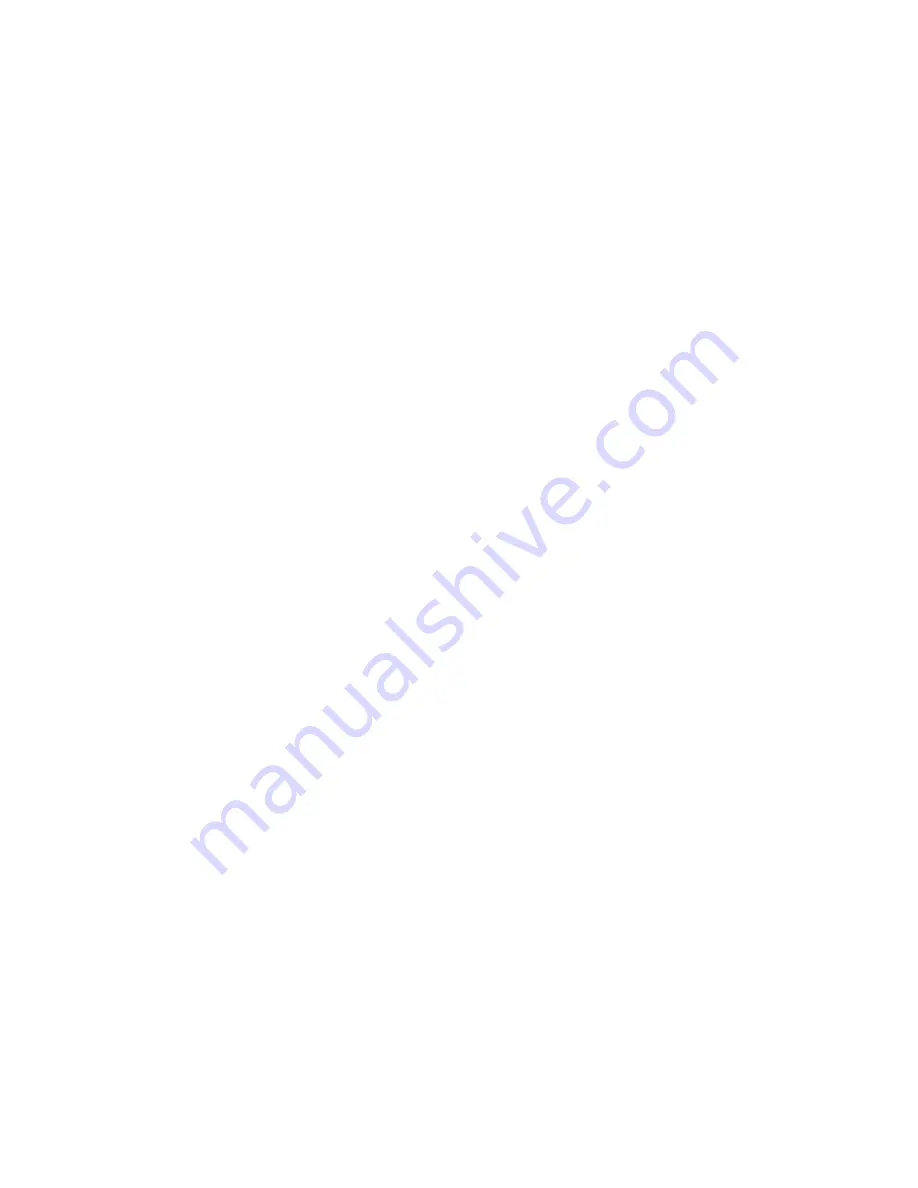
5. Programming in AUTO mode
The power supply can be programmed 12 separate heating profiles or jobs. Each profile can
contain 25 steps. The duration of each step can be up to 640 seconds.
5.1. Entering a program
1. Turn on the power supply and put the MODE selector switch in MANUAL.
2. Enter the program mode by depressing the JOB button for 2 seconds, until the Volt,
Curr, and Freq displays go blank. The STEP will read 1 and JOB will display the last
job used, or 1 if no other job was used.
3. If a heating profile has previously been entered in a Job, then the power and step time
will be displayed on the PWR and STEP TIME readouts.
4. To clear an existing program select the job to be cleared, press the CLR button then
press the ENT button twice. (once for JOB 2nd for Auto Repeat Ar)
5. A power level and a time can be entered for up to 25 steps. The power level will ramp
from the last power level to the power level requested. To get a power level quickly, set
the time to 0.1 seconds and then set power to the desired level. Then set the next step
to that power level and the time to the desired interval.
6. For each step, press PWR UP (
S
) and the PWR DOWN (
T
) keys to set the power level
and press TIME/FREQ UP (
S
) and the TIME/FREQ DOWN (
T
) keys to enter a time up
to 640 seconds. For longer intervals, several steps in a row can be set to the same
power level.
7. Press STEP to move to step 2. Enter power level and time as in step six.
8. Press ENT (enter) once, this will bring you to the “Ar” display (explained later), press
ENT again to record changes, or press JOB to move onto the next job. Note: If no Job
has been programmed an “AUX” trip indicator will be lit.
9. Pressing the CLR button will exit program mode without saving changes.
Note
: Waiting too long to enter values, unit will time out and exit programming.
5.2. Auto Repeat Function
1. Each JOB (except JOB 0) has an auto repeat function, which enables a selected job to
be repeated up to 999 times.
2. To activate auto repeat press and hold JOB for more than one second, after selecting
the job you want to repeat press ENT once, this will open the auto repeat function.
3. In the STEP window Ar will appear, in STEP TIME and in TOTAL TIME window 0’s will
appear. The step time will indicate the “pause” time (indicated by a P in the STEP
window) between repeat cycles and the TOTAL TIME will indicate the repeat number of
cycles.
4. Press the TIME (
S
) (
T
) to increase or decrease the pause time.
5. Press the PWR (
S
) (
T
) to increase or decrease the number of repeat cycles.
6. Press ENT when completed.
Note
: When using any one JOB, a time of more than .3 seconds must be entered at any
STEP and a power level of more than 1% entered to avoid an “
AUX
” trip.
13