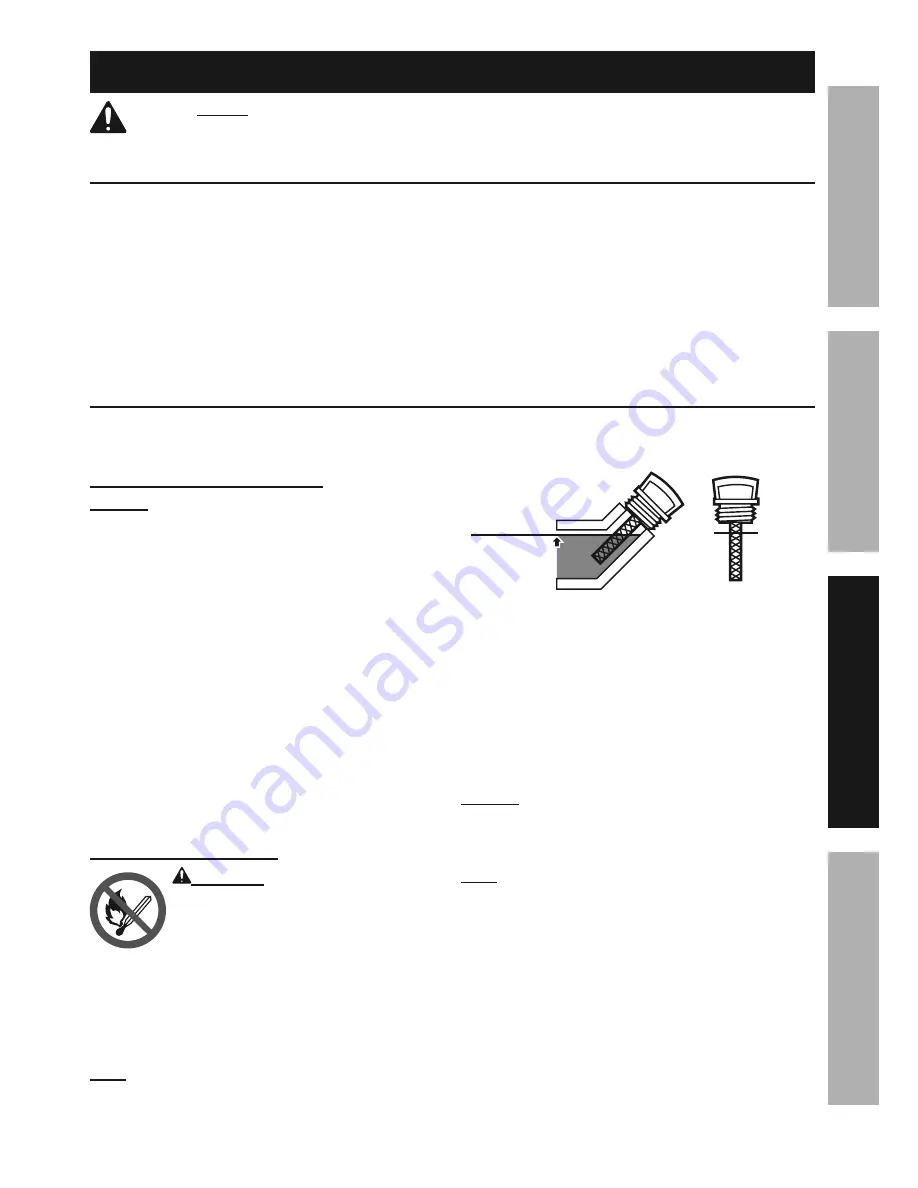
Page 11
For technical questions, please call 1-888-866-5797.
ITEM 61594
SAFETY
Op
ERA
TION
M
AINTENANCE
SETU
p
Operation
Read the ENTIRE IMpORTANT SAFETY INFORMATION section at the beginning of this manual
including all text under subheadings therein before set up or use of this product.
Workpiece and Work Area Set Up
1. Designate a work area that is clean and well-lit.
The work area must not allow access by children
or pets to prevent distraction and injury.
2. There must not be objects, such as utility lines,
nearby that will present a hazard while working.
3. Maximum log size for this Log Splitter is
23.6" long and 8" in diameter. Attempting to
cut logs that exceed those measurements is
dangerous and may damage the Log Splitter.
4. Use a chainsaw (not included) to cut logs
square on each end before splitting. Log ends
that are not cut square can slide out while
splitting and cause a safety hazard or cause
excessive force to Log Splitter components.
5. Do not split wood containing foreign objects
(nails, for example). Do not use odd-shaped,
uneven logs or logs that are knotted or curved.
Engine and Equipment pre-Start Checks
Inspect engine and equipment looking for damaged, loose, and missing parts before set up and starting.
If any problems are found, do not use equipment until fixed properly.
Checking and Filling Engine Oil
NOTICE: Your Warranty is VOID if the engine’s
crankcase is not properly filled with oil before
each use. Before each use, check the oil level.
Do not run the engine with low or no engine oil.
Running the engine with no or low engine oil
WILL permanently damage the engine.
1. Make sure the engine is stopped and is level.
2. Close the Fuel Valve.
3. Clean the top of the Dipstick and the
area around it. Remove the Dipstick
by threading it counterclockwise, and
wipe it off with a clean, lint free rag.
4.
Full level
Full level
Reinsert the Dipstick without threading it in and
remove it to check the oil level. The oil level
should be up to the full level as shown above.
5. If the oil level is at or below the low mark add the
appropriate type of oil until the oil level is at the
proper level. SAE 10W-30 oil is recommended
for general use. (The SAE Viscosity Grade chart
on page 20 in the Service section shows other
viscosities to use in different average temperatures.)
6. Thread the dipstick back in clockwise.
NOTICE: Do not run the engine with too little oil.
The engine will be permanently damaged.
Checking and Filling Fuel
WARNING!
TO pREVENT SERIOUS
INJURY FROM FIRE:
Fill the fuel tank in a well-ventilated area
away from ignition sources. If the engine
is hot from use, shut the engine off and
wait for it to cool before adding fuel. Do not smoke.
1. Clean the Fuel Cap and the area around it.
2. Unscrew and remove the Fuel Cap.
3. Remove the Strainer and remove any dirt
and debris. Then replace the Strainer.
Note: Do not use gasoline containing more than
10% ethanol (E10). Do not use E85 ethanol.
Note: Do not use gasoline that has been stored in a
metal fuel container or a dirty fuel container. It can
cause particles to enter the carburetor, affecting
engine performance and/or causing damage.
4. If needed, fill the Fuel Tank to about 1 inch
under the fill neck of the Fuel Tank with
87 octane or higher unleaded gasoline.
5. Then replace the Fuel Cap.
6. Wipe up any spilled fuel and allow excess
to evaporate before starting engine.
To prevent FIRE, do not start the engine
while the smell of fuel hangs in the air.