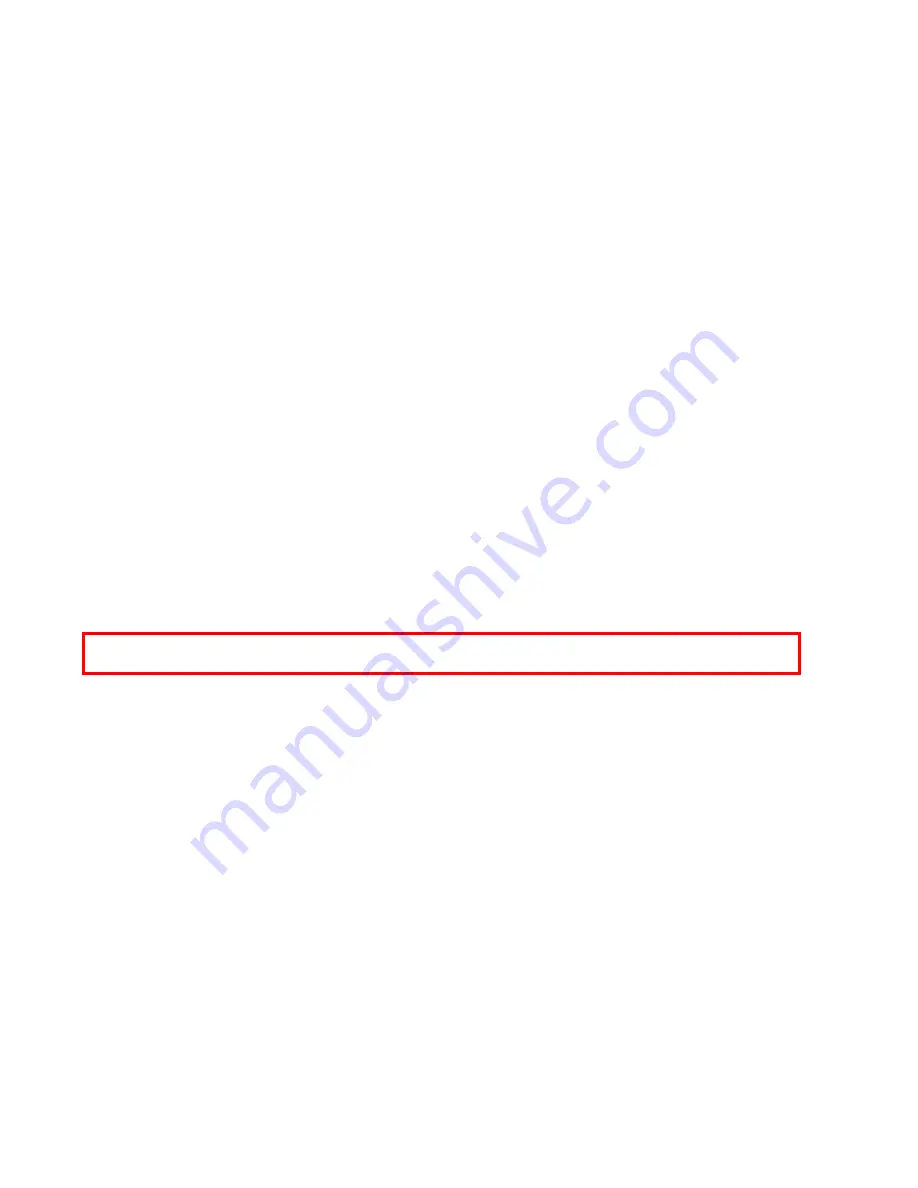
13
8.3 Electrical System Maintenance
8.3.1
Clean the control cabinets periodically (as often as needed) to keep both the interior and the exterior
free of dust, moisture and foreign matter. The interior cleaning of the electrical panels must be done with the
POWER OFF!
NOTE:
For units supplied with control cabinet cooling fans, the condition of the fan
filter must be periodically
checked and the filters cleaned or replaced as necessary.
8.3.2
With the POWER OFF, periodically check the tightness of electrical connections; particularly at power
entrance lugs, fuses (line side) and contractors (load side). This should be done at time of commissioning, at 7 –
14 days thereafter and at least annually. Replace any components that show signs of heat damage (IE:
discoloration, charring, melted insulation, etc
.).
8.3.3
Inspect the condition of the contactors. Look for burned or corroded contacts or overheated coils and
wires. If the contactors chatter or hum during operation, they should be either disassembled and cleaned to
remove dust or other foreign material in the mechanism or replaced.
8.3.4
Inspect the heating elements. Make sure that the terminal contacts are tight, clean, and corrosion-free.
8.3.5
Check all the wiring throughout the unit for frayed or brittle insulation. Replace any wiring showing
insulation degradation.
8.4 Boiler Mechanical System Maintenance
8.4.1
With the POWER OFF, remove the element access covers. Inspect all internal vessel connections,
particularly at the heating elements. Spot check torque on element flange bolts. The acceptable torque range is
10 – 15 ft. lbs
.
CAUTION: Do not over tighten elements
!
8.4.2
Remove and replace any leaking elements or element gaskets. Inspect
handhole and manhole gaskets. If
these gaskets are brittle, they should
replaced.
WARNING:
Over-torquing of the elements nuts will damage the element gasket.
8.4.3
Repair any leak at any place on the unit or adjacent piping. Re-torque flange bolts on system piping.
8.4.4
For all boilers, the interior of the pressure vessel must be inspected at least once a year. If there is any
presence of scale, refer to ‘Preventative Maintenance Water Treatment’ above a consult a local water
treatment firm immediately. Scale formation on the elements will cause heating element failures. Scale
formation elsewhere in the boiler can cause erratic control operation / failure, particularly on water level
controls
.
8.4.5
When the boiler is inspected, rod out the pipes to the water column(s) and inspect the operation of the
float(s) in the level controller(s
).
8.4.6
Remove and clean the low water cutoff probe.
8.4.7
Steam Boiler Special Maintenance
8.4.7.1
All PRECISION steam boilers are supplied with a surface blow-off connection. If surface blowoff valves
are not Factory-installed, they should be installed in the field. The surface blow-off should be used as often as
necessary to remove organics which accumulate at the water surface, and to limit TDS. (Boiler
water TDS
should not exceed 3500 ppm
).
8.4.7.2
Both the boiler and water column should be blown down periodically to remove bottom sludge
.
8.4.7.3
The water column should be blown down daily to assure proper operation of the level control / LWCO
assembly
.
8.4.7.4
Water Treatment