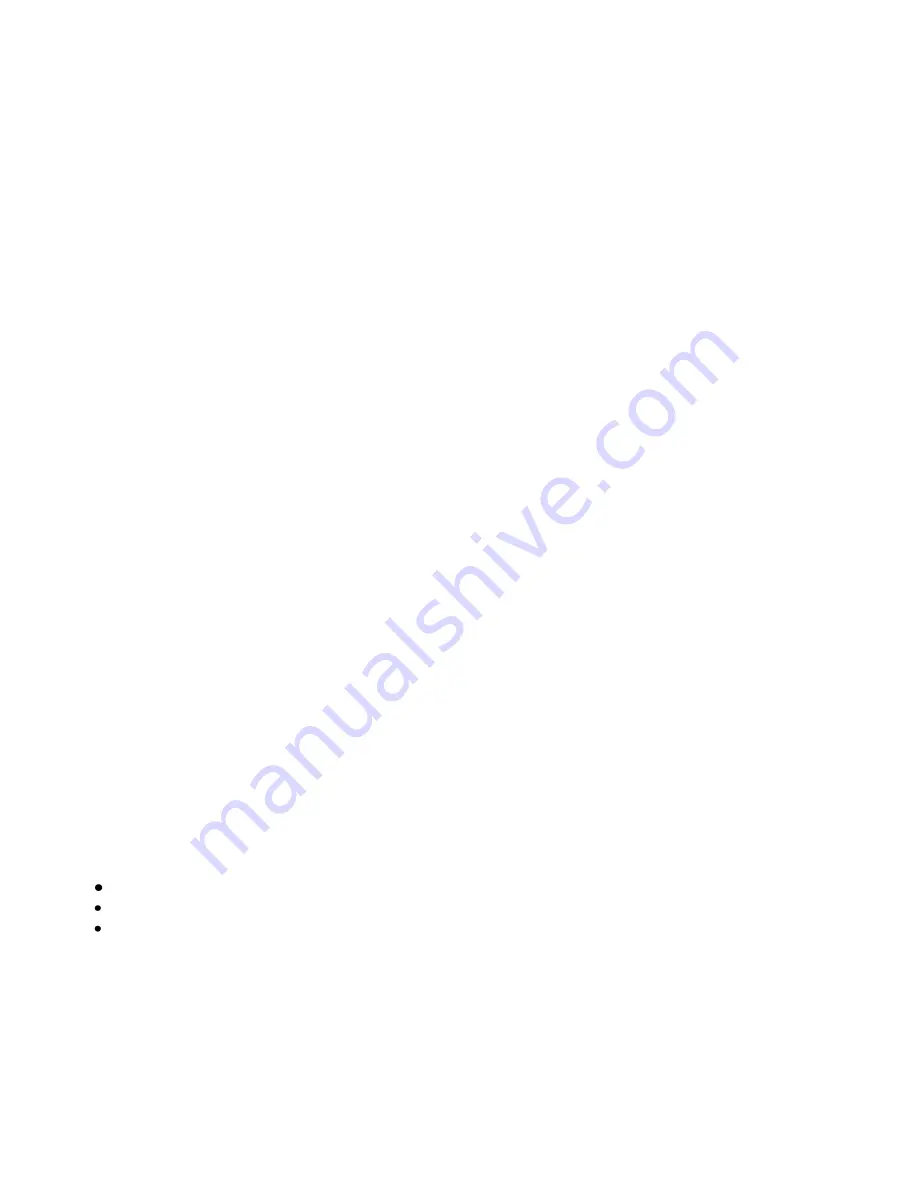
6
3.1.2
Install the safety relief valve(s) on the pipes provided. Plumb the relief valve outlet connections full size to the floor
drain. Check local codes for proper safety valve discharge for steam boilers above 15 psi, which normally are required to
be piped to overhead discharge outside safely away from personnel.
3.1.3
Hot water boilers may be equipped with an air vent pipe on the top of the boiler. Plumb this connection to the
expansion tank or install an automatic air vent on this pipe
.
3.1.4
The direction of flow through hot water boilers and water heaters must be from the inlet to the outlet (IE: bottom
to top). Do not reverse these connections.
NOTE: Do not oversize feedwater piping and values on steam boilers, as this may result in severe pressure fluctuations
during feedwater cycles if the fill rate is too rapid.
3.2 Electrical Connections
3.2.1 Power Feed Wiring
The recommended wire size is listed on both the unit’s Bill of Material (BOM) and the Wiring Diagram (WD). Also, the full
load amperage and maximum voltage are stamped on the unit’s nameplate. The feeder must be sized for 125% of the
full load amperage in accordance with Article 424-3 of the NEC. The wiring must have insulation rated
75°C or greater. Copper wiring is recommended for all power connections. The recommended size is noted in the ‘Notes”
on the wiring diagram.
CAUTION: Do not exceed the maximum voltage as listed on the nameplate. For resistance loads, amperage increases
proportionally with voltage.
3.2.2 Equipment Grounding Conductors
The unit is equipped with grounding lugs(s) inside the power panel(s). The grounding conductors must be installed and
sized in accordance with NEC Article 424-14. The recommended size is noted in the “Notes” on the diagram.
3.2.3 Control Wiring
Alteration of, or additions to, control wiring may void both the Underwriters Laboratories Listing and the Manufacturer’s
Limited Warranty. Field-installed controls, control connections, and modifications must be approved in writing by the
Factory.
NOTE:
All power connections are 3-Phase, 3-Wire. (Exception: If unit is single phase.) There is no provision for a neutral
connection; (IE: the unit should not be wired ‘wye’ or ‘star’
).
3.3 Filling the System
3.3.1
The system and the boiler / water heater must be thoroughly flushed before the final fill. Steam boilers should be
“boiled out” before operation.
3.3.2 Water Treatment
Consult a local water treatment firm for recommendations on proper water treatment and boilout procedure to prevent
damage to the boiler vessel, components and heating elements. The internal materials of boilers are Steel, Incoloy and
Cast Iron, which all are compatible with standard boilout compounds. In lieu of a commercial boilout compound, the
following mix of chemicals can be used for every 1,000 gallons of water:
30 lbs. TSP (tri-sodium phosphate; Na
3
PO
4
), commonly found in many building supply centers
.
5 lbs. caustic soda (50% pure sodium hydroxide; NaOH)
2 lbs. ordinary powdered laundry detergent. (Example: Tide)
These chemicals should be dissolved in warm water prior to their addition to the boiler. The boiler should be heated for at
least 3 hours, then drained and flushed
.
NOTE:
Standard hot water boilers are suitable for ethylene glycol mixtures up to a 50/50 mix
.