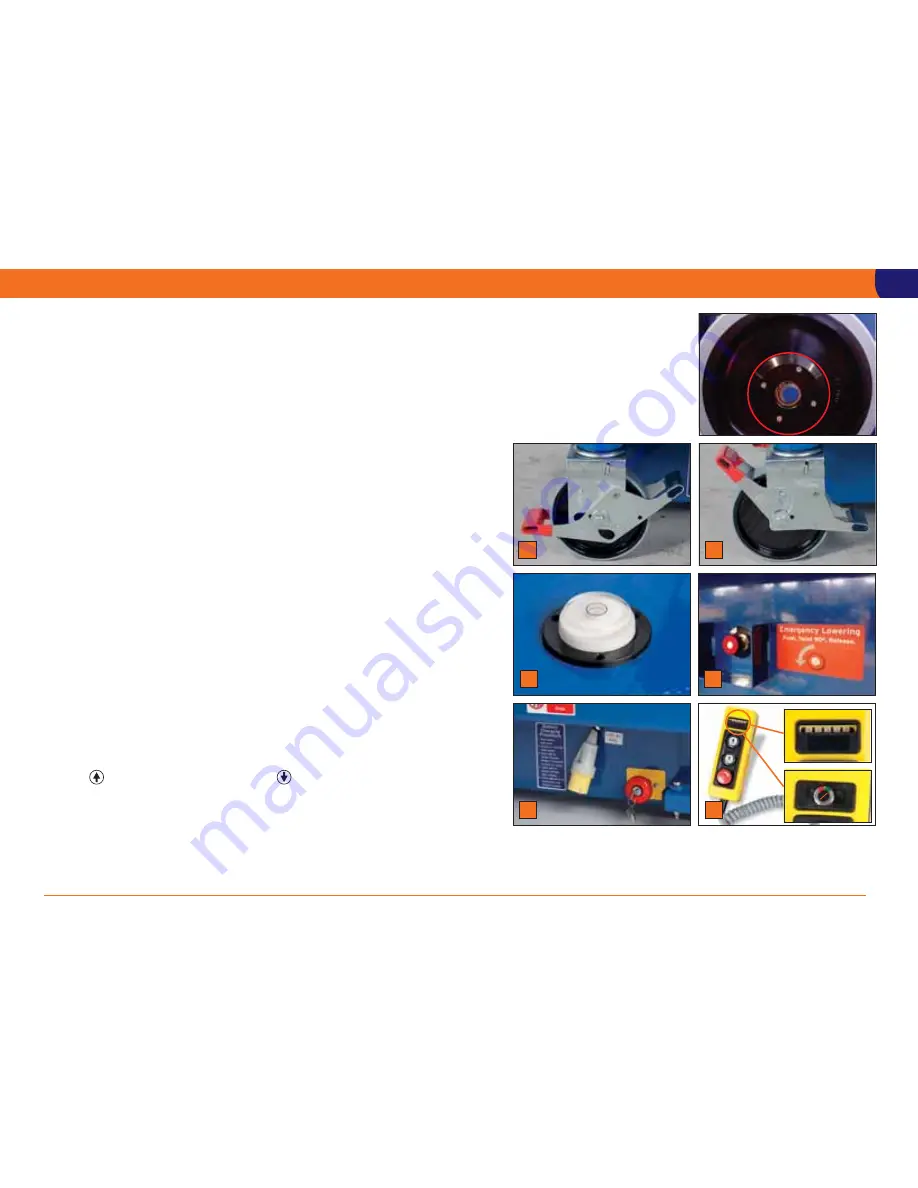
PRE-OPERATION CHECKS
1. Ensure there are no obvious signs of mechanical damage to the handrails,
platform, lifting structure or chassis.
2. Check platform access gate closes when released and that the latch
engages correctly.
3. Check castors and wheels rotate freely and are undamaged.
4. Check castor wheel and castor fixings. Check circlip (red ring) is correctly located
on end of stub axle and retained with hub cap (
Pic A
.)
5. Check emergency lowering is functioning correctly (refer to procedure on p.8).
6. Ensure the battery (where applicable) is fully charged, referring to the LED or dial
battery condition indicator on the pendant controller (
Pic 5
).
7. Ensure the hydraulic oil level is at the correct level. Do not overfill.
8. Check there are no hydraulic oil leaks and that all hydraulic connections
are tight.
9. Cordon off area around machine in accordance with guidelines.
NORMAL OPERATION
Only use the machine internally, on hard level surfaces. Ensure a person is available
at ground level to assist in case of emergency.
Position machine under application. Refer to working envelope
diagram if necessary.
1.
Apply both castor brakes (
Pic 1
).
2. Check spirit level to ensure machine is level (
Pic 2
).
3. Ensure the emergency lowering valve is closed (push and twist 90º,
release - do not force) (
Pic 3
).
4. Turn key switch in emergency stop button (located at the base of the
machine), then pull to release (
Pic 4
).
5. Battery condition indicator on pendant controller will indicate battery charge (
Pic 5
).
6. Check there are no overhead obstructions.
7. Enter platform via step and gate and ensure the gate is closed
and latched correctly when in platform. Do not elevate if the access gate is
not closed and latched.
8. Press arrowed button to elevate. Press arrowed button to descend.
9. In case of uncontrolled platform elevation or descent, depress
red emergency stop button (
on pendant controller or at base of
machine - refer to Pics 4 & 5
).
The user shall obtain the guidance and approval of the manufacturer in
the event of any special working methods or conditions which are outside
those specified by the manufacturer.
OPERATING PROCEDURES
7
Locked
1
Unlocked
1
2
4
3
55
Pic. A
Never affix the pendant controller to the guardrails or
toolbox area of the platform