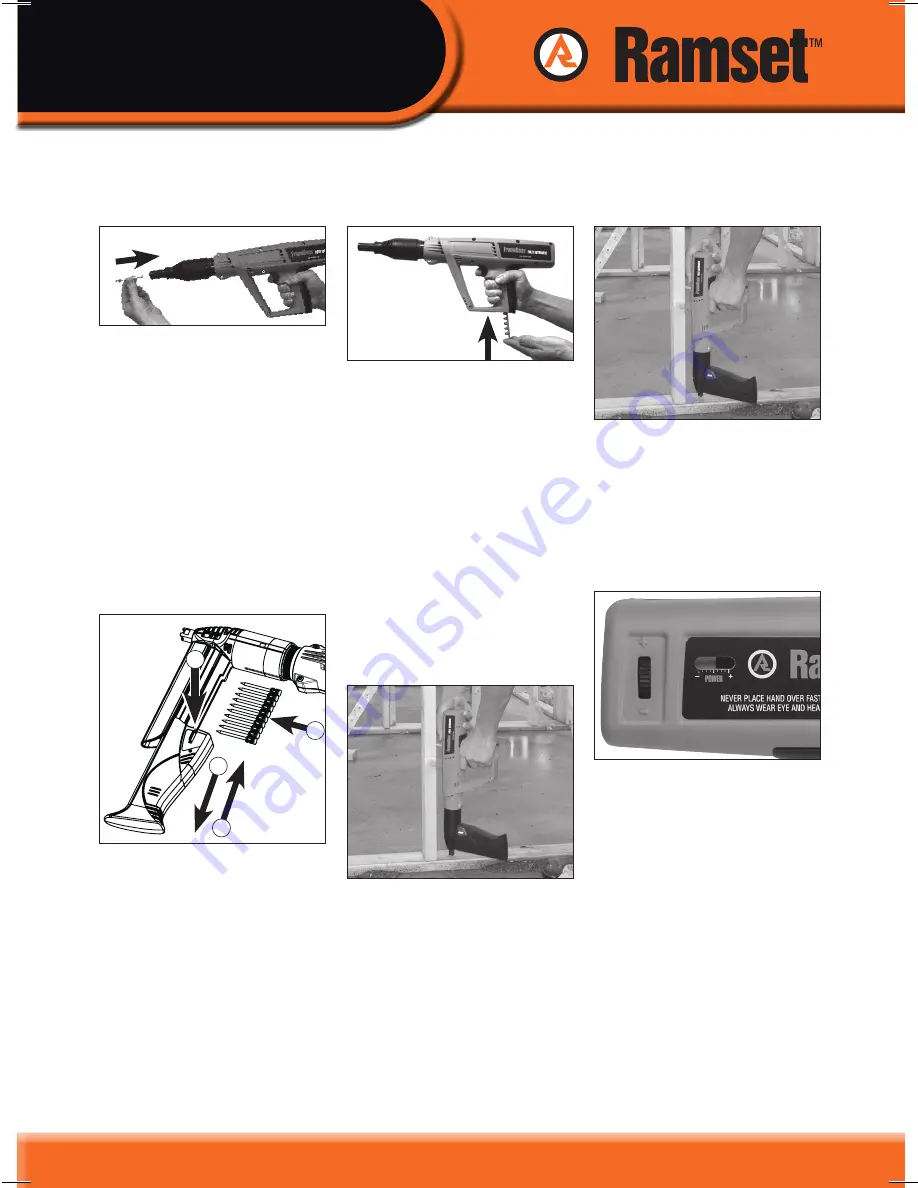
Frame
Boss
™
Instruction Manual
Standard Operating Procedure
Note: Refer to safety precautions before attempting to operate the tool.
4. Fire the tool.
Press the fastener guide firmly
against the work surface,
Call `FIRING’ to alert those
nearby, and pull the trigger.
5. Check the fastener has
been correctly set.
(See Fastener Setting, page 9)
3. Take up the correct firing
stance.
Make sure the tool is at right
angles (90º) in both directions
to the work surface. Your body
should be directly behind the
tool in a balanced posture.
6. Adjust the power, if
necessary.
Increase power by increasing
power setting. When maximum
setting is reached, move wheel
back to minimum position and
insert next strength power load.
7. Repeat steps 1,3,4,5 and 6
for the next fixing point.
8. repeat step 2 after every
10 fixings.
1b. Tool fitted with fastener
magazine.
1 - Press the magazine release
button.
2 - Slide the magazine cover
down.
3 - Insert Ramset™ collated
drive pins.
4 - Push the magazine cover
back into the closed
position.
2
4
3
1
2. Insert the power load.
With the tool in the closed
position insert a power load
strip into the cavity in the base
of the rubber handle and push
it in until the flat of your finger
tip is firmly against the handle
recess. The first power load is
now aligned with the chamber
prior to cocking.
note:
Always use the lowest
strength power load and lowest
power setting first, for a firing
test, then adjust the power to
suit the job.
PUSH
1. Select and insert the
fastener.
Select the correct fastener for
the application (see Fastener
Selection, page 7). Point the tool
down and away from yourself
and any other person.
1a. Tool fitted with single
shot fastener guide.
Insert a fastener, HEAD FIRST
into the fastener guide at the
front end of the tool, making
sure the fastener guide stays in
the forward position.
PUSH
10