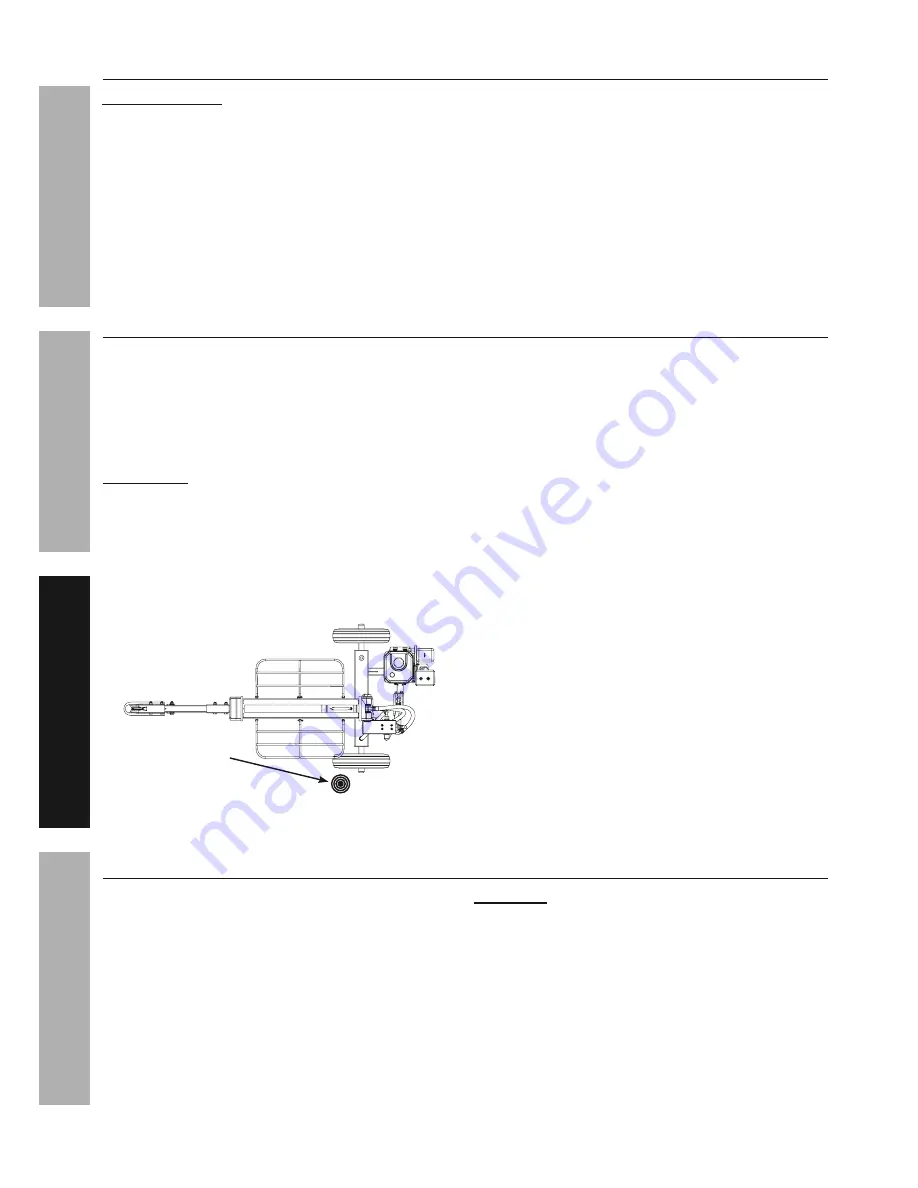
Page 14
For technical questions, please call 1-888-866-5797.
ITEM 61594
SAFETY
Op
ERA
TION
M
AINTENANCE
SETU
p
Break-in period:
a. Breaking-in the engine will help to ensure proper equipment and engine operation.
b. The operational break-in period will last about 3 hours of use. During this period:
• Do not apply a heavy load to the equipment.
• Do not operate the engine at its maximum speed.
c. The maintenance break-in period will last about 20 hours of use.
• Change the engine oil after this period.
Under normal operating conditions subsequent maintenance follows the
schedule explained in the
Maintenance
section on page 18.
Log Splitter Operating Instructions
1.
Check the hydraulic fluid level; fill as necessary.
2. Ensure that the Support Leg is down and place
wheel chocks (not included) on each side of the
wheels to keep the Log Splitter from moving.
3. Follow procedures in previous
section to start the engine.
IMpORTANT:
Hydraulic fluid temperature must be
above 10° F (-12° C) before operating the Log Splitter
or damage to the hydraulic pump may result. If outdoor
temperature is below 32° F (0° C) use the Control Handle
to cycle the Cutting Wedge forward and back several
times to warm the hydraulic fluid before splitting wood.
4. Stand in the correct operator position as shown
in Figure A when operating the Log Splitter.
Correct Operator
position
Figure A: Operator position
5. Hold the rounded, bark side of log and position
it lengthwise in the direction of the grain on the
Beam of the Splitter between the Log Cradles.
Place one end of log against the end plate.
6. The log must be stable so that it will split properly.
Hold the top of the log at its center, if safe to do so.
Release log once Cutting Wedge engages it.
7. Push the Control Handle forward to drive the
Cutting Wedge forward into the log, splitting it.
8. Remove split log pieces and place the next
log against the opposite end plate.
9. Push the Control Handle backward to
drive the Cutting Wedge in the opposite
direction into the log, splitting it.
10. Turn off the Log Splitter engine after use. Clean,
then cover the tool and store in a dry, level,
well-ventilated area out of reach of children.
Removing a Stuck Log
A log that is too stringy or tough to split completely
can become stuck on the Cutting Wedge if the
Wedge becomes embedded in the log and
the log doesn’t completely split and separate.
If this happens, follow the directions below.
1. Relieve pressure on log and end plate
by retracting Cutting Wedge slightly.
2. Turn the Engine Switch to its “OFF” position
and disconnect the spark plug cap.
3. Remove the stuck log from the Cutting Wedge
manually with a sledge hammer and pry bar.
WARNING!
Be extremely careful when removing
the log as pieces may fly off as they separate from
the Wedge. Never attempt to remove a stuck log
by using the hydraulic force of the Log Splitter,
modifying the Log Splitter, or adding attachments
to the Log Splitter. Personal injury could result
from log or metal pieces flying out at high speed,
or the Log Splitter could become damaged.
4. Do not attempt to re-split a stuck log once it
has been removed from the Wedge. Manually
split with a maul, or cut with a chainsaw.
Starting the Engine (continued)