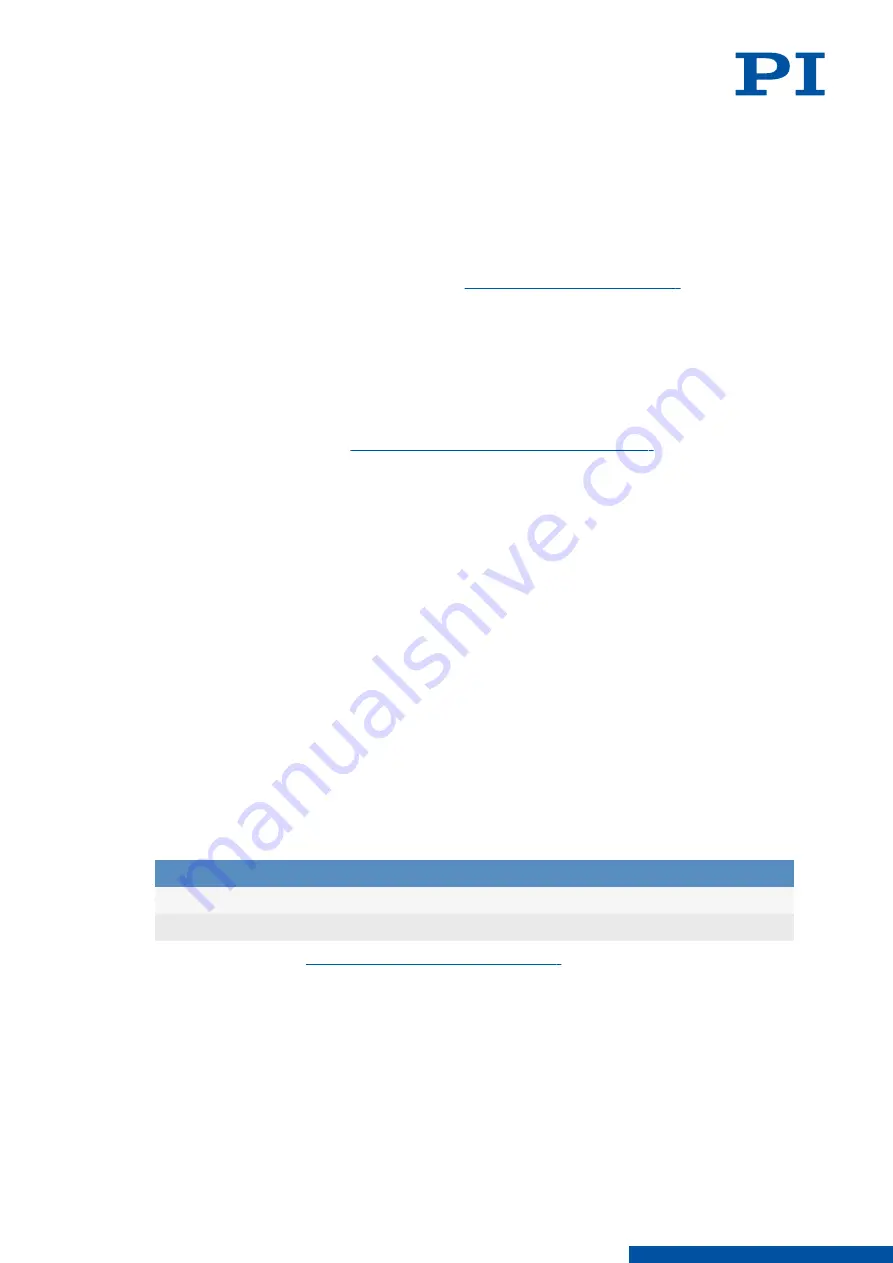
Drive
A 3-phase magnetic motor drives the V-408. The motor transfers the drive force to the
platform directly and free of friction.
Reference switch
The reference switch is a sensor whose fixed position serves as the reference point for
incremental sensor signals.
The V-408 is equipped with an incremental,
optical reference switch (p. 40)
See the controller user manual and/or associated software manuals for the commands that
make use of the reference point signal.
Limit switches
The limit switches are sensors at each end of the travel range that enable the electronics to
abort motion in order to prevent the motion platform from colliding with the mechanical
hard stop.
The V-408 is equipped with
noncontact Hall effect limit switches (p. 41)
Position sensor
The position sensor is an incremental sensor: It measures the position of the motion
platform relative to a known reference point. Optical linear encoders measure the actual
position directly (direct position measuring). Therefore, errors in the drive, such as
nonlinearity, backlash or elastic deformations cannot influence the measurement of the
position.
4.3.2
Drive Connector
The drive connector transmits the supply voltage for the drive.
4.3.3
Sensor Connector
The sensor connector transmits the sensor signals of the V-408.
4.4
Suitable Electronics
The V-408 must be connected to suitable electronics that supply the necessary voltage for
operating the V-408 and if required, to evaluate the sensor and limit switch signals. The
following electronics are suitable:
Product number Description
C-891.130300
PIMag® Motion Controller for Magnetic Direct Drives
ACS modular controller
To order, contact our
customer service department (p. 32)
.
4 PRODUCT DESCRIPTION
V408M0001EN
‒
2/17/2020
11
M O T I O N | P O S I T I O N I N G