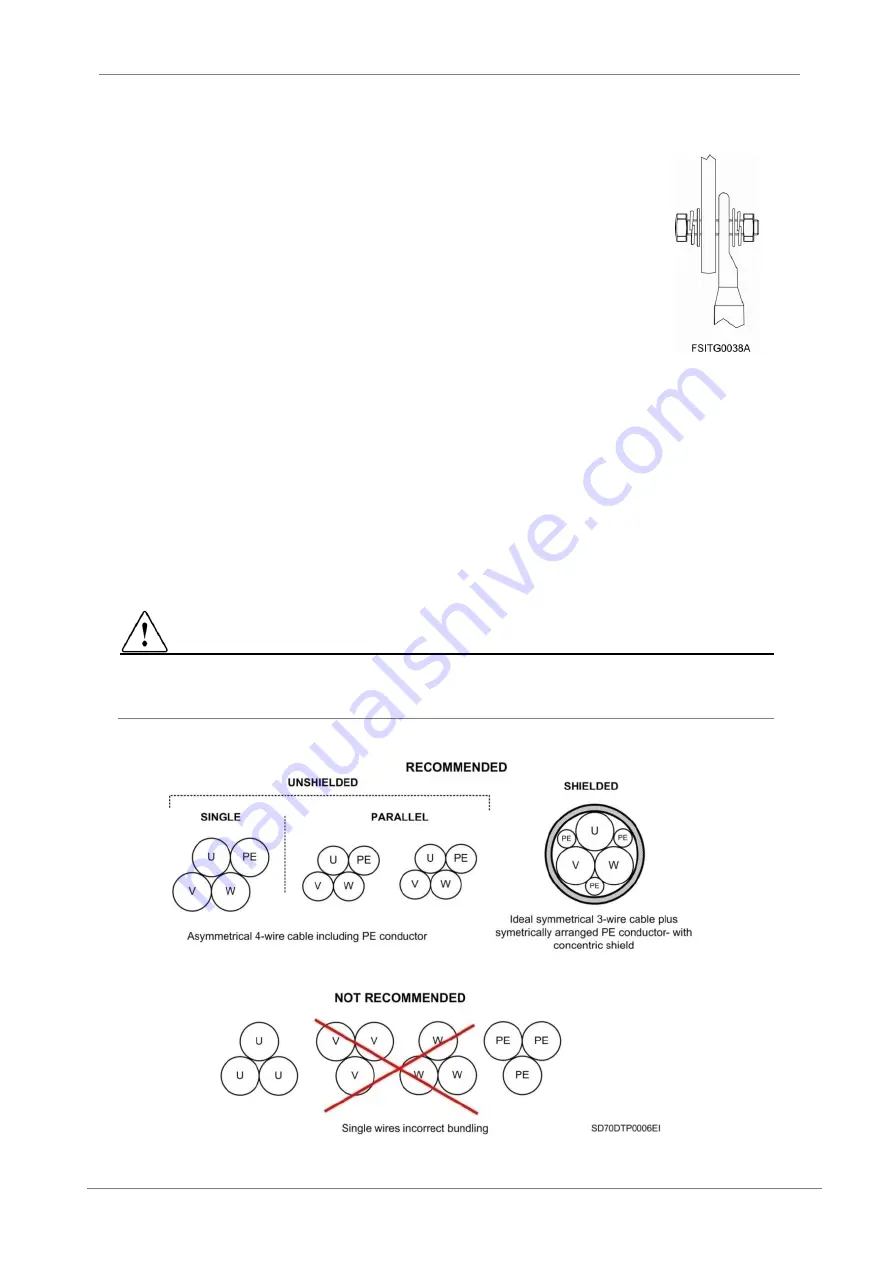
SD700FL SERIES
POWER ELECTRONICS
32
POWER CONNECTION
As standard, the input and output terminals are made of tin plated copper. If they are oxidized prior to its
installation, the connections will be poorly executed and will cause overheating. To avoid this effect is
recommended to follow the next steps.
It is recommended to use Ø11 tin plated copper terminal lugs.
Use M10 zinc bolts and nuts and apply a torque of 40Nm. Check after the
first week of operation that the torque applied is maintained.
The number of available terminals depends on the frame size. Check the
power terminal section.
Before connecting the cables, clean the contact surfaces with a clean
cloth and ethanol cleaner.
Use a spring washer and a fender washer between the nuts or bolts head
and the busbar or terminal lug.
Use copper or aluminium 600Vac conductors for up to 500Vac rated
voltage. For 525Vac and 690Vac phase to phase rated equipment use
1kV conductors.
Figure 6.8 Terminal lug connections
The recommended cable types and lengths between the drive (at factory settings) and the motor are:
Unshielded cable
: 300m. Asymmetrical 4-wire including PE conductor. It is recommended to
use a motor ground cable (PE) cross section equal or higher than active motor wires cross
section (U, V, W). When single-wire cables are used in three-phase systems, the three phase
conductors must be bundled symmetrically.
Shielded cable
: 150m. Ideal symmetrical 3-wire cable plus symmetrically arranged PE
conductor- with concentric shield. To implement an effective shield bonding it could be used an
EMC gland in both motor terminal box and drive cabinet to ensure effective 360º ground
connection and a low high frequency impedance path. Check the EMC recommendations
section.
CAUTION
The number of three phase cable hose (U, V, W, PE) to the motor should be equal to the number of
IGBT’s in the drive, being one cable hose by each IGBT’s Block.
The following figures show the recommended cable type and bundling.
Figure 6.9 Recommended cable type and bundling