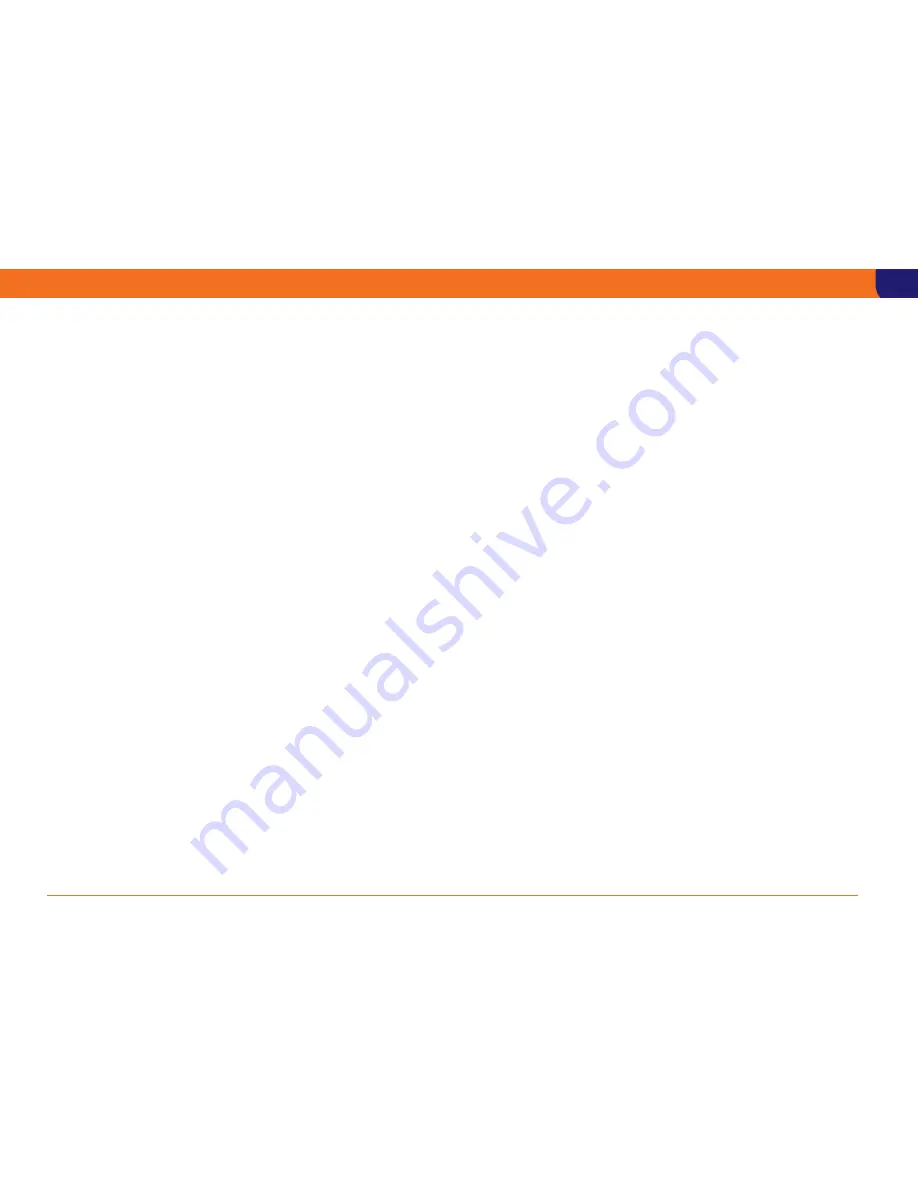
MAINTENANCE PROCEDURES
13
HYDRAULIC OIL
The hydraulic oil must be replaced on an annual basis. If the oil is not
replaced, then premature wear and failure of components will occur.
To drain the hydraulic tank, the mast must be in the transport position,
and the platform tilted to allow access to the motor/pump unit. The
only practical method to remove the oil from the tank is to use a syringe
suitable for hydraulic oil, which are easily obtainable, or a vacuum system
for hydraulic oil. The hydraulic steel pipe connection to the cylinder must
not be disconnected, unless by a competent person. If the connection
has been disconnected, then a full pressure test of the system must be
conducted prior to placing the machine back into service. No leaks must
be evident when the pressure test is conducted.
Refill with grade 32 mineral oil.
WHEELS AND CASTORS
It is absolutely essential that the wheels and castors are maintained in
good condition at all times, for two reasons:
The first is that they act as the stabilisers, and whilst their load capacity
is over rated for the application, any failure could result in a serious
accident. Secondly, if the bearings become tight, then it will make the
machine difficult to manoeuvre.
A measure of horizontal push force can simply be made to determine the
condition of the wheel bearings. On a flat smooth surface the machine
should move with a force of 9 – 10 kg at the mid guard rail height. The
maximum allowance is 20 kg.
Obviously this force is dependant upon the surface and gradient, but the
above is the recognised method of measurement, in accordance with HSE
guidelines.
Check rear wheels to ensure retention circlip is securely fitted to end of
stub axle and plastic cap is fitted over it.
MOTOR CONTACTOR SOLENOIDS
When conducting the six monthly LOLER inspection, check the correct
functioning of the two motor contactors.
Fit new contactors after every three years.
SUZI CABLE CONNECTOR PLUG MAINTENANCE
In order to ensure the reliable and correct operation of the machine it is
highly recommended that on a six monthly basis the connector plug be
separated and the condition of the connector plugs pins be noted and an
anti-corrosive spray be applied before reassembly.
Locate the plug on the end of the wire from the suzi cable and holding
both the wires and the rubber body of the connector plug, pull the two
halves apart. The plugs cans sometimes be difficult to separate and it may
be found that rolling back the outer boot prior to pulling the plug apart
can help.
Once separated look at the condition of the pins. If found to be corrosion
free then spray the pins and sockets with Ambersil S4. Hold each half of
the connector plug vertically and spray a liberal amount of the anti-
corrosive grease into the plug and pins and allow to drain into the back
of the plug body. The spray can also be applied to the rubber boot. Re-
assemble the plug.
If the pins are found to have corrosion they must be replaced. In this case
please refer to Power Towers technical department for assistance.
When replacing components for any reason, only use OEM specification
parts, either supplied from the manufacturer or authorised in writing
by the manufacturer. Warranties and design approvals will be void if
alternative components are fitted.
It is essential to obtain manufacturer’s approval of any alteration
which might affect stability, strength or performance in writing before
proceeding.