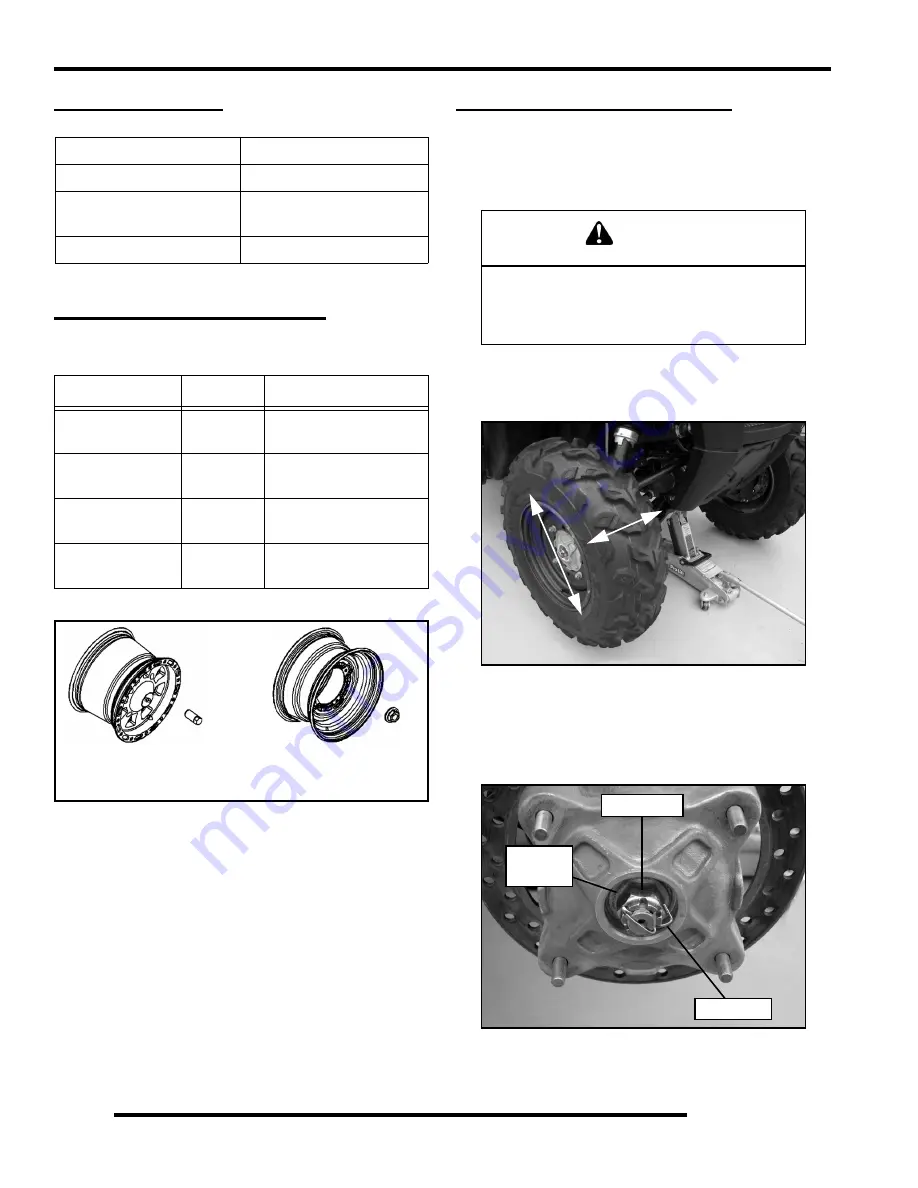
7.2
FINAL DRIVE
SPECIAL TOOLS
TORQUE SPECIFICATIONS
Wheel and Hub Torque Table
FRONT BEARING CARRIER
Bearing Carrier Inspection / Removal
1.
Elevate front of vehicle and safely support machine under
the frame area.
2.
Check bearings for side play by grasping the top and bottom
of the tire firmly and checking for movement. The tire
should rotate smoothly without binding or rough spots.
3.
Remove the (4) wheel nuts and remove the front wheel.
4.
Remove the cotter pin and loosen the front wheel hub castle
nut. Remove the nut, and (2) cone washers from the front
wheel hub assembly.
5.
Remove the fastener retaining the steering tie rod end to the
front bearing carrier.
PART NUMBER
TOOL DESCRIPTION
2872608
Roll Pin Removal Tool
8700226
CV Boot Clamp Pliers
(earless type)
PU-48951
Axle Boot Clamp Tool
ITEM
NUT TYPE
SPECIFICATION
Aluminum Wheels
(Cast)
Lug Nut
(1)
30 ft. lbs. + 90
°
(1/4 turn)
Steel Wheels
Flange Nut
(2)
35 ft. lbs. (47 Nm)
Front Hub
Castle Nut
-
80 ft. lbs. (108 Nm)
Rear Hub
Castle Nut
-
80 ft. lbs. (108 Nm)
Steel Wheel
(Standard Models)
35 ft. lbs. (47 Nm)
#1
#2
Aluminum Wheel
(LE Models)
30 ft. lbs. + 90° (1/4 turn)
CAUTION
Serious injury may result if machine tips or falls.
Be sure machine is secure before beginning this
service procedure. Wear eye protection when
removing bearings and seals.
Castle Nut
Cotter Pin
Cone
Washers
Summary of Contents for Ranger RZR SW
Page 4: ......
Page 12: ...1 8 GENERAL INFORMATION SAE Tap Drill Sizes Metric Tap Drill Sizes Decimal Equivalents ...
Page 14: ...NOTES GENERAL INFORMATION 1 10 ...
Page 48: ...NOTES MAINTENANCE 2 34 ...
Page 50: ...3 2 ENGINE ENGINE SPECIFICATIONS Crankcase Exploded Views ...
Page 51: ...3 3 ENGINE 3 Oil Pump Water Pump Engine Cover Exploded View ...
Page 52: ...3 4 ENGINE Stator Cover Starter Water Pump Oil Filter Pressure Relief Exploded View ...
Page 53: ...3 5 ENGINE 3 Cylinder Cylinder Head Piston Exploded View ...
Page 112: ...NOTES ENGINE 3 64 ...
Page 154: ...4 42 ELECTRONIC FUEL INJECTION Digital Wrench Feature Map ...
Page 192: ...NOTES BODY STEERING SUSPENSION 5 34 ...
Page 264: ...NOTES FINAL DRIVE 7 48 ...
Page 284: ...NOTES TRANSMISSION 8 20 ...
Page 324: ...10 18 ELECTRICAL COOLING SYSTEM SCHEMATIC Cooling System Break Out Diagram ...
Page 345: ......
Page 346: ......