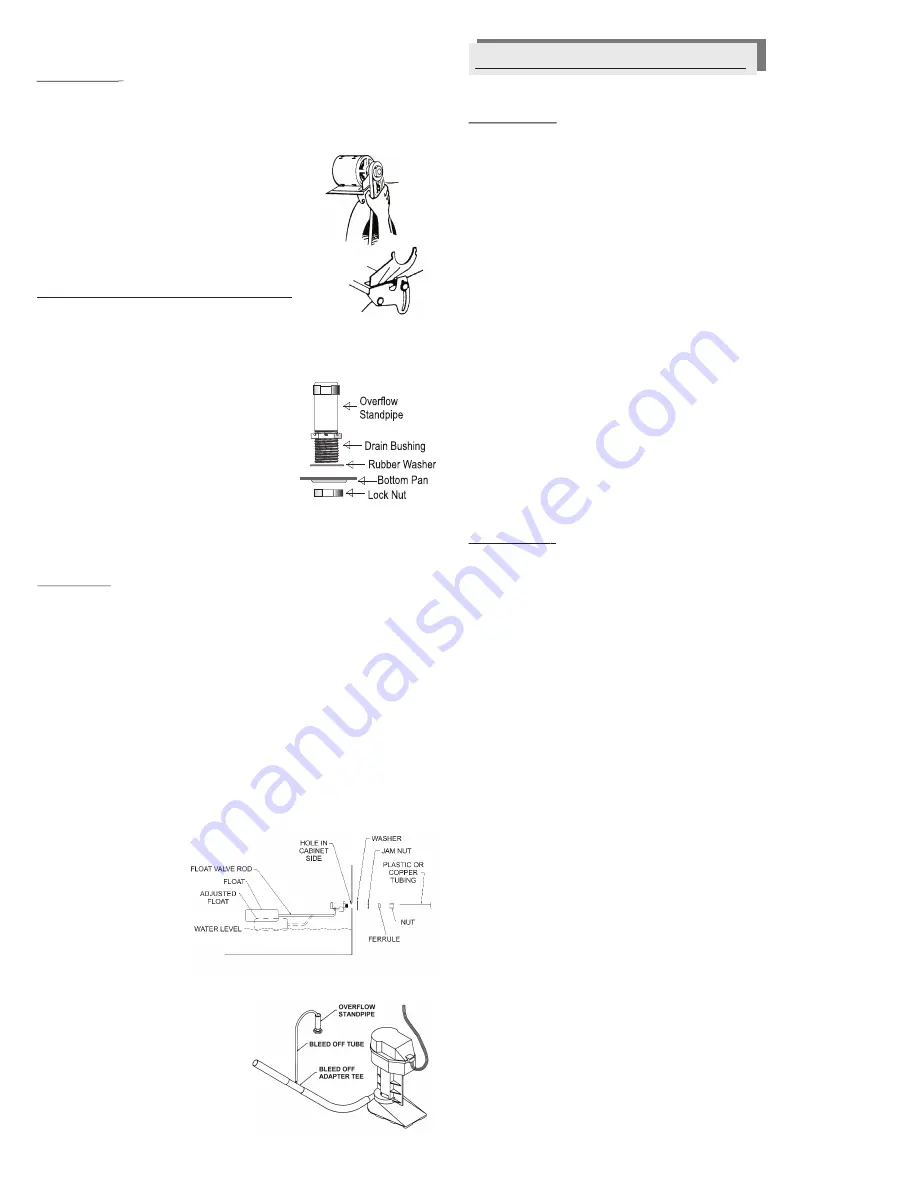
4 Trophy Ducted Evaporative Cooler Use and Care Manual
Belt Tension Adjustment
CAUTION
: Disconnect all electrical power to the cooler
and insure that belt is not rotating before adjusting belt
tension. Do not adjust belt tension by changing diameter
of motor pulley. Adjust belt tension only by adjusting
motor bracket.
Correct belt tension and alignment is
important, proper setup reduces power
consumption and prolongs life of belt and
motor. Check belt tension by squeezing belt.
Proper tension will allow deflection of ½ to ¾
inch. To increase or decrease belt tension,
loosen bolt in slot of motor support bracket.
Adjust belt to proper tension and retighten bolt.
Do not tighten belt by adjusting motor pulley.
Install Overflow Standpipe /
Drain Line
Install overflow drain bushing in bottom of cooler as follows:
Slide rubber washer over drain bushing.
Push drain bushing through bottom of
cooler, assemble and tighten lock nut.
Screw plastic overflow standpipe into
the drain bushing and tighten snugly
(hand tight) to prevent leakage.
Connect a suitable drain line (copper /
PVC / garden hose) to drain bushing.
Never drain water onto a roof; mineral
build-up or damage to roof may occur.
NOTE: Drain water in accordance with local plumbing codes.
Connect Water Supply
CAUTION: All plumbing installations must comply with
local building and safety codes, and must be performed by
qualified personnel only.
NOTE: Coolers should not be connected to “soft” water systems. Soft
water will accelerate corrosion and decrease the effective life of pads
and cooler cabinet. Connect water line as follows:
A water supply valve should be installed at a convenient location, to
allow the water supply to be turned on and off for servicing or
winterizing. Minimum 1/4“ diameter tubing should be used to
provide water to the cooler, larger tubing is recommended if the
distance from the valve to the cooler is greater than 100 feet, then
reduced to 1/4” at the unit.
Install float valve in the bracket provided.
Connect tubing from water supply to float valve. Place
compression nut and ferrule over end of tubing, insert tube into
float valve then tighten compression nut to secure.
Install Bleed-off
To minimize mineral scale “build-
up” use the included bleed-off
assembly. Remove the cap from
the bleed-off tee; insert the black
tubing and route the tubing
through standpipe opening into
the drain line
bove the
water level.
. To prevent
siphoning of the water, make sure
that the bleed-off tee is a
GENERAL INSPECTION
Initial Start-up or Annual Inspection
CAUTION:
Disconnect all electrical power to the cooler
before attempting to install, open, or service your cooler.
More than one disconnect may be required to de-energize
the equipment for servicing. If the cooler is
thermostatically controlled, the thermostat is not to be
used as the power supply disconnect, as it may reset and
start the unit unexpectedly.
Before start-up the cooler for the first time, or at the beginning of each
cooling season, make sure that all required connections,
adjustments, etc. have been made. Verify that:
P
Cooler mounting is level; ductwork is sealed.
P
Cabinet is securely fastened to mounting.
P
Cooler cabinet is properly grounded. Electrical connections are
correctly made, safe and secure.
P
Motor, pump, drain, bleed-off, float valve, etc. are correctly
installed and fully functional.
P
Water line securely connected, turned on, no leaks noted.
P
Float adjusted for proper water level.
P
Pump impeller turns free and smooth. If in doubt, remove
impeller cover (see “Cleaning Pump”) and check rotation.
P
Blower wheel, shaft, pulley and motor sheave bolts /
setscrews are tight.
P
Motor sheave / Blower pulley alignment okay; belt correctly
tensioned, blower wheel turns freely.
Start-up Check List
CAUTION
: Never operate cooler with access panels
removed. This will result in an overloaded condition and
may damage the blower motor.
To verify and check out the cooler installation on initial or annual start-
up, the following procedure should be followed.
P
Turn electrical supply to pump on.
P
Verify that pump starts and pads are evenly wet.
P
Open building exhaust / relief vents (windows, doors, etc.)
P
Turn electrical supply to blower motor on.
P
Observe that motor starts and runs, check each speed
(where applicable) and confirm air delivery.
P
Verify motor amperage does not exceed nameplate.
In case of trouble on any of these steps, refer to the Troubleshooting
Chart on
Cabinet Inspection Checklist
After initial start-up and for a few weeks afterwards, check for and/or
observe the following: Refer to the Troubleshooting Chart on
f
necessary.
P
Leaks from water lines, cabinet, etc.
P
Cooler pads: even wetting, no dry streaks.
P
Confirm water level depth setting is correct.
P
Verify full, even flow in water distribution system.
P
Blower wheel / motor rotates freely, no unusual noises.
P
Belt condition / tension / alignment OK.
P
Check motor mounting, cabinet hardware, setscrews on pulleys,
blower wheel are tight
page 6.
page 6 i
2 1/2"