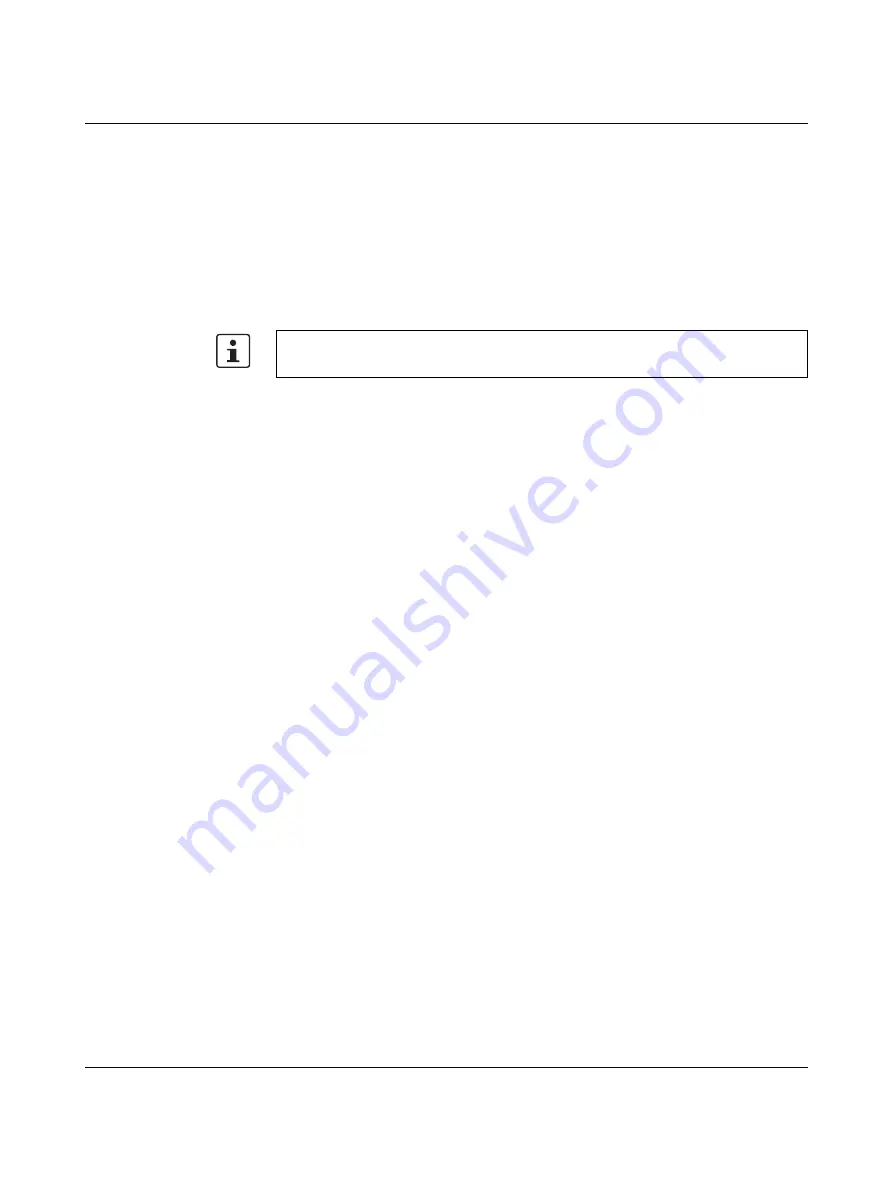
LED status indicators and switching states
108366_en_01
PHOENIX CONTACT
8.1
Recovery in the event of an error
1.
Remove the cause.
2.
Open and close the safety equipment.
If the error is still indicated:
3.
Restart the safety switch:
a)
Disconnect the operating voltage.
b)
Apply the operating voltage again.
If the error cannot be reset, please contact Phoenix Contact.
Perform a function test after every error.