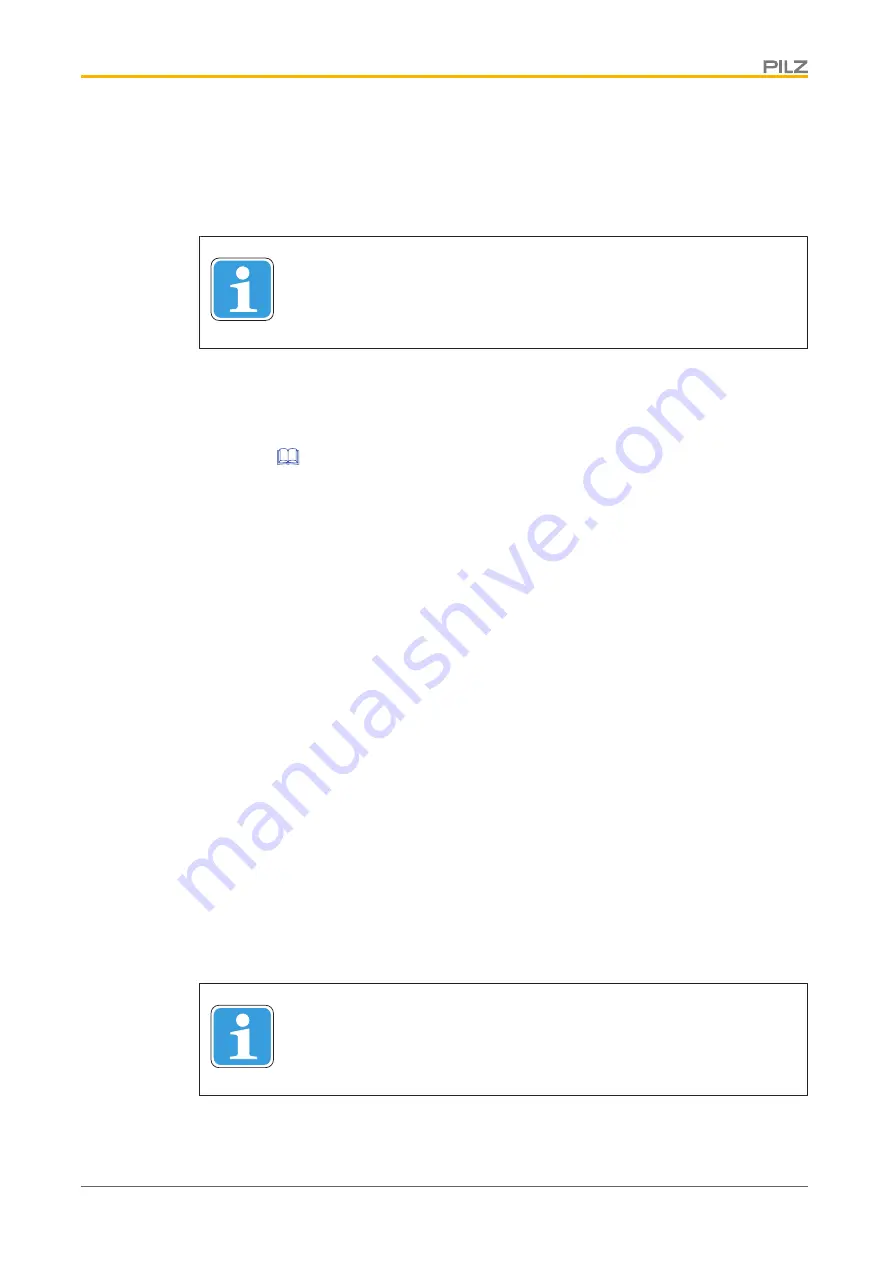
PSEN ma1.4-51 M12/8-0.15m
Operating Manual PSEN ma1.4-51 M12/8-0.15m
22185-EN-05
14
}
The safety switch and actuator should only be secured using screws and nuts made of
non-magnetic material (e.g. brass or stainless steel).
}
Avoid the risk of damages from foreseeable external influences by attaching the safety
switch and actuator. If necessary, safety switch and actuator have to be protected.
INFORMATION
The actuator should be protected from unauthorised removal and from con-
tamination.
}
Prevent self-loosening of the fastening elements of safety switch and actuator.
}
The fastening of safety switch and actuator has to be sufficiently stable to ensure the
proper operation of the safety switch and the actuator.
}
The distance between two safety switches must be maintained (see
Technical
details [
17]
).
}
Safety switches and actuators
– Should be kept away from iron swarf
– Should not be exposed to strong magnetic fields
– Should be used for fixed wiring only
}
Prevent the safety switch and actuator being exposed to heavy shock or vibration
}
Make sure that the safety switch and actuator cannot be used as an end stop.
}
Circumvention of the safety switch in a reasonably foreseeable manner must be pre-
vented.
}
Please note the installation measures in accordance with EN ISO 14119 for a proximity
switch design 4 and with level of coding Low
}
Alignment errors of the guard must not adversely affect the safety function of the guard.
}
The assured operating distance S
ao
and the assured release distance S
ar
must be tested
under real conditions.
Installation type 1
}
1. Cut the thread (M4) in the required position.
}
2. Use a screw to fix the sensor.
}
3. Attach the second screw to the sensor. (Important: do not tighten the screws). Attach
the screws for the actuator, maintaining the distance between the screw head and the
plate: ca. 3 ... 6 mm.
}
4. Align actuator to sensor.
INFORMATION
The inscribed area on the actuator (sensing face) should face the sensor.
}
5. Slide the actuator on to the screws.
}
6. Align sensor and tighten screws with max. 0,8 Nm.