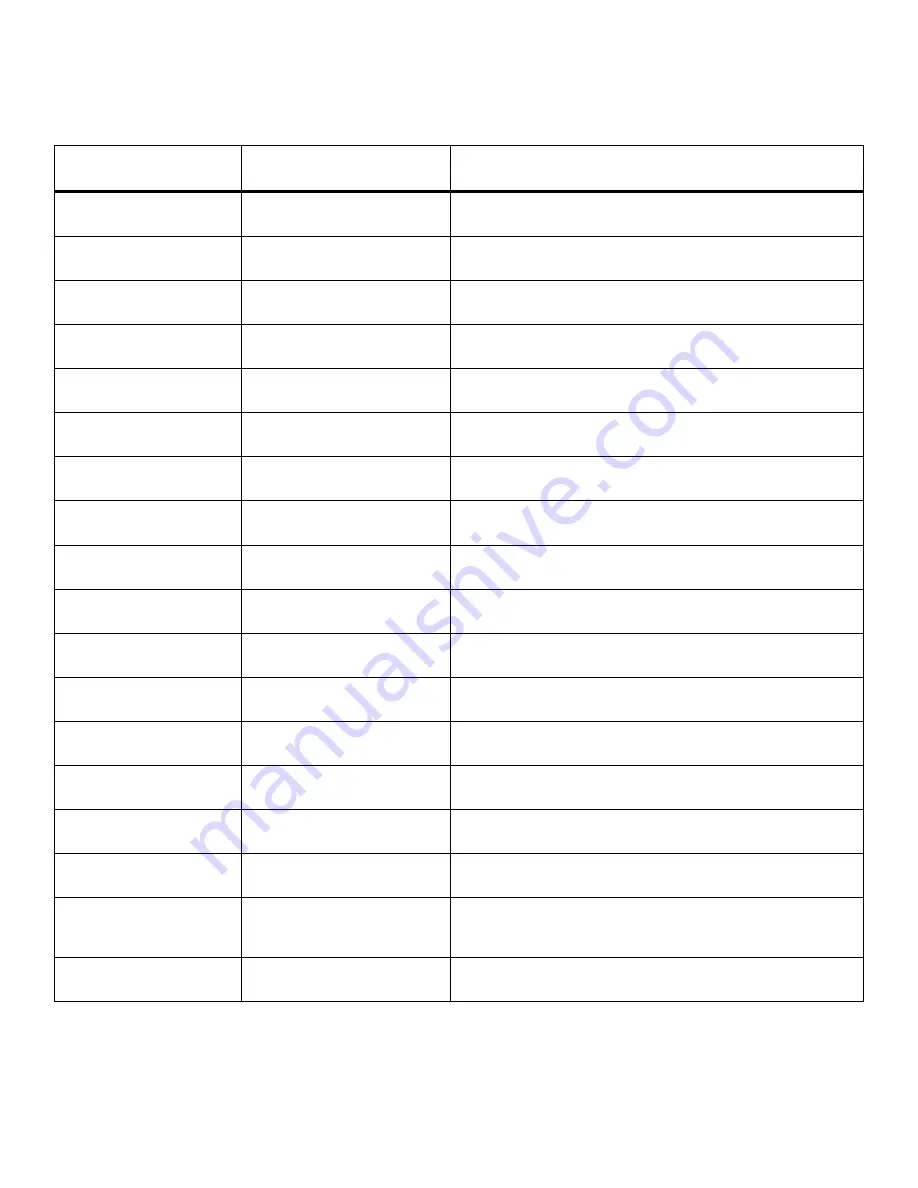
CONQUEST
®
WATER HEATER
53
PV500-71 02/16
18.2 LED Error Code Listing
The following table lists the errors detected by the Platform Ignition Module (PIM) control and the
associated LED indications.
Error Mode
LED Code
Recommended Troubleshooting
Normal Operation
Off
ID Card Fault
Red LED Steady ON,
Green Power LED OFF
Check that the proper ID card is securely connected.
Perform a power and system reset.
Internal Control
Failure
Steady ON
Perform a power and system reset. If fault remains,
replace the PIM.
Airflow Fault
1 flash
Check Blower operation and airflow switch.
False Flame Error
2 flashes
Check for proper gas valve closure. Clean burner and
electrodes.
Ignition Lockout Fault
3 flashes
Check the gas supply. See Table 6-1 for more
information.
Ignition Proving
Current Fault
4 flashes
Check HSI element. Replace with a new element of
the proper rating.
Low Voltage Fault
5 flashes
Check the 24 VAC input voltage. The voltage must be
above 18.0 VAC
Vent Temperature
Fault
6 flashes
Check for a blocked flue. Check the vent sensor and
connections.
Hi-Limit Fault
7 flashes
Check for proper water flow. Check hi-limit and outlet
sensors.
Sensor Fault
8 flashes
See the digital control display for fault identification.
Check sensors and wiring.
Safety #1 Fault
9 flashes
Check gas pressure. Verify proper safety switch
operation.
Water Pressure Fault
10 flashes
Check piping for leaks. Check pressure switch and
connections.
Blower Speed Fault
11 flashes
Verify tachometer signal and connection on J5.
LWCO Fault
12 flashes
Check LWCO switch and connections. Check the
water level.
Hi-Temperature Delta
Fault
13 flashes
Check pump operation. Confirm proper water flow
across heat exchanger.
Ft-bus
Communications
Fault
14 flashes
Verify the digital control display is connected and
operating. Check the cable between the control display
and J1.
Safety #2 Fault
15 flashes
Check gas pressure. Verify proper safety switch
operation.