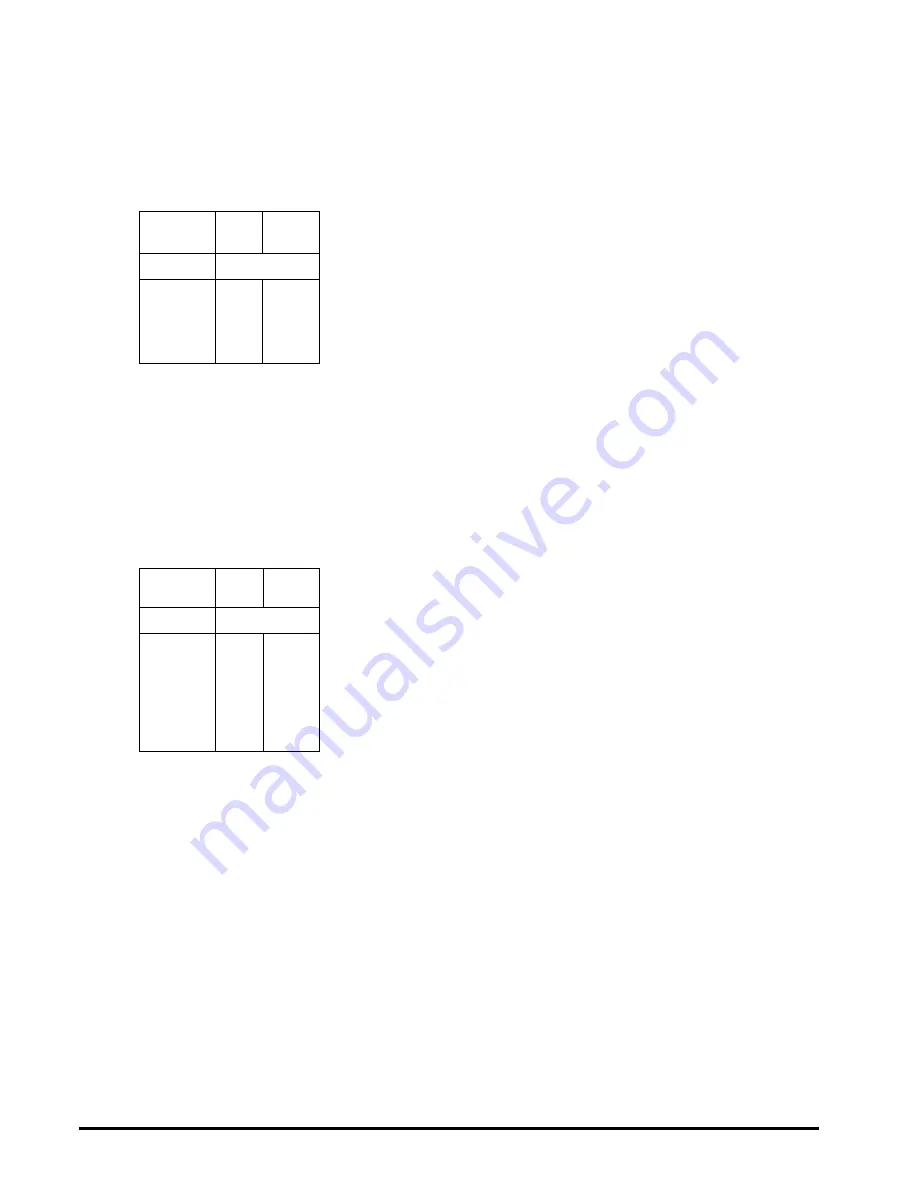
22
Part No. 5106463
Pre-Installation Requirements
Pipe Dia
I/D in mm.
8
10
'A' Metres Length in Metres
0.5
10
20
1.0
20
40
1.5
40
80
2.0
60
100
Table 4
Figures for
Kerosine Only
Pipe Dia
I/D in mm.
8
10
'B' Metres Length in Metres
0.0
100
100
0.5
100
100
1.0
100
100
1.5
100
100
2.0
100
100
2.5
80
100
3.0
55
100
3.5
5
90
Table 5
Figures for
Kerosine Only
appliances with pressure jet burners by means of
a single pipe need to be positioned so that they will
apply the 300 mm minimum required head of oil to
the burner when the fuel level is at its lowest point.
The fittings and layout are shown in Fig. 16.
b) Two Pipe Supply Systems - If the tank base is
below the level at which gravity feed to the burner
can be maintained, a two pipe oil supply system
can be adopted. The fittings and layout are shown
in Fig. 17. The non return valve in the supply line of
the two pipe system is required to prevent oil
running back from the burner and un-priming the
oil pump. The non return valve in the return line is
only required if the top of the tank is above the
burner. Its purpose is to prevent oil running back
through the burner during maintenance.
Oil Line De-Aerating Devices
These may be used in conjunction with Statesman
boilers. It is recommended that they are fitted outside
the dwelling. It is not permissible to fit plastic
components in fuel lines within dwellings or boiler
rooms. The manufacturers instructions should always
be followed, particularly when the oil tank may be
situated at low level. The fittings and layout are shown
in Fig. 16.
Oil Filter
An oil filter should always be fitted in the oil supply
line. Facilities should be provided to enable it to be
serviced without draining down the oil supply system.
Fire Valves
A fire valve is an essential part of the oil supply system.
It should be capable of cutting off the flow of oil outside
the building in the event of a fire starting up within the
boiler.
The valve should be located just outside the building
at the point where the oil supply line enters. It must be
activated by a remote sensor located over the burner
but in a position clear of any direct radiation or
excessive heat. Weight operated valves connected to
a sensor by wires and pulleys have been used for this
purpose. It is preferable, however, to use a valve with
a capillary connection between its sensor and the oil
cut off mechanism. The use of fusible head isolating
valves is not recommended.
It is essential that these devices conform to current
Standards and Regulations. When they are
installed, their manufacturers recommendations
must be adhered to.
Copper Tube and Fittings
Copper tube for oil lines should be to BS.2871:Part 1:
Table Y. It can be obtained in coil form or half hard for
use with bending machines. This pipe can be obtained
with protective plastic sheathing applied. Copper tubes
for oil lines must not be soldered.
Note: Galvanised pipes must not be used.
Fittings for copper pipe should be of the flared
manipulative type to BS.864:Part 2:1983. Steel pipe
should be to BS.1387:1985. Fittings for steel pipe
should be to BS.1740:Part 1:197271 with taper threads.
Floor Temperatures
The thermal insulation provided in the boiler base
ensures the floor temperatures is kept below 80 °C
and as such, a non combustible hearth is not required.
The floor should always be smooth and flat and capable
of supporting the installed weight of the boiler, including
its water content. If constructed by a material which is
softened by oil, it is advisable to install an additional
metal tray underneath the boiler for protection against
accidental damage.
The Heating System
When fitting into an existing installation, the system
should be chemically cleaned (if practical) before
installing the boiler. A suitable inhibitor should be added
to keep it in good condition.
System Requirements: These boilers are specifically
designed for Sealed Systems but will operate on open
vented systems. When used on a sealed system the
central heating system should be in accordance with
the relevant recommendations given in BS 5449 Pt 1
and BS 7074 Pt 1.