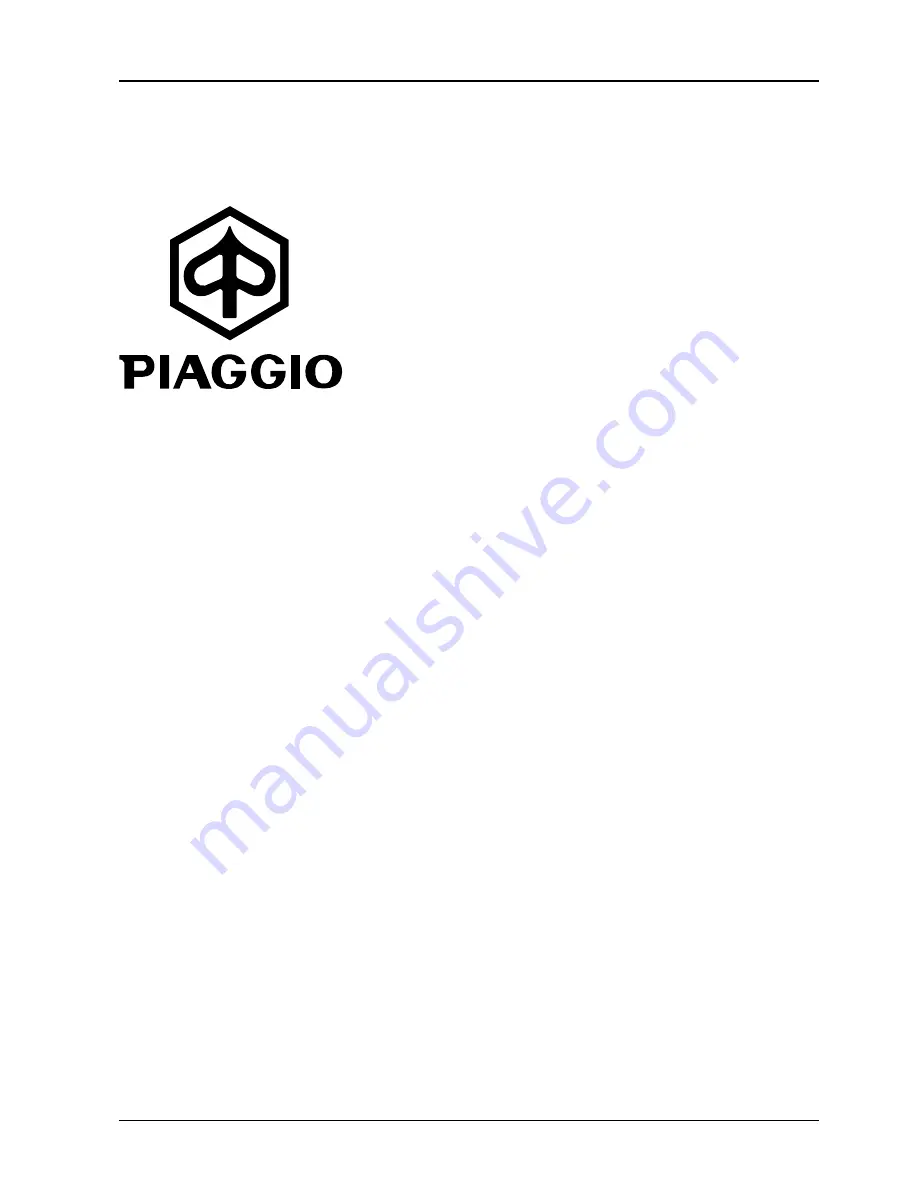
SERVICE
STATION
MANUAL
Piaggio & C. S.p.A.
Pontedera
After Sales Service
Dis. 594766 - 04/01
Grafica e Stampa:
C.L.D. - Pontedera (PI)
“© Copyright 2001 - PIAGGIO & C. S.p.A. Pontedera.
All rights reserved.”
Data are subject to modification without notice.
We decline all liability for the use of non-original spare parts or accessories that have not been tested and/or approved.
• Engine 500 cc
Summary of Contents for 500 cc
Page 4: ...TABLE OF CONTENTS GENERAL INFORMATION AND MAINTENANCE 1...
Page 12: ...TABLE OF CONTENTS SPECIFIC TOOLING 2...
Page 15: ...TABLE OF CONTENTS AUTOMATIC TRANSMISSION 3...
Page 32: ...TABLE OF CONTENTS FINAL REDUCTION 4...
Page 34: ...TABLE OF CONTENTS FLYWHEEL COVER 5...
Page 51: ...TABLE OF CONTENTS FLYWHEEL AND STARTING SYSTEM 6...
Page 63: ...TABLE OF CONTENTS THERMAL UNIT AND TIMING SYSTEM 7...
Page 94: ...TABLE OF CONTENTS CRANKCASE AND DRIVING SHAFT 8...
Page 113: ...TABLE OF CONTENTS FUEL INJECTION 9...
Page 220: ...TABLE OF CONTENTS LUBRICATION 10...
Page 228: ...TABLE OF CONTENTS COOLING SYSTEM 11...
Page 236: ...TABLE OF CONTENCTS STARTING 12...