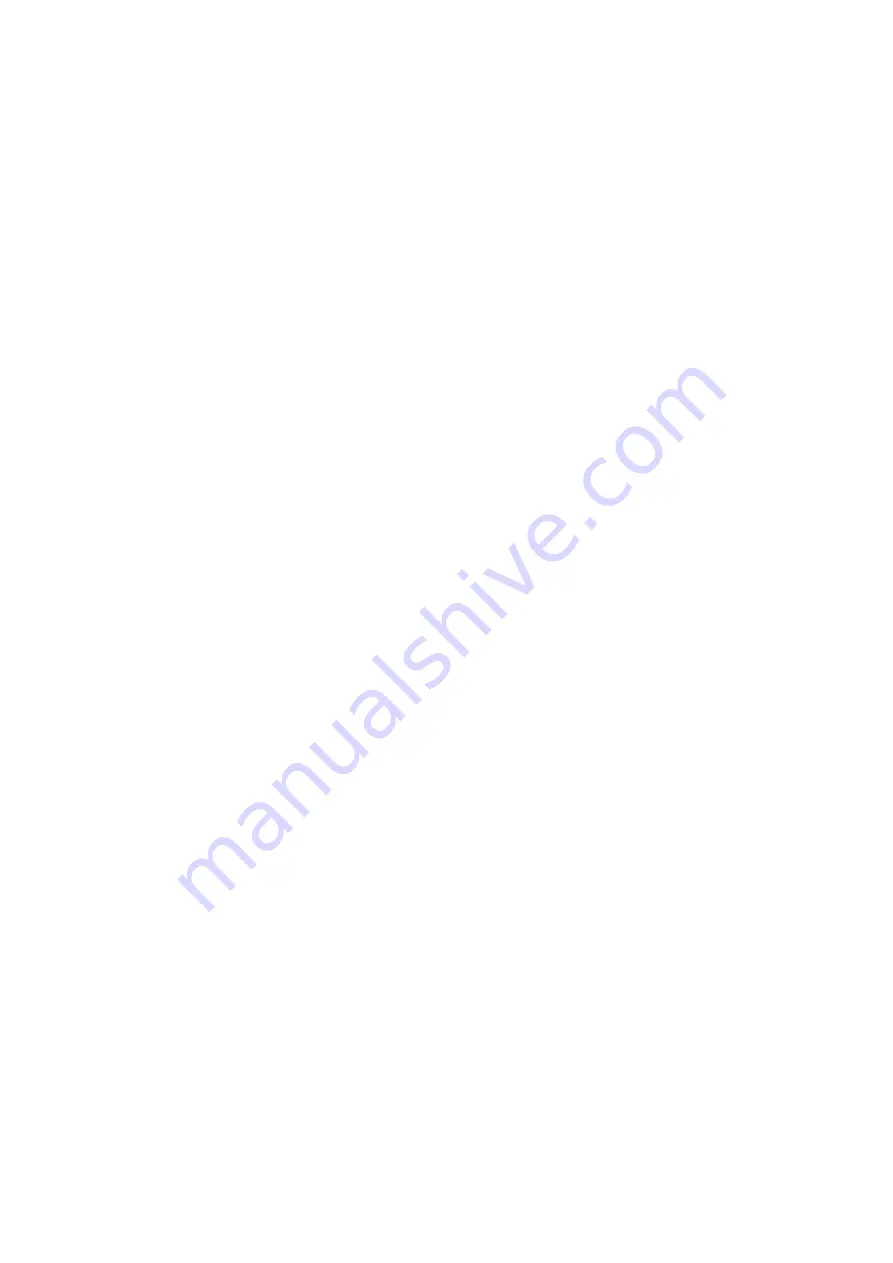
The following principles must be adhered to during assembly of hydraulic circuit sub-assemblies, elements and piping. The basic rule
is cleanliness and good order! The hydraulic circuit consists of very precise elements and it is very difficult, tough and costly to
remove any contamination and its consequences. Inappropriate storage or failure to renew the rust protection of hydraulic elements
causes locking of internal moving parts of the elements. The element must be washed with a suitable degreasing agent (petrol, etc.)
and the oil film must be renewed. Read through the manufacturer's documentation containing the instructions concerning the
method of assembly, the torque of bolts, etc. All the hydraulic circuit components must be mounted without force. When lifting the
hydraulic units and sets, make sure they are protected against mechanical damage by the binding equipment. Hydraulic element
guards (transport plates on bearing surfaces, plugs in threaded chambers) should be removed immediately before assembly.
Electrical Installation
Electrical installation, electromagnet and control element leads (electromagnets) must comply with the valid regulations and
standards, especially CSN 33 2200 and CSN 34 5611. Check the plate or catalogue operational voltage and frequency values with
regard to the network values before making the connection to the electric network. Protection against dangerous touch voltage must
comply with CSN 34 1010, according to which the entire equipment must, among others, be properly earthed. The earth connection
(interconnection of the equipment with the earthing system or the neutral conductor) is carried out by the earthing screw provided on
one leg of the unit tank. The nut welded to the tank is provided with the earthing marking. The regulations stipulated by the CSN 34
3100 must be followed during attendance and repair of the electrical installation.
Filling Tank with Oil
First, check the inside space of the tank thoroughly. Check the condition of the oil-resistant coating. Should any flaking or poor quality
manifest themselves, remove the coating with an appropriate solvent, wash, dry and clean with pressure air. In this way, failures
caused by poor-quality coating, which contaminates the entire hydraulic system, will be prevented. On principal, only oil
recommended by the equipment manufacturer may be filled in. Never make the filling directly from barrels. Always use a filter unit
with filters 12 µm and better. The proven method is using two filters with different filtering property. The first coarse filter with a metal
sleeve, the other one fine with a paper sleeve. The work will be facilitated and achieve better quality if the filters are provided with
signaling of clogging.
What should be done before putting hydraulic unit into operation after repair.
Make sure that
• the tank has been filled with the prescribed pure oil up to the upper limit;
• all pipelines have been thoroughly cleaned, the connections properly tightened and the pipeline assembled without internal strain;
• all pipe unions and elements have been properly mounted and tightened by the specified torque and the assembled connection
corresponds to the hydraulic diagram;
• alignment and axial clearance have been adhered to when the couplings between motors and hydrogenerators and/or hydromotors
and other equipment have been mounted;
• the electric motor has been correctly connected ( ∆ or Y), the sense of rotation adhered to and the level, pressure and temperature
sensors function properly;
• the filters (sleeves) have the specified filtration values and are mounted in the correct flow direction and filled with oil identical to the
tank oil, and the inside space of the piston hydrogenerators is filled with oil.
Putting the Equipment into Operation
• start the hydrogenerator within short intervals,
• check the piping for noise and leakage,
• vent the hydraulic circuit,
• check the circuit functions with minimum load, if possible,
• gradually increase the pressure to the specified operating value; at the same time, adjust the control elements, such as control
valves, etc.,
• monitor the gauges and measuring devices, noise, oil level and temperature in the tank,
• follow the instructions of the individual operating manuals.
Putting out of Operation
• tighten all connections.
Restarting
• check oil level,
• test all functions simultaneously; compare the values measured to values specified,
• check the signaling of pressure gradient on filters.
Principles of Hydraulic Unit Assembly and Maintenance
ATTACHMENT TO OPERATING INSTRUCTIONS FOR HYDRAULIC UNIT
Summary of Contents for ARG 250 plus S.A.F.
Page 34: ...11 3 2 Table turning table pivot and vice assembly ARG 250 plus S A F ARG 300 plus S A F...
Page 44: ......
Page 45: ......
Page 47: ......