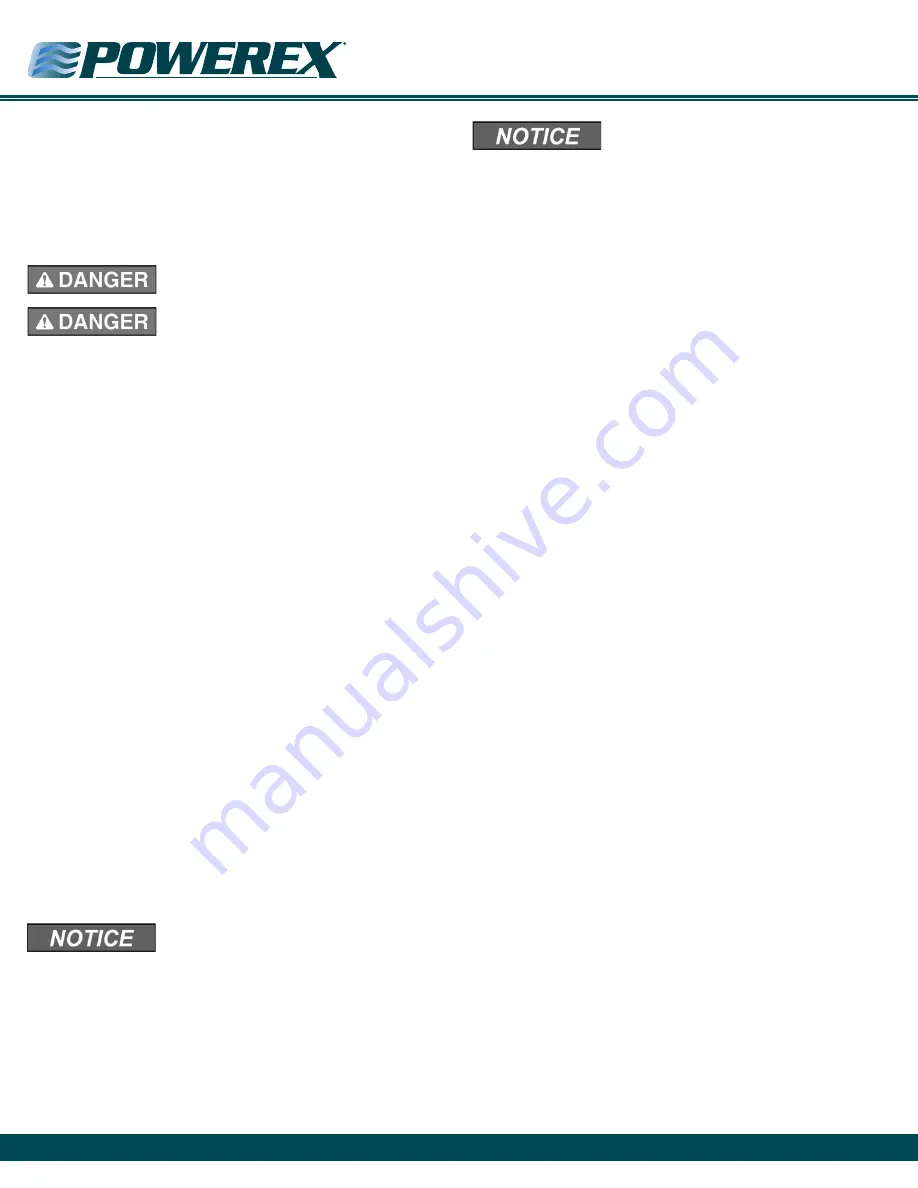
Medical Air & Laboratory Air Systems – 7.5 & 10 HP Pumps
Powerex
•
150 Production Drive
•
Harrison, OH 45030
•
USA
P 1.888.769.7979
•
F 513.367.3125
•
www.powerexinc.com
IN594402AV
•
06/2017
Page 4 of 28
Wiring
Lock out and tag out the electrical supply before
servicing the equipment.
requirements.
Electrical shock hazard. Make sure the system
is grounded in accordance with NEC and local
All electrical hook-ups must be performed by a qualified electrician.
Installations must be in accordance with local and national electric
codes. Make sure power supply conductors are sized adequately for
full system demand.
Use solder-less terminals to connect the electrical power source.
Piping
General Guidelines
Refer to the general product manual.
1. Make sure the piping is lined up without being strained or
twisted when assembling the piping for the system.
2. Appropriate expansion loops or bends should be installed at
the system to avoid stresses caused by changes in hot and cold
conditions.
3. Piping supports should be anchored separately from the
system to reduce noise and vibration.
4. Never use any piping smaller than the system outlet connection.
5. Use flexible hose to connect the outlet of the system to the
piping so that the vibration of the system does not transfer to
the piping.
Remote Intake Piping
Powerex Compressor Medical and Laboratory Air Systems with
7.5 and 10 HP pumps are constructed manifolds with a single point
connection for remote air intake. Piping for remote intake system
must be installed at the final operating site. Under some conditions,
the intake piping may facilitate the condensation of humidity in the
intake air stream into liquid water.
water going into the pumps will damage the pumps and void the warranty.
The intake filters supplied by Powerex will not
stop ingestion of liquid water by the pumps. Liquid
Always install drip legs with sufficient capacity to capture liquid
water in the intake piping before the system connection points. Drip
legs must be sized with low enough air velocity to make sure they
are effective at capturing liquid water in the intake air and must be
maintained (drained) at frequent intervals to make sure they remain
effective.
take up any slack, but do not crush the pad. Pads are most effective
when they are lightly loaded.
In some cases alternate isolation devices may be preferred. Install
them according to the recommendations of the device manufacturer.
If desired, additional support points may be selected and holes drilled
in the base as needed to accommodate the design.
auto. Operation with closed valves will damage the pump. The intake
isolation valves have had the handles removed and a handle or handles
are provided inside the electrical panel. Powerex strongly recommends the
valves opening and closing be controlled to avoid pump damage.
Intake isolation valves must never be closed
when the connected compressor is running or in
Safety Valves, Pressure Vessels, and Piping
1. Powerex systems are shipped with ASME safety valves sized so
that the maximum system flow is less than the capacity of the
valve or valves at the rated pressure. The rated pressure of the
valve is equal to or less than the maximum allowable working
pressure of the vessel or upstream pressure bearing parts. DO
NOT MODIFY or install any valves with different specifications
unless appropriate evaluations are completed. Do not modify
the structure of the pressure vessel or weld on the vessel.
2. Do not install any shut off valves between the safety valve
and the vessel or between the compressor pump and the
first system safety valve. Doing so can result in a dangerous
condition and lead to death or injury.
3. Do not install shut off valves in the system that create trapped
compressed air.
4. Manually operate the safety valve every six months or 2,500
operating hours to provide assurance that the mechanism is
free to operate. Replace valve if it is leaking when it is closed
or if it fails to vent when actuated.
5. Any piping or pressure bearing connection hose or tubing used
in the system must be rated equal to or higher than the safety
valve pressure rating. Inadequate pressure rating could result
in bursting.
Modular Placement
1. Unpack each frame module and discard or recycle all wood
shipping materials.
2. Systems consist of multiple frame modules. The steel base
platforms are intended to be bolted to the floor as shown in
the design drawings and connecting hoses provided (found in
the parts pack box). Systems may be placed on isolation pads
if desired. Modules may be spaced farther apart without any
structural problems, but electrical connections may need to be
modified—additional isolation pads and longer hoses may be
needed.
3. Place frame modules at location designated on build drawing.
Provide sufficient clearance around system for servicing (see
minimum clearance section).
Connecting Piping
1. Locate connection for piping at rear of compressor module to
receiver tank module.
2. Remove plastic caps or adhesive covering on ports and
connectors.
3. Connect flex line to the ports making sure each flex line is not