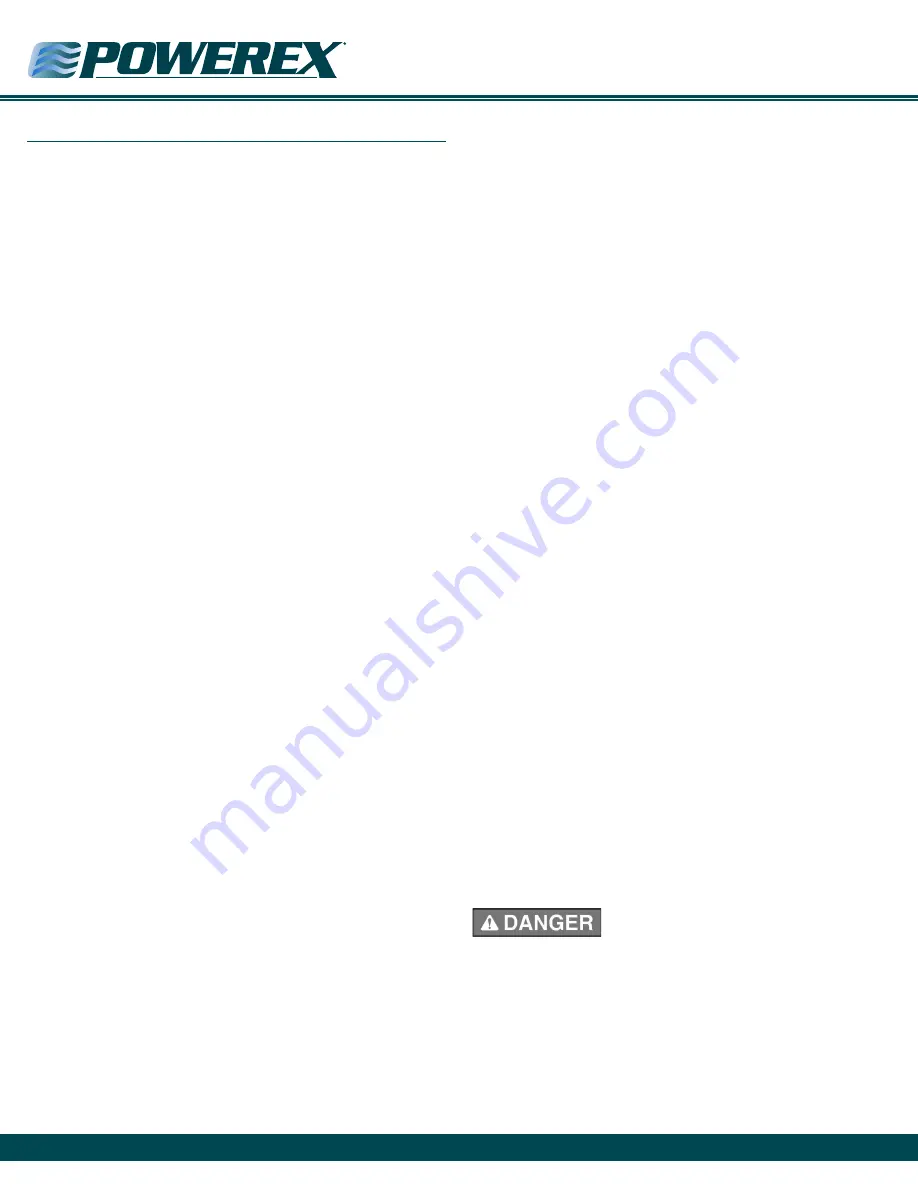
Medical Air & Laboratory Air Systems – 7.5 & 10 HP Pumps
Powerex
•
150 Production Drive
•
Harrison, OH 45030
•
USA
P 1.888.769.7979
•
F 513.367.3125
•
www.powerexinc.com
IN594402AV
•
06/2017
Page 2 of 28
Components
Oil-less Scroll Compressor Pumps
Powerex laboratory open scroll systems are designed to supply
continuous oil-free air by using the most advanced scroll technology.
The Powerex scroll compressor offers a dynamically balanced air
end which insures vibration-free operation. The rotary design permits
a continuous 100% duty cycle. No oil separation, oil filtration, or inlet
valves are required on the Powerex Scroll unit. Each compressor
shall be belt driven oil-less rotary scroll single stage, air-cooled
construction with absolutely no oil needed for operation. Direct drive
compressors shall not be used. The rotary design shall not require any
inlet or exhaust valves and shall be rated for 100% continuous duty.
Systems consist of multiple compressor pumps that are automatically
controlled and alternated to equalize usage and wear.
The Powerex oil-less rotary scroll air compressor is based on the
theory of scroll compression. A scroll is a free-standing, intricate
spiral bounded on one side by a solid, flat plane or base. A scroll set,
the basic compression element of a scroll compressor, is made up
of two identical spirals which form right and left hand parts. One of
these scroll components is indexed or phased 180° with respect to
the other so the scrolls can mesh.
Crescent-shaped gas pockets are formed and bounded by the spirals
and the base plate of both scrolls. As the moving scroll is orbited
around the fixed scroll, the pockets formed by the meshed scrolls
follow the spiral toward the center and diminish in size. The moving
scroll is prevented from rotating during this process so that the 180°
phase relationship of the scrolls is maintained. The compressor’s inlet
is at the outer boundary of the scrolls. The entering gas is trapped in
two completely opposite gas pockets and compressed as the pockets
move toward the center. The compressed gas is discharged through
the outlet at the center of the fixed scroll so no valves are needed.
Each compressor shall have flexible connectors on intake and
discharge, an electric drive motor, a discharge check valve, an air-
cooled aftercooler and a high discharge temperature shut down
switch. Each compressor module shall have an isolation valve and a
moisture separator with automatic drain.
The scroll pump is driven by a three phase electric motor and a dual
V-belt drive.
The system includes an after cooler for each pump and condensate
separators connected to electric timer drain valves. For NFPA99
systems, duplex, isolatable timer drains are installed. Each pump
module or stack of two pumps for 10 HP models is equipped with
an isolation valve so that the pump or module may be removed for
service and the valve closed leaving the system operable with partial
capacity. (If the valve is used to isolate the system while a person is
working or risk of injury exists, appropriate energy lock out tag out
procedures must be employed.)
Controls
The disconnects and protection devices in the Powerex control
system are for the motor branch circuits, accessory supply circuits and
for the control circuit only. The controls on the Powerex Laboratory
Open Scroll System do not include a service disconnect and circuit
protection for the supply circuit. Selection and installation of these
items must be provided in compliance to local and national codes in
accordance with each facility’s need.
The PLC automatically alternates the lead designation and brings
on lag pumps as needed, equalizing run time on the pumps in the
system. The touch screen HMI (Human Machine Interface) panel on
the front allows operation and monitoring of the system. The touch
screen provides the user with displays showing the operating status
and allows the user to access features of the control system. The
control panel also allows communication using the BACnet® protocol.
The control panel includes Hand-Off-Auto selector switches for
each pump so that a pump can be held on (or off). This can be useful
if maintenance or diagnostic procedures are being performed.
The transformer is sized for the loads imposed by the Powerex
factory controls and should not be utilized for any other purpose.
Premium control panels utilize a backup transformer with a reserve
transformer in use alarm.
Local alarms are provided for low pressure and general fault
conditions. The general fault alarm includes high temperature,
reserve transformer in use, motor overload and reserve pump in use
(when specified). The wiring connection point for the alarms is on the
terminal strip in the control panel box, with good conditions being
contacts closed. (If a wire connection is lost, the result is an alarm.)
Receiver Tank
The ASME, National Board registered air receiver is provided in sizes
from 200 to 240 gallons. Each receiver is rated at 200 psig working
pressure. Receivers are provided with sight gauge, moisture drain
(manual and no-loss electric), and internal lining to prevent corrosion.
The system receiver tank with bypass valves and duplex twin tower
desiccant dryers are sized to provide adequate air storage and provide
a pressure dew point of –40°F for laboratory systems with one dryer
operating. Medical systems are not intended to operate with both
dryers simultaneously. Doing so will result in back flow into one of
the regulators and leakage of air from that device. Laboratory systems
have valves to allow both dryers to operate if needed.
The receiver tank is equipped with an electric timer drain that is
powered from the main control panel. The drain has a manual test
feature. The automatic action of the drain will be confirmed by the
lack of water accumulation.
Never drill holes in, or perform any welding on
receiver tanks (unless qualified by ASME to do
so) or use them beyond the rated pressure settings. Never mount other
machinery or equipment on receivers.
Air Dryer (Desiccant)
The regenerative desiccant consists of two (dual) towers filled with
desiccant. Each tower is switched on and off stream, alternating the
air system stream and then being regenerated. Dry purge air pulls
moisture from the desiccant and carries the moisture out of the
system. The medical system duplex twin tower desiccant dryers have